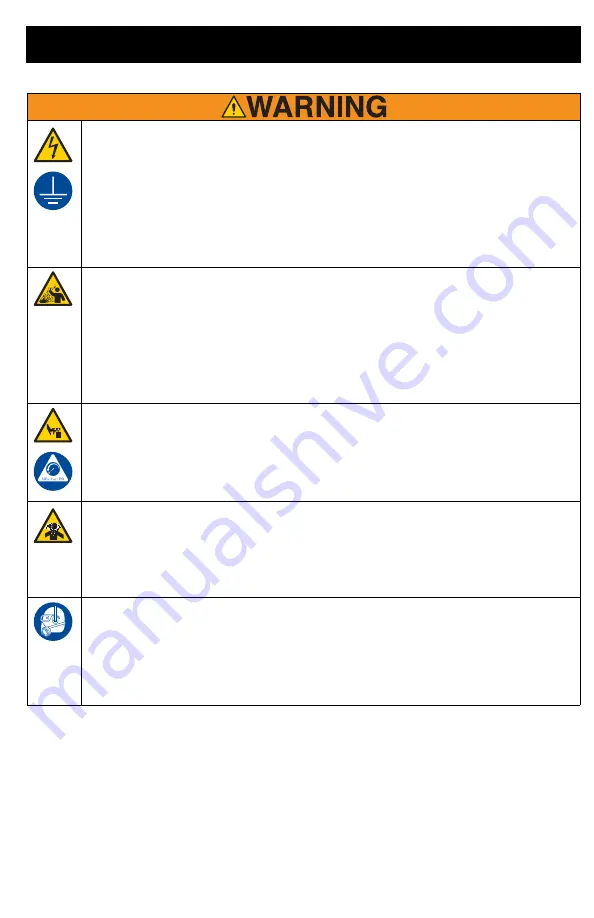
Warnings
3A6491E
7
ELECTRIC SHOCK HAZARD
This equipment must be grounded. Improper grounding, setup, or usage of the system can
cause electric shock.
•
Turn off and disconnect power cord before servicing equipment.
•
Connect only to grounded electrical outlets.
•
Use only 3-wire extension cords.
•
Ensure ground prongs are intact on power and extension cords.
•
Do not expose to rain. Store indoors.
•
Wait five minutes after disconnecting power cord before servicing.
PRESSURIZED ALUMINUM PARTS HAZARD
Use of fluids that are incompatible with aluminum in pressurized equipment can cause serious
chemical reaction and equipment rupture. Failure to follow this warning can result in death,
serious injury, or property damage.
•
Do not use 1,1,1-trichloroethane, methylene chloride, other halogenated hydrocarbon
solvents or fluids containing such solvents.
•
Do not use chlorine bleach.
•
Many other fluids may contain chemicals that can react with aluminum. Contact your
material supplier for compatibility.
MOVING PARTS HAZARD
Moving parts can pinch, cut or amputate fingers and other body parts.
•
Keep clear of moving parts.
•
Do not operate equipment with protective guards or covers removed.
•
Equipment can start without warning. Before checking, moving, or servicing equipment,
follow the
Pressure Relief Procedure
and disconnect all power sources.
TOXIC FLUID OR FUMES HAZARD
Toxic fluids or fumes can cause serious injury or death if splashed in the eyes or on skin,
inhaled, or swallowed.
•
Read Safety Data Sheets (SDSs) to know the specific hazards of the fluids you are using.
•
Store hazardous fluid in approved containers, and dispose of it according to applicable
guidelines.
PERSONAL PROTECTIVE EQUIPMENT
Wear appropriate protective equipment when in the work area to help prevent serious injury,
including eye injury, hearing loss, inhalation of toxic fumes, and burns. This protective
equipment includes but is not limited to:
•
Protective eyewear, and hearing protection.
•
Respirators, protective clothing, and gloves as recommended by the fluid and solvent
manufacturer.
Summary of Contents for ST MAX II 395 PC Pro
Page 35: ...Troubleshooting 3A6491E 35 Electrical cont Sprayer Will Not Run See following page for steps ...
Page 36: ...Troubleshooting 36 3A6491E ...
Page 49: ...Notes 3A6491E 49 Notes ...
Page 52: ...Battery Replacement 52 3A6491E Battery Replacement BlueLink Units Only ...
Page 53: ...Wiring Diagrams 3A6491E 53 Wiring Diagrams 110 120V Models 395EU 490 495 595 ...
Page 55: ...Wiring Diagrams 3A6491E 55 120V 110V Model 650 ...
Page 57: ...Notes 3A6491E 57 Notes ...
Page 63: ...Graco Information 3A6491E 63 ...