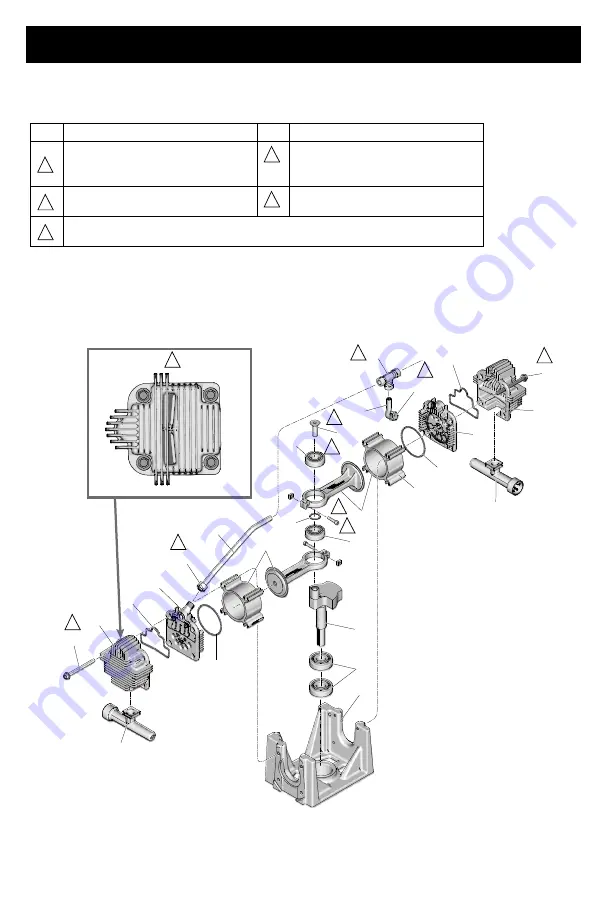
Compressor Assembly Parts
3A3265A
29
Compressor Assembly Parts
Ref.
Torque
Ref.
Torque
Piston retaining bolt and crankshaft
bolts must torqued before head
bolts (14) are torqued.
165-185 ft-lb (18.6 - 20.9 N•m)
50-65 in-lb (5.7 - 7.3 N•m)
Hand tighten then one additional full
turn.
120-140 in-lb (13.6 - 15.8 N•m) Finger tighten cap screw in position 4 first then
torque cap screws in the sequence illustrated.
3
7
5
8
6
3
1
2
4
5
6
4
5
7
8
10
10
12
12
14
14
13
13
9
9
11
11
15
15
19
20
21
ti27981a
4
2
1
3
3
5
6
7
3
8
8
8
Torque Sequence
6
6