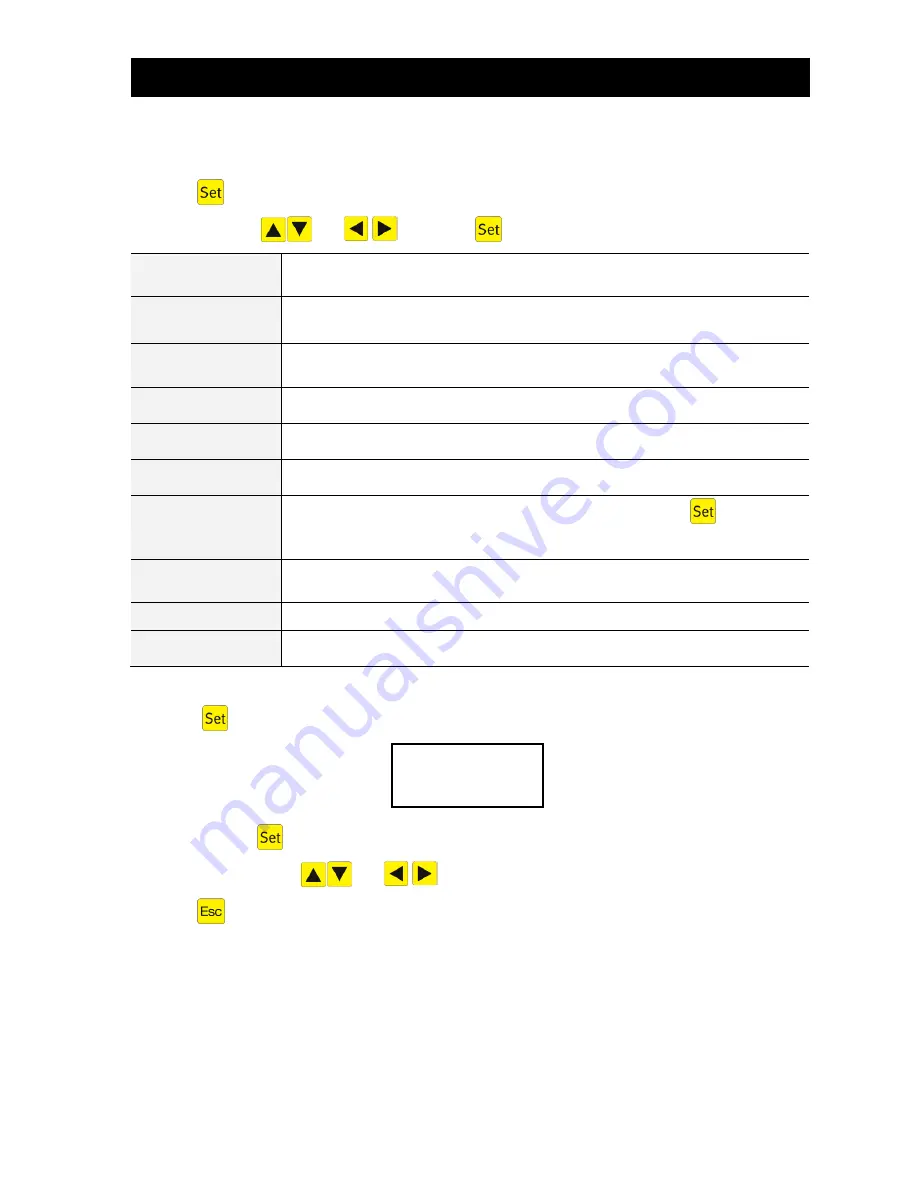
4
.
Control unit
13 / 40
Operating the control unit
4.6
You can start various queries when in automatic mode.
Pressing
takes you to the first operating level. Now you can call up the individual queries by pressing
the two arrow keys
and
followed by
:
Display
KL24plus
Meaning
Operating mode
Remaining time
Time remaining in current operating phase
Operating hours
counter reading
Operating hours display for individual valves and compressor
Manual mode
function
Manual activation of valves
Date
time
Current time, day and date. Can be set by pressing SET
Holiday mode
set date
Set holiday mode (max. 90 days)
Read out old
faults
Operational faults are saved here and can be read out. Press
to switch be-
tween the error message and the associated date
Display
settings
The current settings can be viewed using the arrow keys
Action code
For specialists
Enter service
menu code
For specialists
4.6.1
Operating hours query
Press the
key. Screen shows:
By again pressing
, the operating hours can be called up for valves, compressor and house pump in
turn using the arrow keys
and
.
Pressing
once takes you back to the "Operating hours" display.
Note:
If no key is pressed for 10 minutes, normal mode engages automatically.
Operating hours
Summary of Contents for one2clean+ XXL
Page 39: ...13 Notes 39 40 13 Notes ...