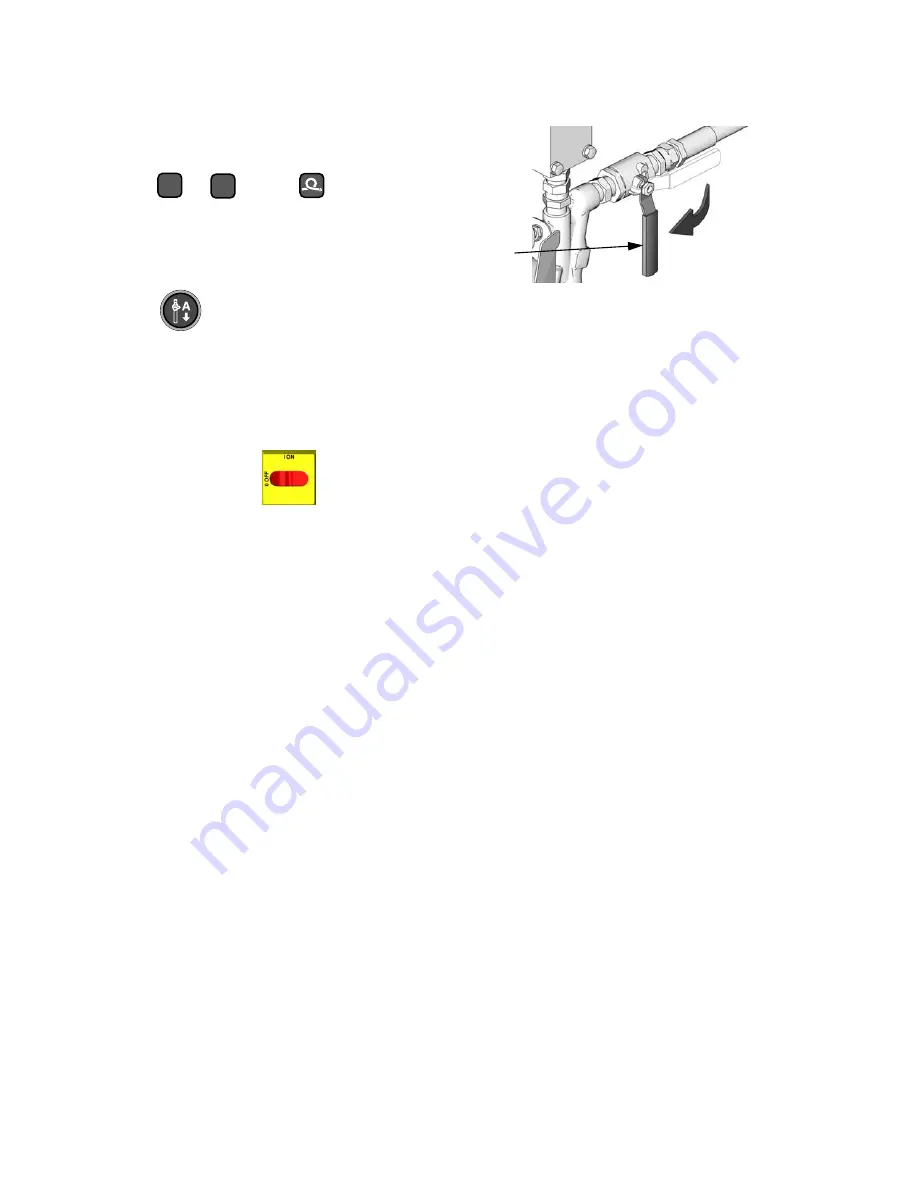
Shutdown
34
Shutdown
1. Shut off
,
, and
heat
zones.
2. Park pumps.
a. Press
.
b. Trigger gun until pump A stops in the
retracted position and the pressure of
both pumps bleeds down.
3. Turn main power OFF
.
4. Close both fluid supply valves (FV).
5. Relieve pressure, page 35.
6. Shut down feed pumps as required.
A
B
ti9883a
FV