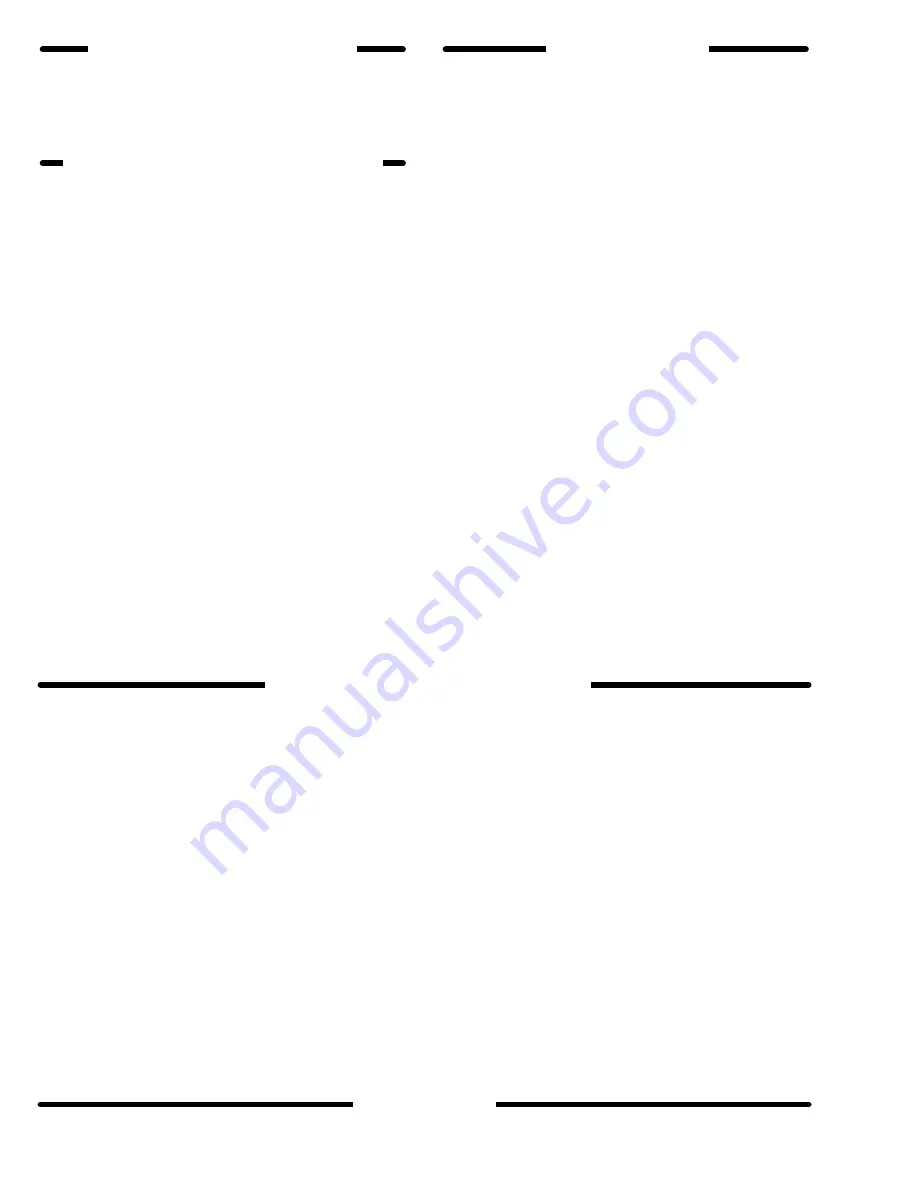
4
308-319
MOVING PARTS HAZARD
Moving parts can pinch or amputate your fingers or other
body parts. KEEP CLEAR of moving parts when starting or
operating the sprayer. Follow the
Pressure Relief Proce-
dure
on page 3 before checking or servicing any part of the
sprayer, to prevent it from starting accidentally.
EQUIPMENT MISUSE HAZARD
General Safety
Any misuse of the spray equipment or accessories, such as
overpressurizing, modifying parts, using incompatible chemi-
cals and fluids, or using worn or damaged parts, can cause
them to rupture and result in fluid injection, splashing in the
eyes or on the skin, or other serious bodily injury, or fire, ex-
plosion or property damage.
NEVER alter or modify any part of this equipment; doing so
could cause it to malfunction.
CHECK all spray equipment regularly and repair or replace
worn or damaged parts immediately.
Always wear protective eyewear, gloves, clothing and respi-
rator as recommended by the fluid and solvent manufacturer.
System Pressure
This sprayer can develop
195 bar (2750 psi)
maximum
working pressure
.
Be sure that all spray equipment and ac-
cessories used are rated to withstand this pressure. DO NOT
exceed the maximum working pressure of any component or
accessory used in the system.
Fluid and Solvent Compatibility
BE SURE that all fluids and solvents used are chemically
compatible with the wetted parts shown in the
TECHNICAL
DATA
on page 39. Always read the fluid and solvent manu-
facturer’s literature before using them in this sprayer.
Do not use 1,1,1-trichloroethane, methylene chloride, other
halogenated hydrocarbon solvents or fluids containing such
solvents in this equipment, which contains aluminum and/or
zinc parts. Such use could result in a serious chemical reac-
tion, with the possibility of explosion, which could cause death,
serious bodily injury and/or substantial property damage.
HOSE SAFETY
High pressure fluid in the hoses can be very dangerous. If the
hose develops a leak, split or rupture due to any kind of wear,
damage or misuse, the high pressure spray emitted from it
can cause a fluid injection injury or other serious bodily injury
or property damage.
All fluid hoses must have spring guards on both ends!
Spring guards help protect the hose from kinks or bends at or
close to the coupling which can result in hose rupture.
TIGHTEN all fluid connections securely before each use.
High pressure fluid can dislodge a loose coupling or allow
high pressure spray to be emitted from the coupling.
NEVER use a damaged hose. Before each use, check the
entire hose for cuts, leaks, abrasion, bulging cover, or damage
or movement of the hose couplings. If any of these conditions
exist, replace the hose immediately. DO NOT try to recouple
high pressure hose or mend it with tape or any other device. A
repaired hose cannot contain the high pressure fluid.
Handle and route hoses carefully. Do not pull on hoses to
move equipment. Keep hoses clear of moving parts and hot
surfaces of the pump and gas engine. Do not use fluids or
solvents which are not compatible with the inner tube and
cover of the hose. DO NOT expose Graco hose to tempera-
tures above 180
F (82
C) or below –40
F (–40
C).
Hose Grounding Continuity
Proper hose grounding continuity is essential to maintaining a
grounded spray system. Check the electrical resistance of
your fluid hoses at least once a week. If your hose does not
have a tag on it which specifies the maximum electrical resis-
tance, contact the hose supplier or manufacturer for the maxi-
mum resistance limits. Use a resistance meter in the appro-
priate range for your hose to check the resistance. If the
resistance exceeds the recommended limits, replace it imme-
diately. An ungrounded or poorly grounded hose can make
your system hazardous. Also read
FIRE OR EXPLOSION
HAZARD.
FIRE OR EXPLOSION HAZARD
Static electricity is created by the flow of fluid through the
pump and hose. If every part of the spray equipment is not
properly grounded, sparking may occur, and the system may
become hazardous. Sparking may also occur when plugging
in or unplugging a power supply cord. Sparks can ignite
fumes from solvents and the fluid being sprayed, dust parti-
cles and other flammable substances, whether you are
spraying indoors or outdoors, and can cause a fire or explo-
sion and serious bodily injury and property damage. Plug the
sprayer into a grounded outlet at least 20 ft. (6 m) from the
sprayer.
If you experience any static sparking or even a slight shock
while using this equipment,
stop spraying immediately
.
Check the entire system for proper grounding. Do not use the
system again until the problem has been identified and cor-
rected.
Grounding
To reduce the risk of static sparking, ground the sprayer and
all other spray equipment used or located in the spray area.
CHECK your local electrical code for detailed grounding in-
structions for your area and type of equipment. BE SURE to
ground all of this spray equipment:
1.
Sprayer: plug into a properly grounded outlet. Do not use
an adapter. Extension cords must have three wires and
be rated for at least 15 amps.
2.
Fluid hoses: use only grounded hoses with a maximum of
500 ft (150 m) combined hose length to ensure grounding
continuity. See
Hose Grounding Continuity
.
3.
Spray gun: obtain grounding through connection to a
properly grounded fluid hose and sprayer.
4.
Object being sprayed: according to local code.
5.
Fluid supply container: according to local code.
6.
All solvent pails used when flushing, according to local
code. Use only metal pails, which are conductive. Do not
place the pail on a non–conductive surface, such as pa-
per or cardboard, which interrupts the grounding continu-
ity.
7.
To maintain grounding continuity when flushing or reliev-
ing pressure, always hold a metal part of the gun firmly to
the side of a grounded metal pail, then trigger the gun.
Flushing Safety
Reduce the risk of fluid injection injury, static sparking, or
splashing by following the flushing procedure given on page
15 of this manual. Follow the
Pressure Relief Procedure
on
page 3, and remove the spray tip before flushing. Hold a
metal part of the gun firmly to the side of a grounded metal pail
and use the lowest possible fluid pressure during flushing.
IMPORTANT
United States Government safety standards have been adopted under the Occupational Safety and Health Act. These standards
– particularly the General Standards, Part 1910, and the Construction Standards, Part 1926 – should be consulted.