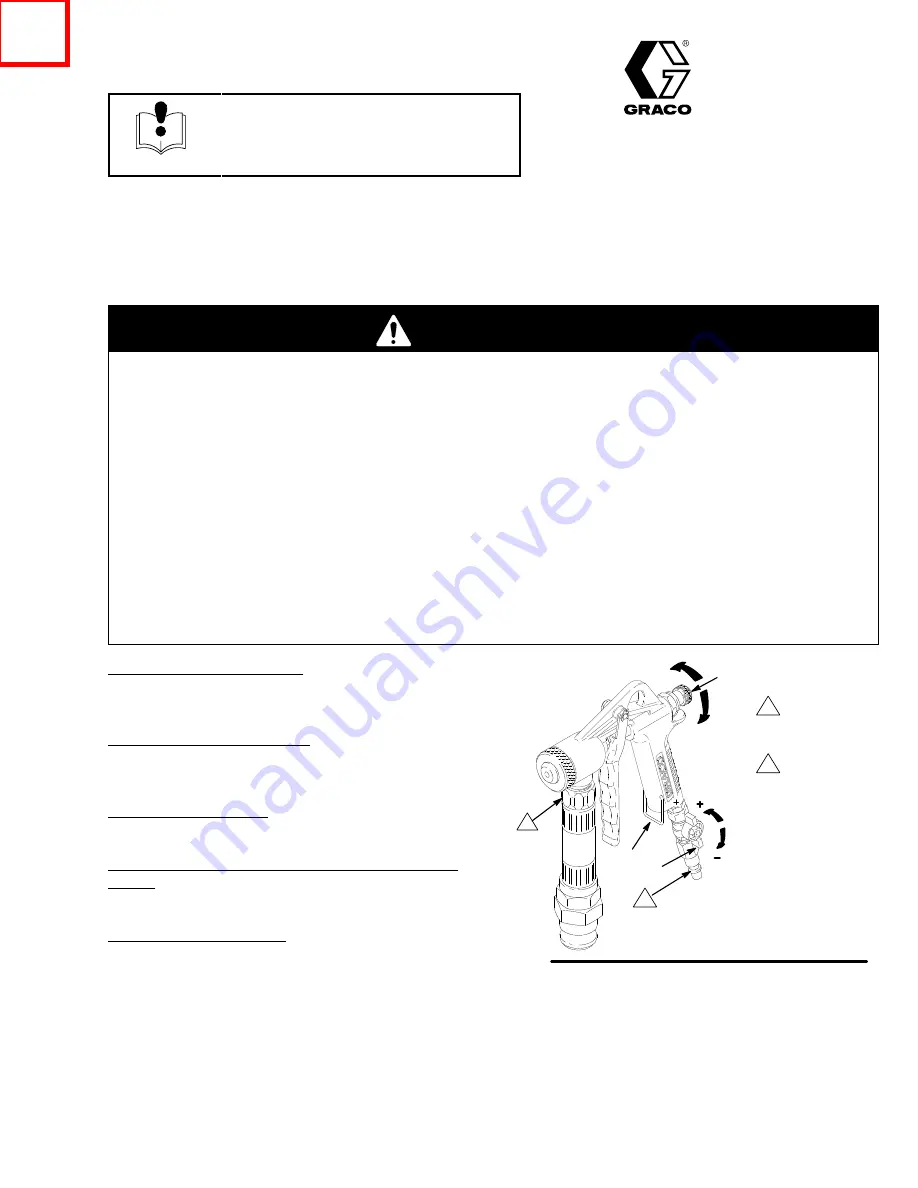
308–878
Rev. A
INSTRUCTIONS-PARTS LIST
INSTRUCTIONS
This manual contains important
warnings and information.
READ AND KEEP FOR REFERENCE.
TEXTURE SPRAY GUN
100 psi (7 bar) Maximum Air and Fluid Working Pressure
Model 240–786, Series A; Model 240–787, Series A
WARNING
Pressure Relief Procedure
To reduce the risk of serious bodily injury, including
electric shock and splashing fluid in the eyes, follow this
procedure whenever you stop spraying.
1.
Shut off the pump or sprayer.
2.
Trigger the gun.
3.
Open the gun air valve.
4.
Disconnect the power source.
Grounding
To reduce the risk of electric shock, proper electrical
grounding is essential. See your separate pump or
sprayer instruction manual, and consult your local
electrical codes for detailed grounding instructions.
Working Pressure
To reduce the risk of component rupture and serious
bodily injury, never exceed
100 psi (7 bar) AIR OR
FLUID WORKING PRESSURE to this gun. Do not
exceed the maximum working pressure of any other
component in the system.
Fluid and Solvent Compatibility
Do not use 1,1,1-trichloroethane, methylene chloride,
other halogenated hydrocarbon solvents or fluids con-
taining such solvents in this equipment, which contains
aluminum and/or zinc parts. Such use could result in a
serious chemical reaction, with the possibility of explo-
sion, which could cause death, serious bodily injury
and/or substantial property damage.
The standard gun adjustment is to adjust the material
flow knob (18) so only 1 or 2 threads are visible and
fully open the air valve (23).
Air bleeds from the gun nozzle when the gun air valve
(23) is open. Close the valve to stop the air, if desired.
Otherwise, it can stay open except during priming.
For continuous spraying, use the trigger bail (1) to hold
the trigger open to reduce fatigue.
To prevent material surge at the beginning of a spray
pattern, squeeze the trigger slowly to the fully triggered
position while moving the gun quickly.
Adjusting the spray pattern requires testing to balance
the pump pressure and the air to the gun, and using
the right tip size.
1.
Turn off air valve (23). Adjust the pump pressure
until the material stream is about 8 in. (203 mm)
long. Turn on air valve (23).
2.
Test the spray pattern on cardboard. Spray 18–30
in. (457–762 mm) from the surface.
23
Fig. 1
18
IN
OUT
1
Fluid inlet
special
threads
Air inlet
1/4 npsm
8416A
3.
Adjust the pump and the gun air valve (23) to
achieve a uniform, round spray pattern.
4.
Consider the size of aggregate in the material and
the coarseness of the spray pattern. Remember,
the larger the tip, the heavier the pattern.
5.
Overlap each stroke 50%.
GRACO INC.
P.O. BOX 1441
MINNEAPOLIS, MN
55440–1441
COPYRIGHT 1998, GRACO INC.
Graco Inc. is registered to I.S. EN ISO 9001