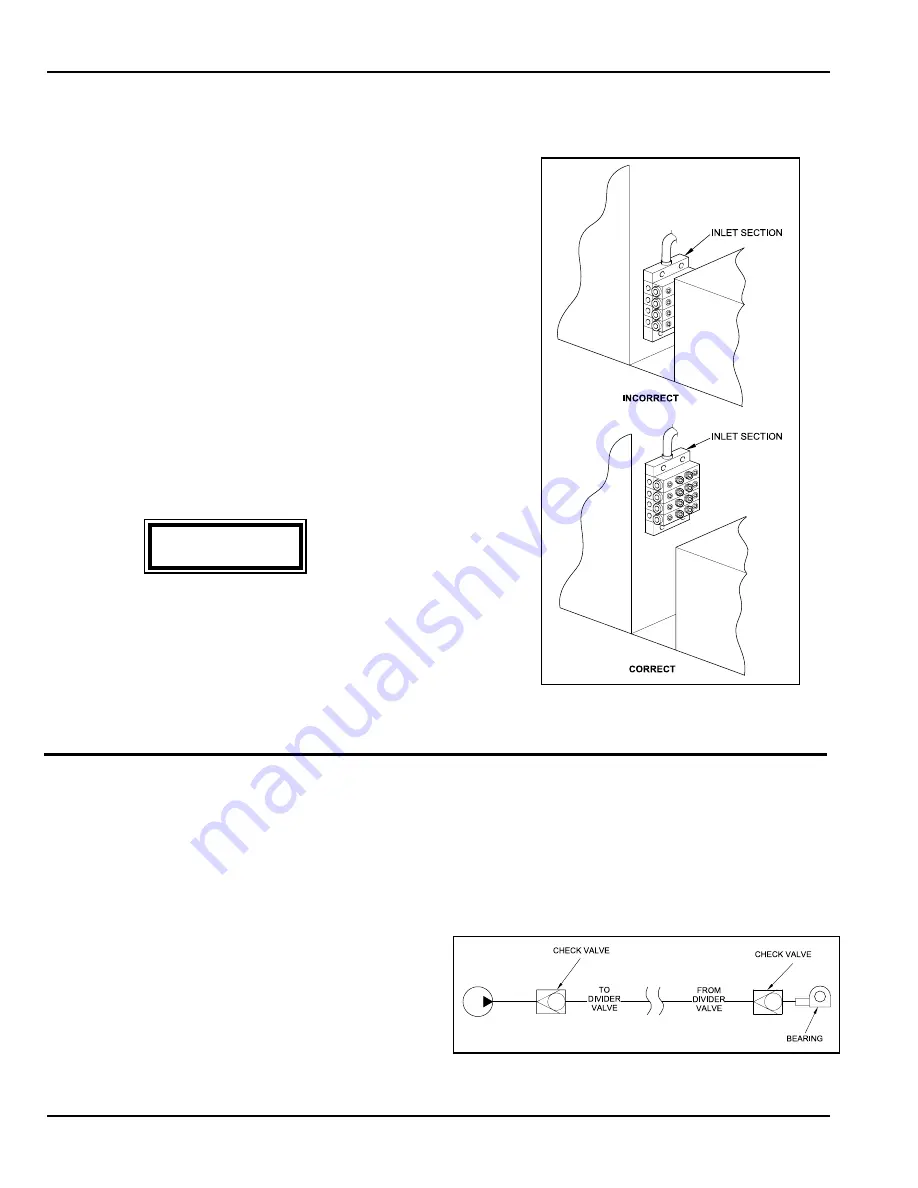
Series Progressive Lubrication Systems Installation Guide
L40000
Page 5
MOUNTING DIVIDER VALVES
(continued)
Avoid locating the divider valve assembly in locations that
•
restrict access to it. The ports on the front of the divider
valves should be acces sible for prefilling and purging
procedures (see Figure 5).
The inlet and end sections of each divider valve have two
holes each to enable the installer to attach it to an appropriate
surface with properly-sized bolts. The valves may be attached
directly to one of the machine surfaces if the surface can be
drilled and tapped, but the mounting surface should be flat in
order to prevent the divider valve from being deformed. Other
mounting variations may require the use of a mounting plate
interface. Graco has several styles of mounting plates available
for straightforward installations. Also, a customized design
can be developed for those installations that require special
considerations and hardware.
CAUTION
If a weld-in-place mounting plate is be ing installed, the plate
should be welded in place prior to mounting the divider valve
assembly in order to pre vent damage to the internal 0-rings by
heat generated during the welding op eration.
Figure 5
be placed as close as possible to the final lubrication point (see
Figure 6). This prevents drainage of lubricant from the lube
lines should disassembly be required. However, systems using
grease as the lubricant may not experience lubricant self-flow
when com ponents are removed and, therefore, may not require
lube point check valves.
INSTALLING CHECK VALVES
After the divider valves have been located, the check valves
should be installed with each one oriented so that it faces
toward the particular divid er valve outlet port that supplies it
with lubricant. This helps to determine the minimum length of
connecting tubing or hose.
There are several locations within any lubrication system that
benefit from the use of a check valve, including the outlet of
the pump and the ends of all lube lines. The check valve should
Figure 6