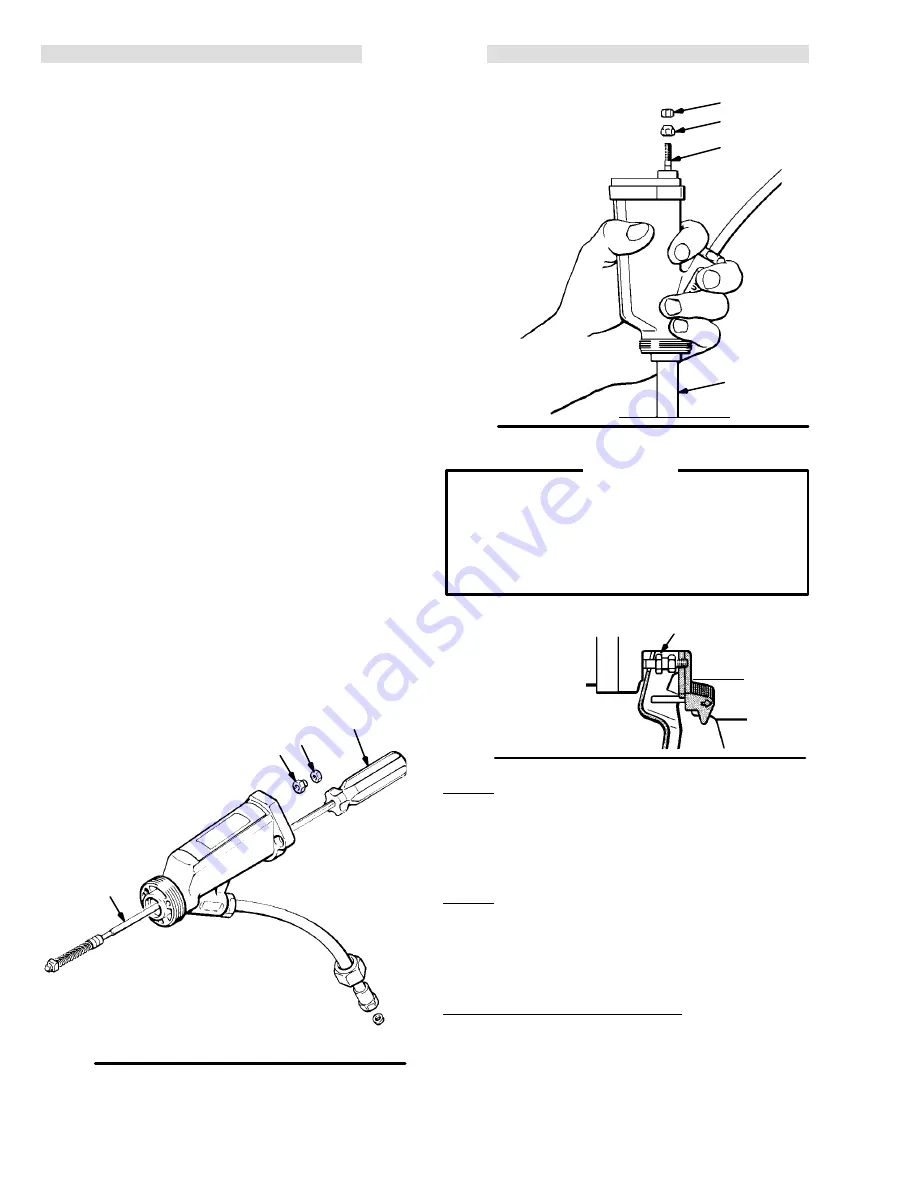
SERVICE
Fluid Needle Replacement
1.
Remove the gun barrel (9) as instructed on page
17. If the power cartridge comes out, carefully press
it back into the handle.
2.
Insert the narrow end of the pressing tool (63c)
through the front of the gun to push the needle back,
then remove the nut (21) and the adjustment nut
(17a). See Fig 17.
3.
Press the needle assembly (17) out the front of
the gun as far as you can with a finger, or by pressing
it against a flat surface. Then use the wrench (63f) to
finish pushing it out. See Fig 16.
4.
Remove the nut (17a) from the new needle
assembly. Then install the new needle assembly
through the front of the gun. Insert the narrow end of
the pressing tool (63c) into the front of the gun and
press to seat the needle. See Fig 17.
5.
Install the new adjustment nut (17a), hex end
first, onto the needle.
6.
Use the pressing tool (63c) to press on the
needle from the front of the gun, then screw the
adjusting nut (17a) all the way to the bottom of the
threads. Remove the pressing tool.
7.
Screw the other nut (21) firmly against the
adjustment nut to lock them together.
8.
Reassemble the gun as described in Barrel
Reassembly.
Fig 16
KEY
17
Needle Assembly
17a
Adjustment Nut
21
Nut
63f
Wrench
21
17a
17
63f
Fig 17
KEY
17a
Adjustment Nut
21
Nut
63c
Pressing Tool
21
17a
63c
Bottom of
thread
Check the Gun Safety Latch
WARNING
Check to be sure the gun safety latch works prop-
erly each time after you change the needle.
Safety
latch failure or improper use of the safety latch can
result in accidental gun triggering, which could
cause fluid injection or splashing fluid into the eyes
or on skin and result in serious injury.
Fig 18
17a
Trigger MUST NOT
touch nut (17a) when
safety latch is locked.
SPRAY
LOCK
TEST 1
Engage the trigger safety latch to the right, then try to trig-
ger the gun. Look behind the trigger to be sure it is
not
engaging the nut (17a). Then engage the latch to the left
and check again. See Fig 18.
TEST 2
Disengage the trigger safety latch, and trigger the gun
gently to see if you can feel the “lead and lag” operation,
which means the air will come on before the fluid does,
and the fluid shuts off before the air does.
If the gun fails either TEST 1 or 2:
Remove the trigger and the ball seat housing. Back the
nuts
(17a, 21) away from the bottom of the threads.
Reassemble and check Tests 1 and 2 again. Also check
in front of the trigger to make sure the needle still moves.
If the trigger still fails any of these tests now, the needle
assembly (17) is out of tolerance and must be replaced.
Summary of Contents for PRO AA4000
Page 2: ... ...