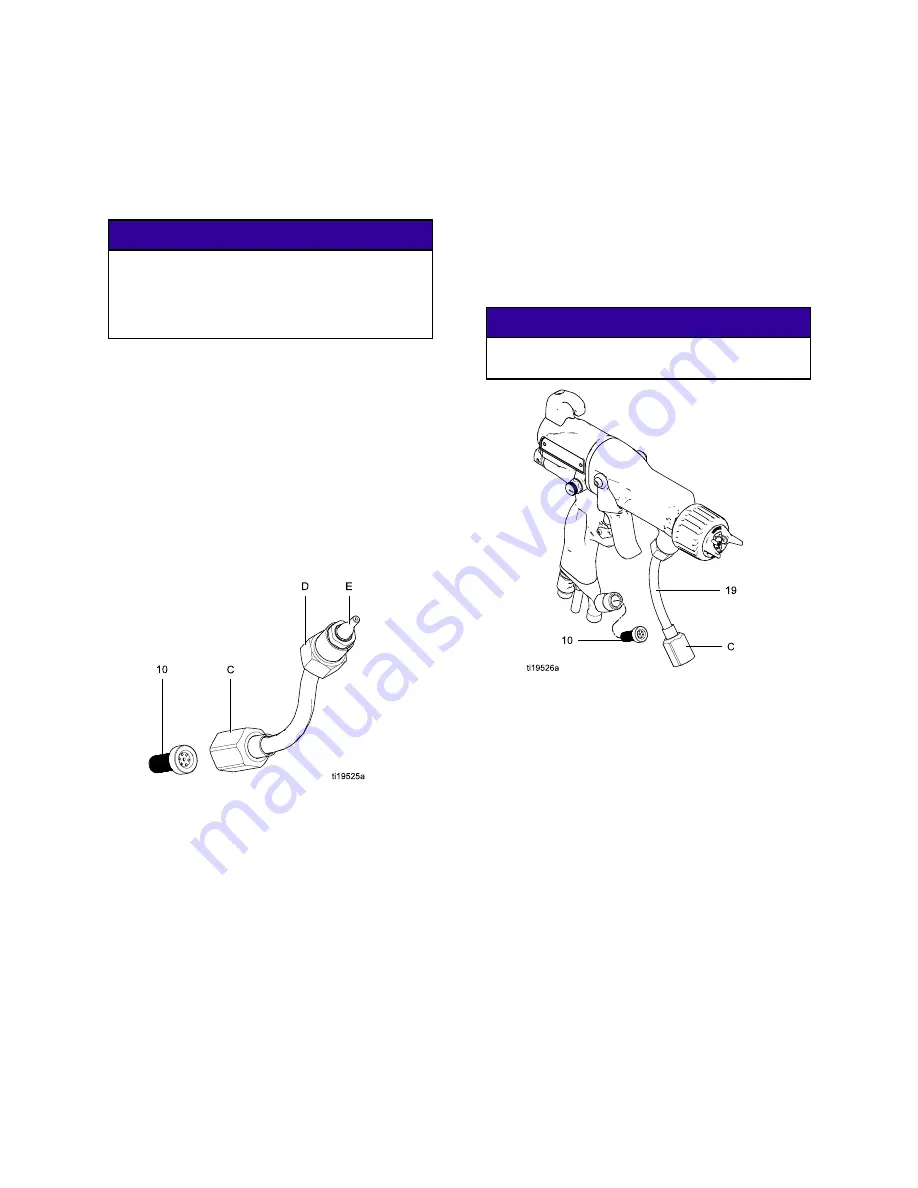
Fluid
Fluid
Fluid Tube
Tube
Tube Removal
Removal
Removal and
and
and Replacement
Replacement
Replacement
1.
See
Prepare the Gun for Service, page 39
.
2.
Disconnect the bottom fluid tube nut (C).
3.
Carefully unscrew the top fluid tube nut (D).
NOTICE
NOTICE
NOTICE
Be careful not to damage the fluid tube
assembly (19) when cleaning or installing
it, especially the sealing surface (E). If the
sealing surface is damaged, the entire fluid
tube assembly must be replaced.
4.
Apply dielectric grease (57) to the entire length of
the plastic extension on the fluid tube.
5.
Apply low strength sealant to the fluid tube nut
threads.
6.
Install the fluid tube into the gun barrel and
tighten the top nut (D) until snug, then 1/2 turn
tighter. There will be a gap between the nut and
barrel. Do not over-tighten the nut.
7.
Make sure the fluid filter (10) is in place in the
fluid fitting. Tighten the bottom nut (C) securely
onto the fitting. Make sure the top nut remains
tight.
Figure 25 Fluid Tube
Fluid
Fluid
Fluid Filter
Filter
Filter Replacement
Replacement
Replacement
1.
See
Prepare the Gun for Service, page 39
.
2.
Disconnect the bottom fluid tube nut (C).
3.
Remove the fluid filter (10) from the fluid fitting.
Clean or replace the filter, as needed.
4.
Install the fluid filter (10) in the fluid fitting. Tighten
the bottom nut (C) onto the fitting and torque to
140–150 in-lb (15.8–16.9 N•m). Make sure the
top nut remains tight at 20–30 in-lb (2.3–3.4 N•m).
NOTICE
NOTICE
NOTICE
Be sure the fluid tube (19) is not twisted after
tightening the bottom nut (C).
Figure 26 Replace Fluid Filter
42
3A2495K