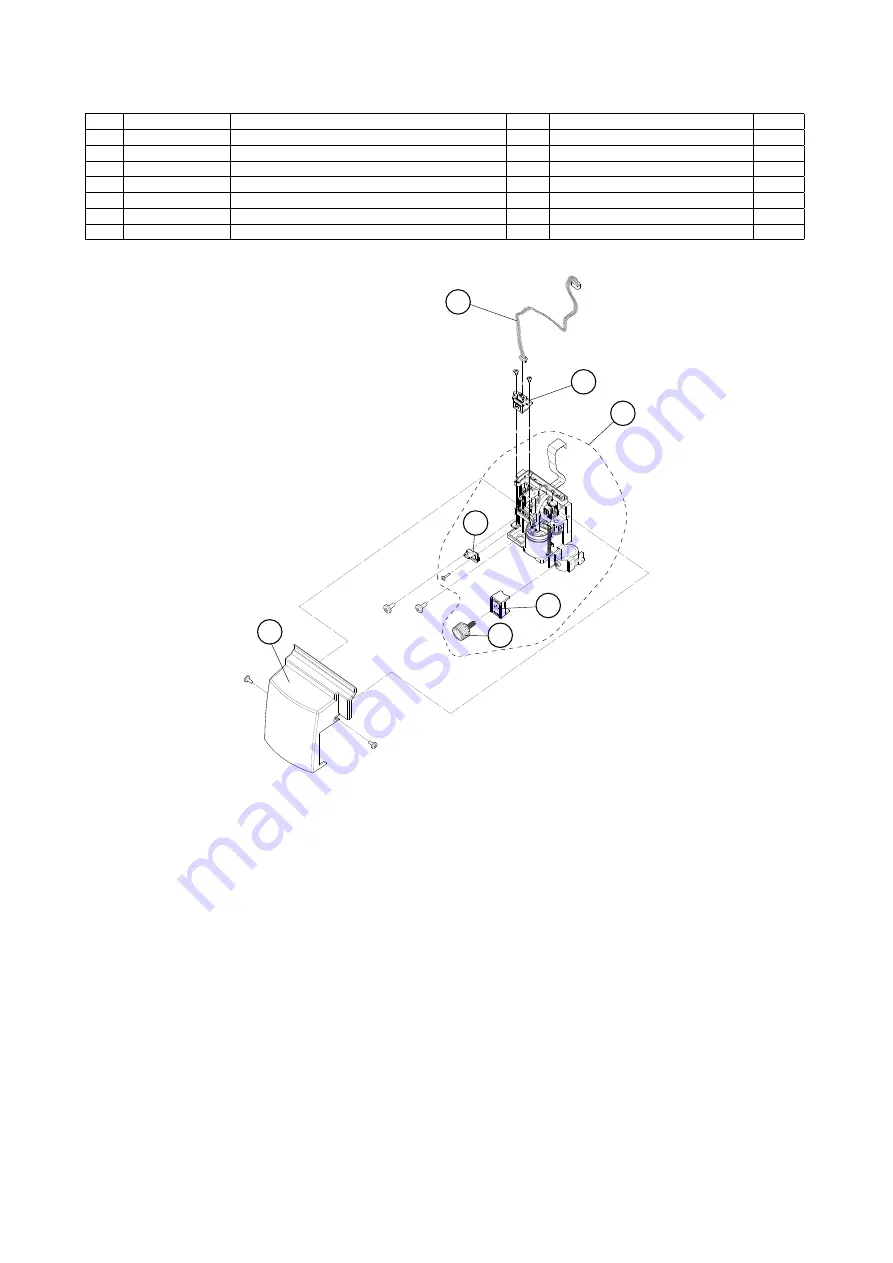
CE7000-UM-251-9370 10-5
10 PARTS LIST
10.5 Pen Block CE7000-40/60/130/160
No.
Part No.
Description
Q’ty
Remarks
Rank
1
U792700760 Pen Block Assembly, CE70
1
A
2
U621833091 Clamp, Cutter Pen Holder
1
A
3
U621353011 Thumb Screw L10
1
A
4
U621843920 Wire Guide, RM Sensor, CE70
1
C
5
U682180300 Registration Mark Sensor, KR4012-GTLF
1
KR4012-GTLF
A
6
U692180161 Cable, CA512216A
1
B
7
U621844021 Pen Block Cover, CE70
1
B
Pen Block CE7000-40/60/130/160
1
2
3
4
5
6
7
Summary of Contents for CE7000-130
Page 1: ...CE7000 UM 251 00 9370 CUTTING PLOTTER SERVICE MANUAL CE7000 40 60 130 160 130AP ...
Page 2: ......
Page 4: ...CE7000 UM 251 9370 II ...
Page 72: ...CE7000 UM 251 9370 5 2 5 RECOMMENDED PARTS LIST ...
Page 74: ......