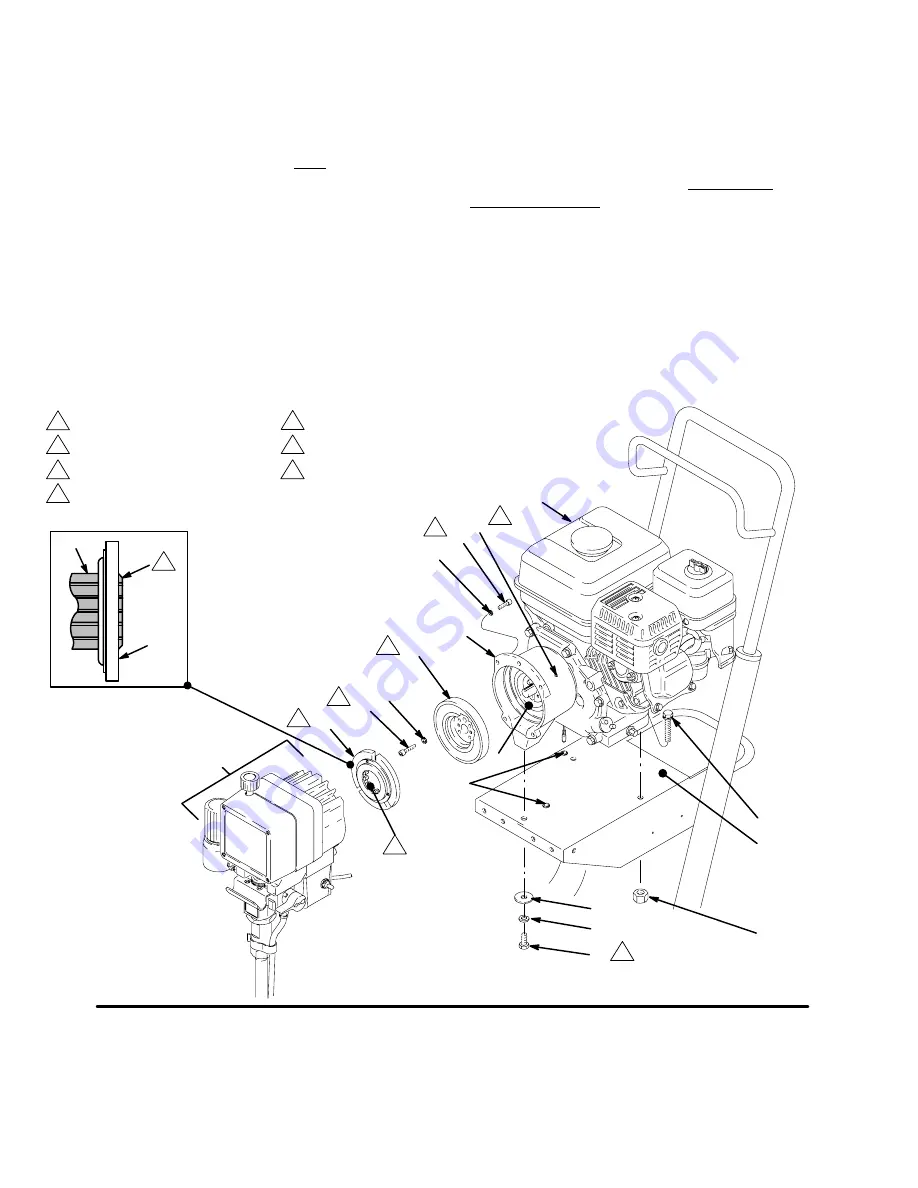
6
308660
Reassembly
NOTE:
With the autogap style armature, the gap be-
tween the rotor and the armature is critical for proper
operation. The clutch kits with an autogap style arma-
ture include a cardboard spacer (p/n 186–857) to set
the proper gap. This spacer is for use
only
during
installation.
1.
Clean the face of the
armature (51b)
. With the flat
side of the armature facing the rotor (51a), slide
the armature onto the hub (2h) in the drive/pinion
assembly (D) just until the chamfered end of the
hub (2h) protrudes through the armature. See
Detail B, Fig. 7. There will be significant resis-
tance. Attach the cardboard spacer, supplied with
the clutch kit, to the face of the armature. Engage
the tabs on the spacer with the slots in the arma-
ture or bend tabs over outside diameter of arma-
ture.
Brace the cart against a wall to keep it from rolling.
Push the drive/pinion assembly onto the clutch
housing (1). There will be significant resistance.
When the mating surfaces of the drive/pinion as-
sembly and the clutch housing (1) are flush, re-
move the drive/pinion assembly.
Remove the
cardboard spacer.
2.
Assemble the
drive assembly (D)
to the clutch
housing (1), using the capscrews (59) and lock-
washers (16). See Fig. 7.
05843A
Fig. 7
A
78
61
51b
16
51a
53
1
48
57
62
58
77
16
59
1
3
4
2
Torque the screw to 7 ft–lb (9.5 N.m).
The face must be clean.
1
2
Spline
4
2
To engine alternator.
Detail B
5
52
2h
D
60
50
Chamfered end of hub (2h)
5
06007
6
Apply low strength thread locker.
7
Torque to 100 in.-lb (N
m).
7
6
6