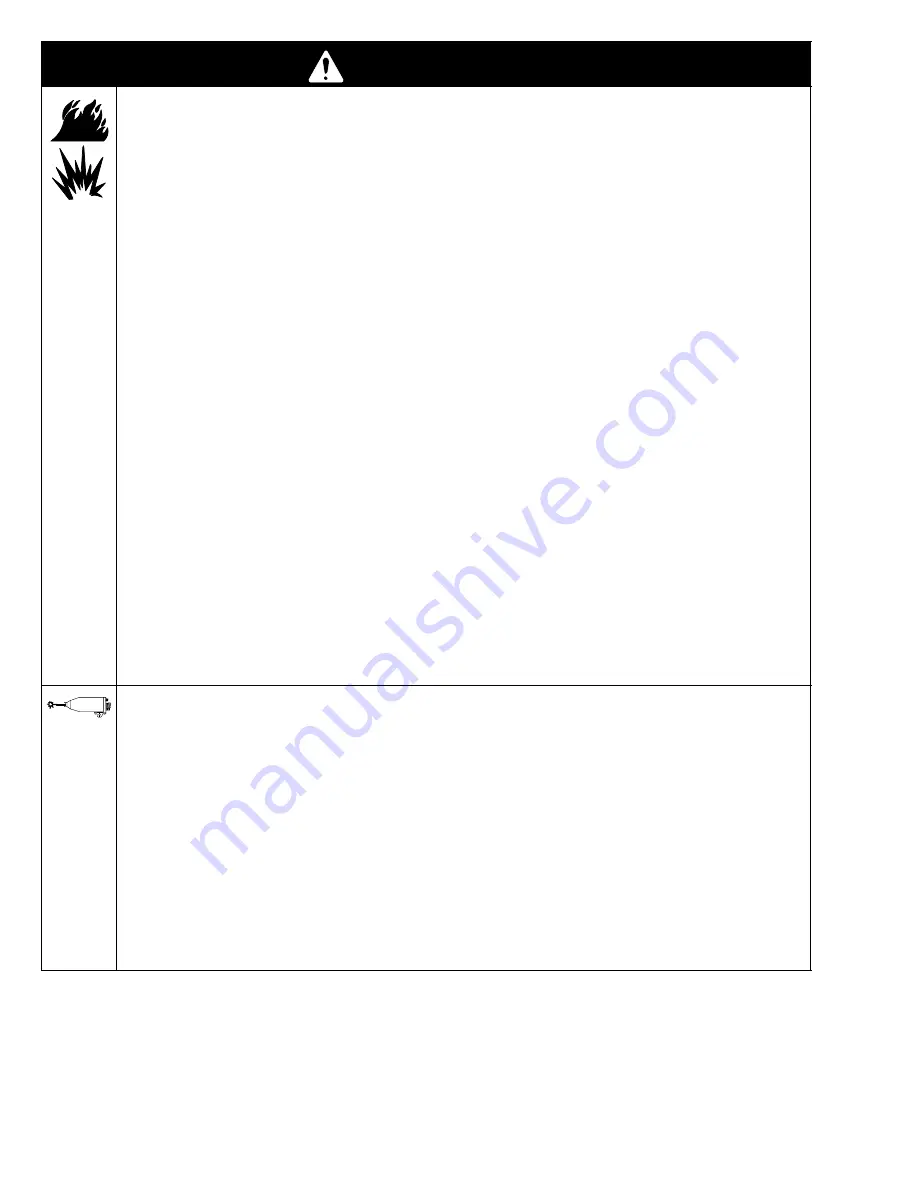
4 308496
WARNING
FIRE AND EXPLOSION HAZARD
Improper grounding, poor air ventilation, open flames, or sparks can cause a hazardous condition and
result in a fire or explosion.
Electrostatic equipment must be used only by trained, qualified personnel who understand the
requirements stated in this instruction manual.
Ground the equipment, personnel in or close to the spray area, the object being sprayed, and all
other electrically conductive objects in the spray area. See Ground the System on page 17.
Test the gun electrical resistance daily as instructed on page 33.
Provide fresh air ventilation to avoid the buildup of toxic vapors. Interlock the gun turbine air supply
to prevent operation of the power supply unless the ventilating fans are on. See Ventilate the
Spray Booth on page 9.
Only use this equipment to spray non-flammable, waterborne fluids, as defined on the front cover
of this manual.
Only flush, purge, or clean the electrostatic, waterborne spray system with non-flammable fluids,
as defined on the front cover of this manual.
Do not flush the system with the gun electrostatics turned on.
Use only non-sparking tools to clean residue from the booth and hangers.
Extinguish all open flames or pilot lights in the spray area.
Keep the spray area free of debris, including solvent, rags, and gasoline.
Do not store any flammable fluids in the spray area.
Do not turn on or off any light switch in the spray area while operating or if fumes are present.
Do not smoke in the spray area.
Do not operate a gasoline engine in the spray area.
PRESSURIZED EQUIPMENT HAZARD
Spray from the gun, hose leaks, or ruptured components can splash fluid in the eyes or on the skin
and cause a serious injury.
Do not point the spray gun at anyone or any part of the body.
Do not stop or deflect fluid leaks with your hand, body, glove, or rag.
Follow the Pressure Relief Procedure on page 19 whenever you: are instructed to relieve the
pressure; stop spraying; clean, check, or servicing the equipment; and install or clean the fluid
nozzles.
Tighten all the fluid connections before each use.
Check the hoses, tubes and couplings daily. Replace worn, damaged, or loose parts immediately.
Permanently coupled hoses cannot be repaired; replace the entire hose.
Warnings are continued on the next page.
Summary of Contents for PRO 5500wb
Page 49: ...308496 49 Notes ...
Page 59: ...308496 59 Notes ...