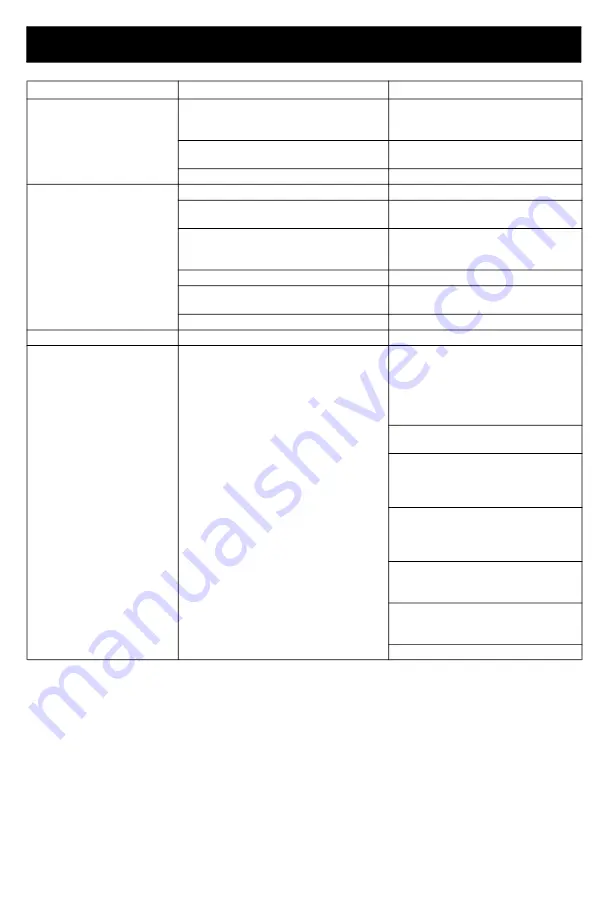
Troubleshooting
3A9014A
27
Sprayer makes no sound
when Trigger is pulled
Power supply
Make certain the sprayer is
plugged into a grounded and
functional power source.
Motor has overheated
Wait 20-30 minutes for motor to
cool.
Electronic control failure
Replace electronic control.
Sprayer sprays with poor
results
Spray Tip is partially clogged
Spray Tip is not in correct position See
Incorrect Spray Tip for application
of material
Install a different size Spray Tip.
Spray Tip is worn or damaged
Replace Spray Tip.
Material being sprayed is aerated
and full of bubbles
Let material settle or change to
different material.
Material being sprayed is too cold Warm material.
Paint leaks from sprayer Pump has reached its maximum life Replace pump.
Paint leaks out of the cup
threads
Cup not properly seated
Verify Cup Lid is tight. An under
tightened Cup Lid will allow air to
seep into the FlexLiner and
cause a loss of prime. Add Seal
Lube (included) to the Cup Lid
gasket to ensure an airtight seal.
Make certain there is only one
FlexLiner in the Cup Support.
Make certain there is no damage
to or debris on the top sealing
edge of the FlexLiner or Cup Lid
gasket.
Make certain the Cup Lid is
properly threaded to the Cup
Support. There should be no
threads visible when tight.
Avoid flexing or pushing on the
Cup Support when you evacuate
the air out of the FlexLiner.
Avoid pulling down on the
FlexLiner when you evacuate the
air out of the FlexLiner.
Replace FlexLiner.
Problem
Cause
Solution