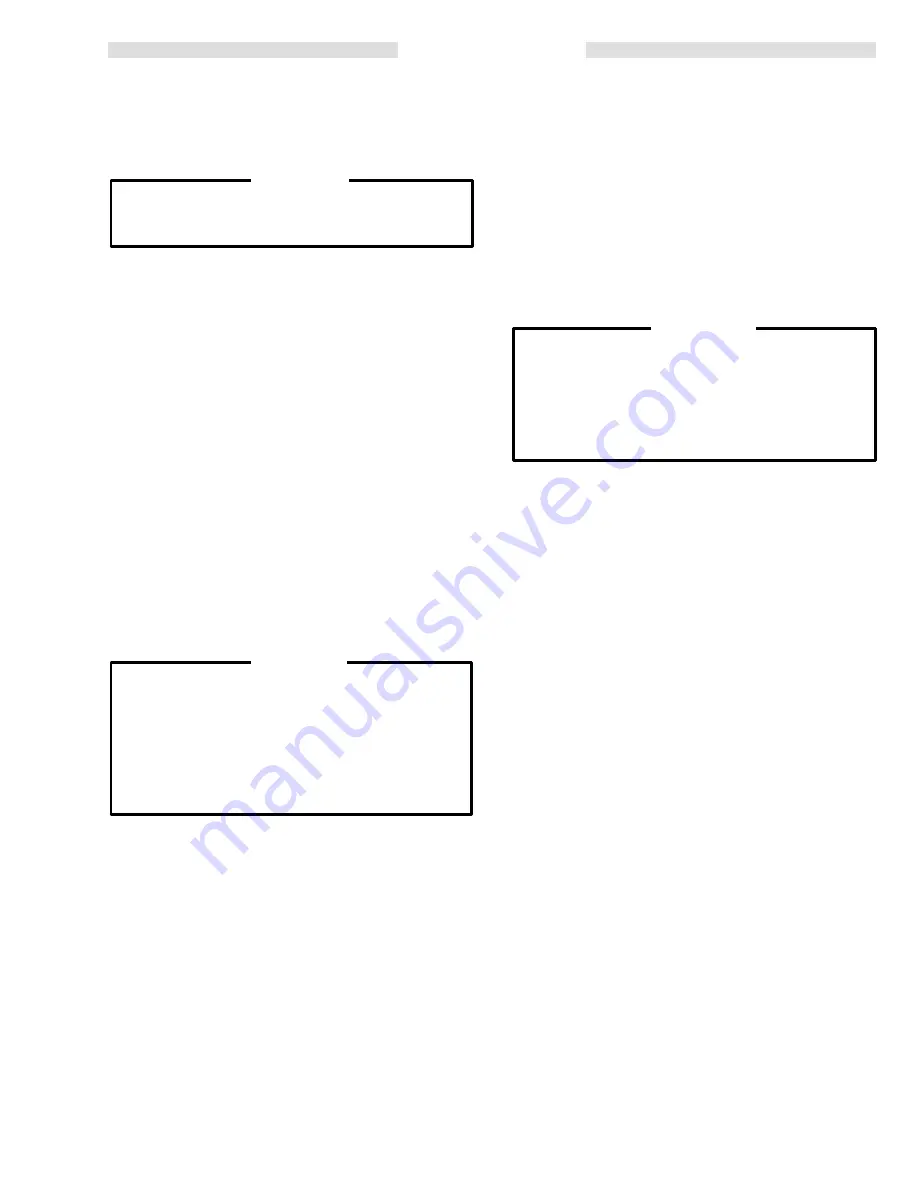
INSTALLATION
Install the Air Line Interlock
Install the air line interlock. Use the u-bolts and brackets
to secure the air line in place. Mount the air manifold to
the safety fence. See Typical Installation.
WARNING
Never tamper with or bypass the air-line interlock
as this could cause electric shock and result in
serious injury.
Connect the Air Lines
1.
Connect the 1/4 in. ID nylon
non-conductive air hose
(N) between the air manifold and the fluid supply.
Refer to the TYPICAL INSTALLATION drawing on
page 4.
2.
Connect the 3/8 in. ID air hose (S) between the main
air supply line and the air manifold air line interlock
fitting.
3.
Connect the 5/16 in. ID air hose (R) between the air
manifold and the voltage control air inlet.
4.
Install a bleed-type air regulator on the fluid supply
unit and gun air supply lines to control air pressure to
the fluid supply unit and gun.
5.
Connect the gun’s
electrically conductive air supply
hose (C) between the air regulator and the gun’s air
inlet. (The gun air inlet fitting has a left hand thread.)
Connect the air supply hose ground cable (Q) to the
strain relief/ground terminal.
WARNING
To reduce the risk of electric shock or other serious
bodily injury, the gun air supply hose must be elec-
trically connected to a true earth ground. Use Only
Graco Electrically Conductive Air Supply
Hose, as specified in the ACCESSORIES section
of this manual. This hose, and the gun, have spe-
cial threads which prevent using any other type of
hose with the gun.
6.
Install an air line filter and an air and water separator
on the air line to ensure a dry, clean air supply to the
gun. Dirt and moisture can ruin the appearance of
your finished workpiece and can cause the gun to
malfunction. A combination air filter/moisture sepa-
rator is shown in the ACCESSORIES section.
7.
Install a bleed-type air shutoff valve on the main air
line and the fluid supply unit line to shut off air to the
fluid supply unit and/or gun(s). Install an additional
bleed-type valve on each fluid supply unit’s air supply
line to relieve air trapped between this valve and the
fluid supply unit after the air regulator is shut off.
WARNING
The
bleed-type air shutoff valve is required in your
system to relieve air trapped between this valve
and the fluid supply unit after the air regulator is
closed. Trapped air can cause the gun to spray
unexpectedly, which could result in serious bodily
injury, including splashing in the eyes or on the skin
and injury from moving parts.
8.
Install an air shutoff valve on each gun air supply line
to shut off air to the gun(s).
Connect the Fluid Line
1.
Install a fluid regulator (E) on the fluid line to control
fluid pressure to the gun.
2.
Install a fluid filter at the fluid supply unit outlet.
3.
Connect the fluid line to the fluid supply unit.
Summary of Contents for PRO 3500WB
Page 11: ... NOTES ...
Page 35: ... NOTES ...