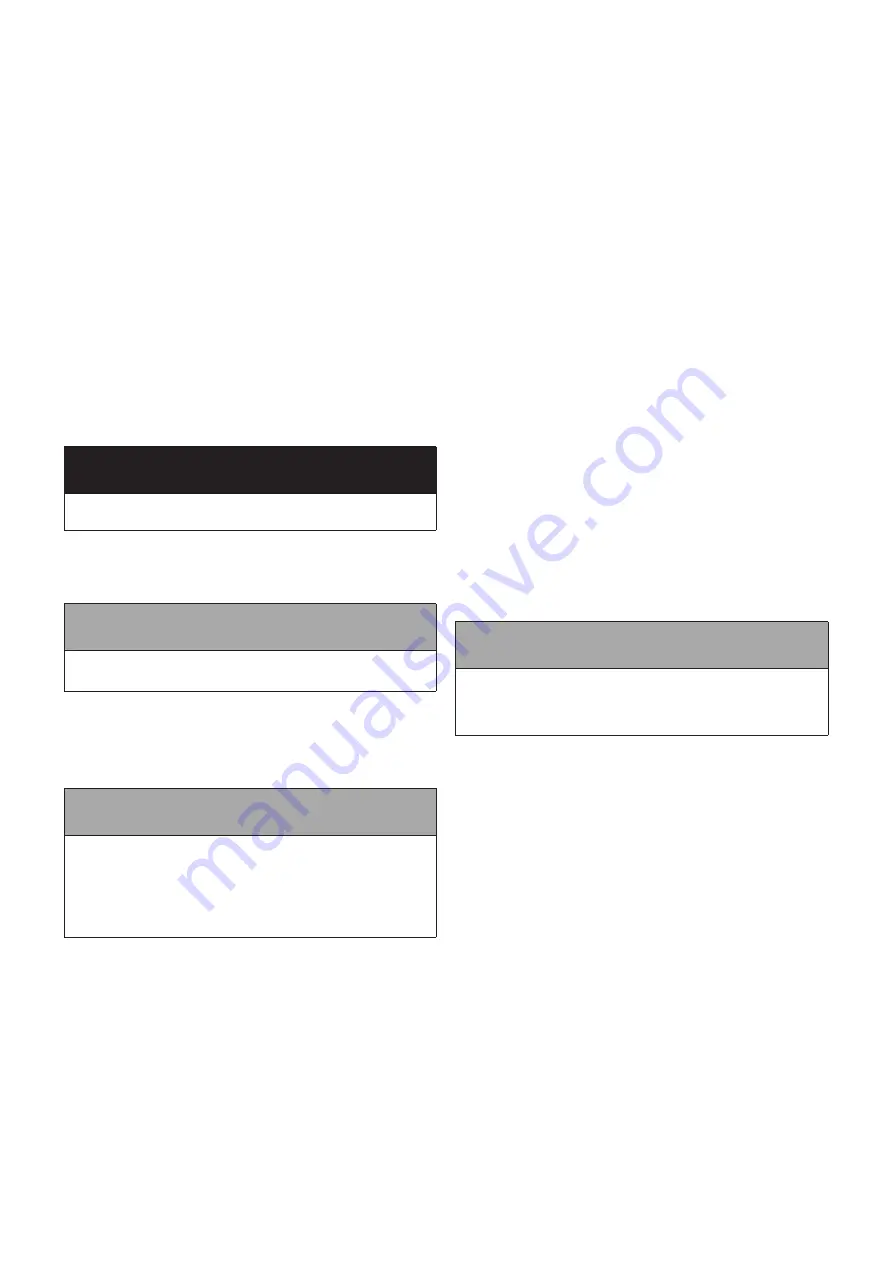
Section 7: Sealed Systems
Page 22
3.
Ensure that the flexible filling loop is connected and that the
double check shut off valve connecting it to the water supply
is closed. A valve is open when the operating lever is in line
with the valve, and closed when it is at right angles to it.
4.
Open the fill point valve.
5. Gradually open the double check valve from the water supply
until water is heard to flow.
6. When the needle of the pressure gauge is between 0.5 and
1.0 bar, close the valve.
7. Vent each radiator in turn, starting with the lowest one in the
system, to remove air.
8.
Continue to fill the system until the pressure gauge indicates
between 0.5 and 1.0 bar. Close the fill point valve. The
system fill pressure (cold) should be 0.2 - 0.3 bar greater
than the vessel charge pressure – giving typical system fill
pressures of approx 0.5 bar for a bungalow and 1.0 bar for a
two storey house.
Refer to the Domestic Heating Design Guide for further
information if required.
9.
Repeat steps 5 to 7 as required until system is full of water at
the correct pressure and vented.
10. Water may be released from the system by manually
operating the safety valve until the system design pressure is
obtained.
11.
Close the fill point and double check valves either side of the
filling loop and disconnect the loop.
12.
Check the system for water soundness, rectifying where
necessary.
7.3
VENTING THE PUMP
For those heating circulating pumps fitted with a vent plug, it is
important that the pump is properly vented to avoid an air lock and
also prevent it running dry and damaging the bearings.
Unscrew and remove the plug from the centre of the pump motor.
Using a suitable screwdriver, rotate the pump spindle about one
turn. Replace the plug in the motor. Do not over tighten.
! NOTE !
Some heating circulating pumps are not fitted with a
vent plug so it is not possible to vent these pumps in the
manner described above. Refer to pump manufacturers
own instructions for further details.
If a Wilo Para pump is used, please refer to Appendix A3
at the back of this installation and servicing manual for
guidance on venting the pump.
7.4
PRESSURE RELIEF (SAFETY) VALVE
OPERATION
Check the operation of the pressure relief (safety) valve as
follows:
1. Turning the head of the valve anticlockwise until it clicks. The
click is the safety valve head lifting off its seat allowing water
to escape from the system.
2.
Check that the water is escaping from the system.
3. Top-up the system pressure, as necessary, by following the
procedure outlined in Section 7.2.
7.1.4 FILLING LOOP
Provision should be made to replace water lost from the
system. This can be done manually (where allowed by the local
water undertaking) using an approved filling loop arrangement
incorporating a double check valve assembly.
The filling loop must be isolated and disconnected after filling the
system.
7.1.5 HEATING SYSTEM
The maximum ‘setpoint’ temperature for the central heating water
is 75°C. Refer to Section 1.1.
An air vent should be fitted in the flow and return pipes of the
highest point of the system.
If thermostatic radiator valves are fitted to all radiators, a system
by-pass must be fitted. The by-pass must be an automatic type.
All fittings used in the system must be able to withstand pressures
up to 3 bar. Radiator valves must comply with the requirements of
BS 2767.
One or more drain taps (to BS 2879) must be used to allow the
system to be completely drained.
7.2
FILLING THE SEALED SYSTEM
Filling of the system must be carried out in a manner approved by
the local Water Undertaking.
! WARNING !
Only ever fill or add water to the system when it is cold and
the boiler is off. Do not overfill.
The procedure for filling the sealed system is as follows:
1.
Check the air charge pressure in the expansion vessel
BEFORE filling the system.
! NOTE !
The air charge pressure can only be correctly checked
when the system water pressure is zero.
The expansion vessel charge pressure should always be
slightly greater than the maximum static head of the system,
in bar, at the level of the vessel (1 bar = 10.2 metres of
water). Refer to Figure 7-2.
The charge pressure must not be less than the actual static
head at the point of connection.
! NOTE !
The air charge pressure may be checked using a tyre
pressure gauge on the expansion vessel Schraeder valve.
The vessel may be re-pressurised, when necessary, using
a suitable pump. When checking the air pressure, the
water in the heating system must be cold and the system
pressure reduced to zero.
2.
Check that the small cap (or screw) on all air vents is open
at least one turn. The cap (or screw) remains in this position
from now on.