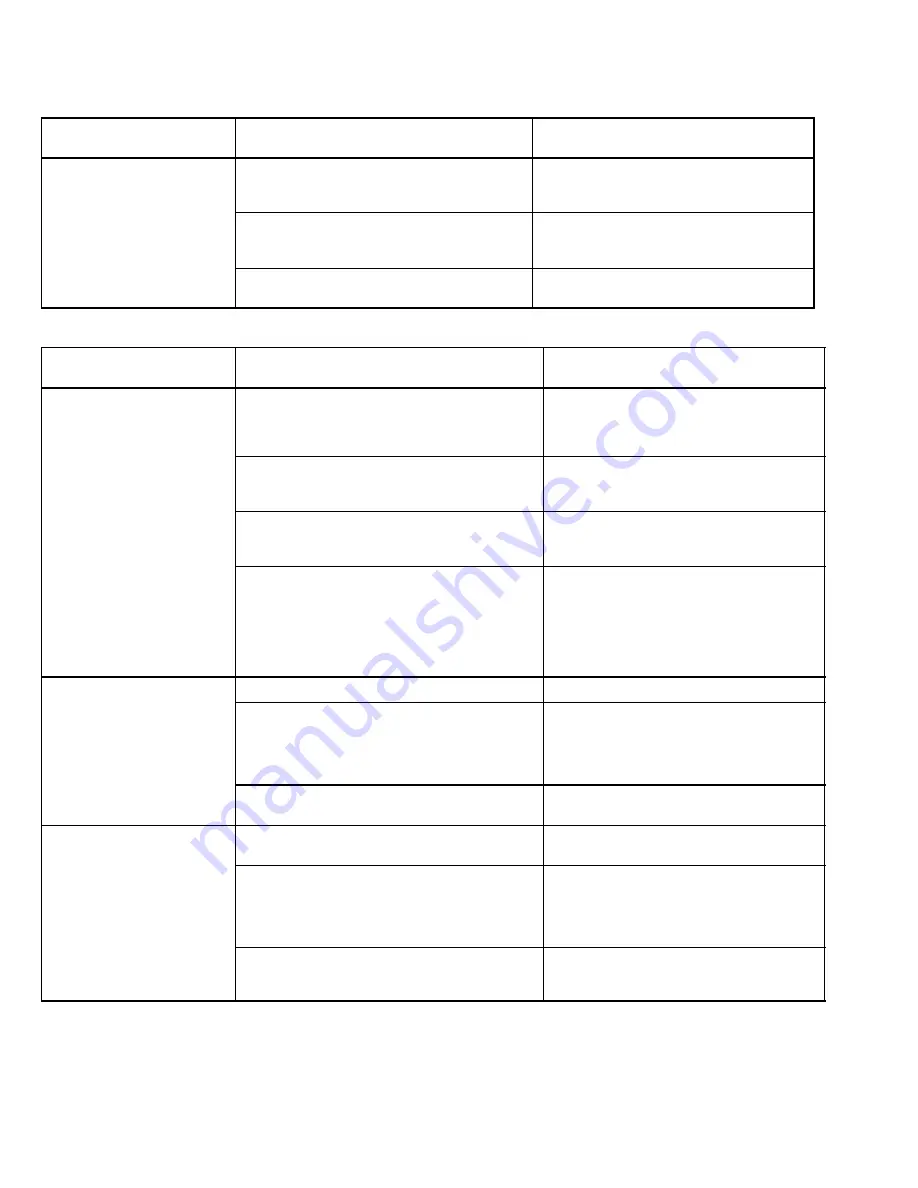
8
308842
Troubleshooting
MOTOR IS HOT AND RUNS INTERMITTENTLY
TYPE OF PROBLEM
WHAT TO CHECK
If check is OK, go to next check
WHAT TO DO
When check is not OK refer to this column
Motor is hot and runs intermit-
tently.
1. Determine if sprayer was operated at high
pressure with small tips, which causes low
motor RPM and excessive heat build up.
1. Decrease pressure setting or increase tip
size.
2. Be sure ambient temperature where sprayer
is located is no more than 90
F and sprayer
is not located in direct sun.
2. Move sprayer to shaded, cooler area if pos-
sible.
3. Determine if sprayer was turned on, pressur-
ized, but not operating for long periods of time.
3 Turn off sprayer whenever you stop spray-
ing for a while and relieve fluid pressure.
ELECTRICAL SHORT
TYPE OF PROBLEM
WHAT TO CHECK
If check is OK, go to next check
WHAT TO DO
When check is not OK refer to this column
Building circuit breaker opens
as soon as sprayer switch is
turned on.
1. All electrical wiring for damaged insulation, and
all terminals for loose fit or damage. Also wires
between pressure control and motor. See page
16.
1. Repair or replace any damaged wiring or
terminals. Securely reconnect all wires.
2. For missing inspection plate gasket (see page
16), bent terminal forks or other metal to metal
contact points which could cause a short.
2. Correct faulty conditions.
3. Motor armature for shorts. Use an armature
tester (growler) or perform spin test. See page
9. Inspect windings for burns.
3. Replace motor. See page 16.
4. Motor control board (104) by performing motor
control board diagnostics on page 12. If diag-
nostics indicate, substitute with a good board.
CAUTION:
Do not perform this check until mo-
tor armature is determined to be good. A bad
motor armature can burn out a good board.
4. Replace with a new pressure control board
(104). See page 12.
1. Basic Electrical Problems on page 4.
1. Perform necessary procedures.
2. ON/OFF switch (80) See page 11.
Be sure
sprayer is unplugged!
Disconnect wires from
switch. Check switch with ohmmeter. Reading
must be infinity with ON/OFF switch OFF, and
zero with switch ON.
2. Replace ON/OFF switch. See page 11.
3. For damaged or pinched wires in pressure con-
trol. See page 12.
3. Replace damaged parts. See page 12.
Sprayer quits after sprayer op-
erates for 5 to 10 minutes.
1. Basic Electrical Problems on page 4.
1. Perform necessary procedures.
2. Electrical supply with volt meter.
Meter must read:
210–250 VAC for models 232144, 145, 154.
100–120 VAC for models 232148, 158.
90–110 VAC for models 232156, 157.
2. If voltage is too high, do not operate
sprayer until corrected.
3. Tightness of pump packing nut. Over tightening
tightens packings on rod, restricts pump action,
and damages packings.
3. Loosen packing nut. Check for leaking
around throat. Replace pump packings, if
necessary. See page 17.
.
CAUTION
Any short in any part of the
motor power circuit will cause
the control circuit to inhibit
sprayer operation. Correctly
diagnose and repair all shorts
before checking and replac-
ing control board.
Building circuit breaker opens
as soon as sprayer is plugged
into outlet and sprayer is NOT
turned on.