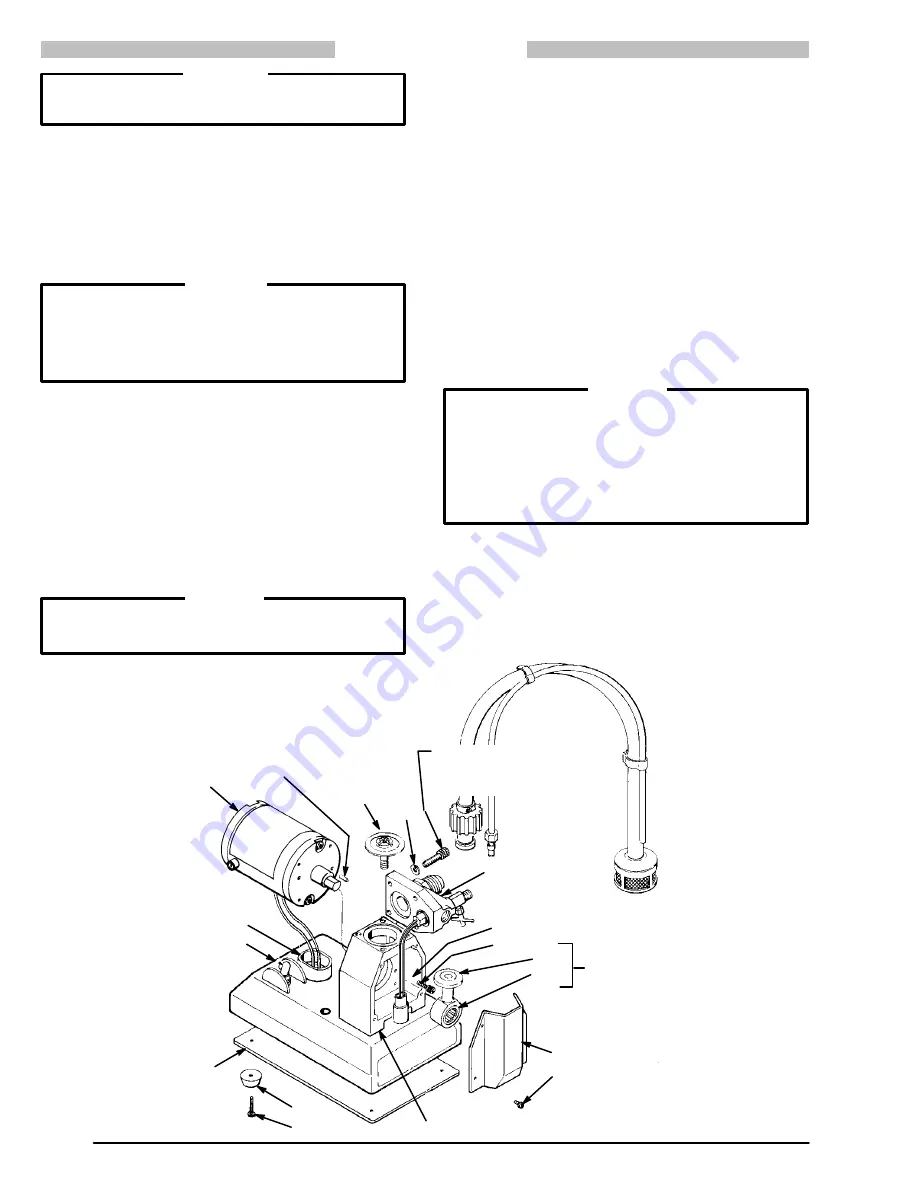
12
307–959
SPRAYER REPAIR
WARNING
Always follow the
Pressure Relief Procedure
Warning
on page 8 before doing any repair.
Connecting Rod & Bearing
(See Fig 10)
1. Remove the following parts: bottom cover (42),
screws (28), handle (32), shield (79), front cover
(23). Refer to the Parts Drawing.
2. Remove the screws (15) and lockwashers (16). Tip
the pump housing (9) out of the way . Unscrew the
diaphragm (17) and discard.
Replace the diaphragm (17) whenever you remove
the pump housing (9). During use, small grooves
are formed in the diaphragm which cannot be re-
aligned properly. Reusing a diaphragm may cause
leaking and result in costly damage to the pump.
CAUTION
3. Remove the motor screws (20) and
lockwashers
(21). Lift the motor (30) slightly. Hold the connecting
rod while pulling the motor away from the housing
(22).
4. Inspect the bearing (18b) in the connecting rod (18a).
If it is worn or any rollers are broken, replace the
bearing and rod assembly (18). Inspect the motor ec-
centric. Replace the motor if the eccentric is worn.
5. Use your fingers to pack high–quality bearing grease
thoroughly in between the bearing rollers.
Thorough greasing of the bearing is essential to ex-
tend the life of the bearing and the motor eccentric.
CAUTION
6. Use a soft brass or nylon bristle brush to clean the top
of the connecting rod and housing.
Gently clean the
bottom of the pump housing (9), avoiding damage to
the diaphragm grooves.
7. Install the connecting rod (18) in the connecting rod
housing (22). Screw a new diaphragm (17) into the
rod just until it touches the bottom. T urn the dia-
phragm 1/4 to 1/2 turn more (6–8 in–lb [2.7–3.6
N.m]). Do not turn more than 1/2 turn, or the dia-
phragm will not function properly.
8. Align the motor with the pins in the connecting rod
housing (22) Guide the motor eccentric through the
connecting rod bearing (18b). Spin the motor shaft to
be sure it moves freely.
9. Loosely install the lockwashers (21) and screws (20).
Spin the motor shaft again. Now, alternately tighten
the screws. Spin the motor shaft again.
Spin the motor shaft while assembling the pump to
ensure that parts are properly aligned. If they are
not, and the pump is started, serious damage could
result to the motor, bearing, and connecting rod. If
there is binding or resistance, disassemble the
parts. Check the spin often until you determine the
cause of the binding.
CAUTION
10. Position the pump housing (9) on the sprayer. Lubri-
cate the screws (15). Install the screws and
lockwashers (16) loosely. Torque the screws a few
inch–pounds (N.m) at a time, oppositely and evenly,
to 85 in–lb (9.7 N.m).
11. Reinstall all parts.
34
GREASE BEARING THOROUGHLY
Fig 10
30
16
17
9
21
20
18a
18b
18
23
24
22
42
43
33
69
PRESS FIT
INTO 22
15
TORQUE OPPOSITELY AND
EVENLY A FEW IN–LB AT A
TIME TO 85 IN–LB (9.7 N.M)