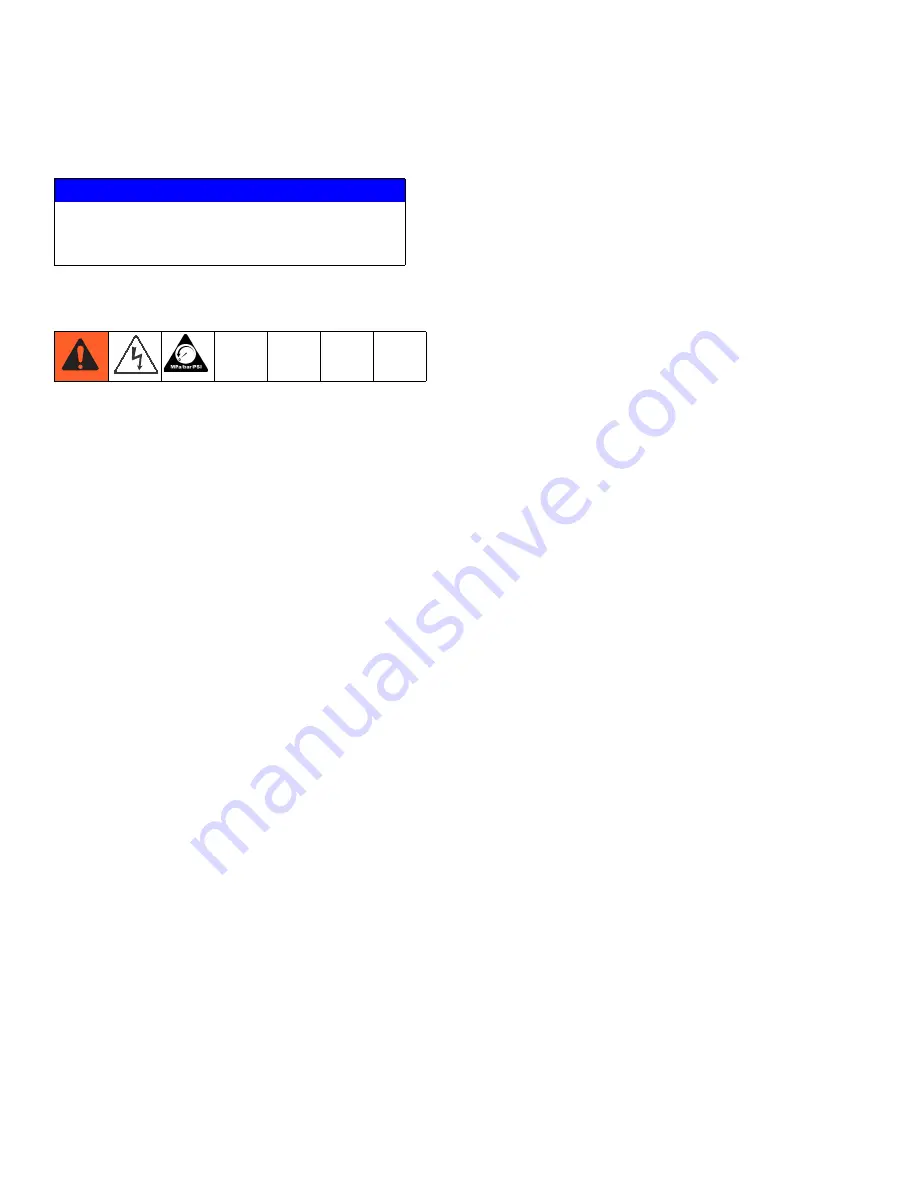
Drive Housing Replacement
20
3A2817A
Drive Housing Replacement
Removal
1.
Relieve pressure, page 9.
2.
Disconnect power cord from outlet.
3.
Remove screws (12) and pump rod cover (70).
4.
Remove pump, Displacement Pump Replacement,
page 17.
5.
Remove screws (12) from shroud (23).
6.
Remove screws (12) from front cover (22).
7.
Remove screws (47).
8.
Pull drive housing (42) off motor (54).
9.
Remove gear cluster (44) and (40) and thrust
washer (25) from drive housing.
Installation
1.
Apply a heavy coat of grease to gears and needle
bearing surfaces.
2.
Install washers (8, 10) on back of gear (40). Install
gear in motor end bell. Using grease for retention,
place washer (10) over bearing inside housing (42).
3.
Install washers (1, 9) on back of gear (44). Install in
motor endbell.
4.
Install thrust washer (25) on gear (44).
5.
Push drive housing (42) on motor endbell as you
guide gear crank (44) through hole in connecting
rod (43).
6.
Install screws (47).
7.
Install cover (22) and screws (12).
8.
Install shroud (23) and screws (12).
9.
Install pump; see Displacement Pump Replace-
ment, page 17.
10. Install pump rod cover (70) with screws (12).
NOTICE
Do not drop gear cluster (44) and (40) when remov-
ing from drive housing (42). Gear cluster may stay
engaged in motor front end bell or drive housing.