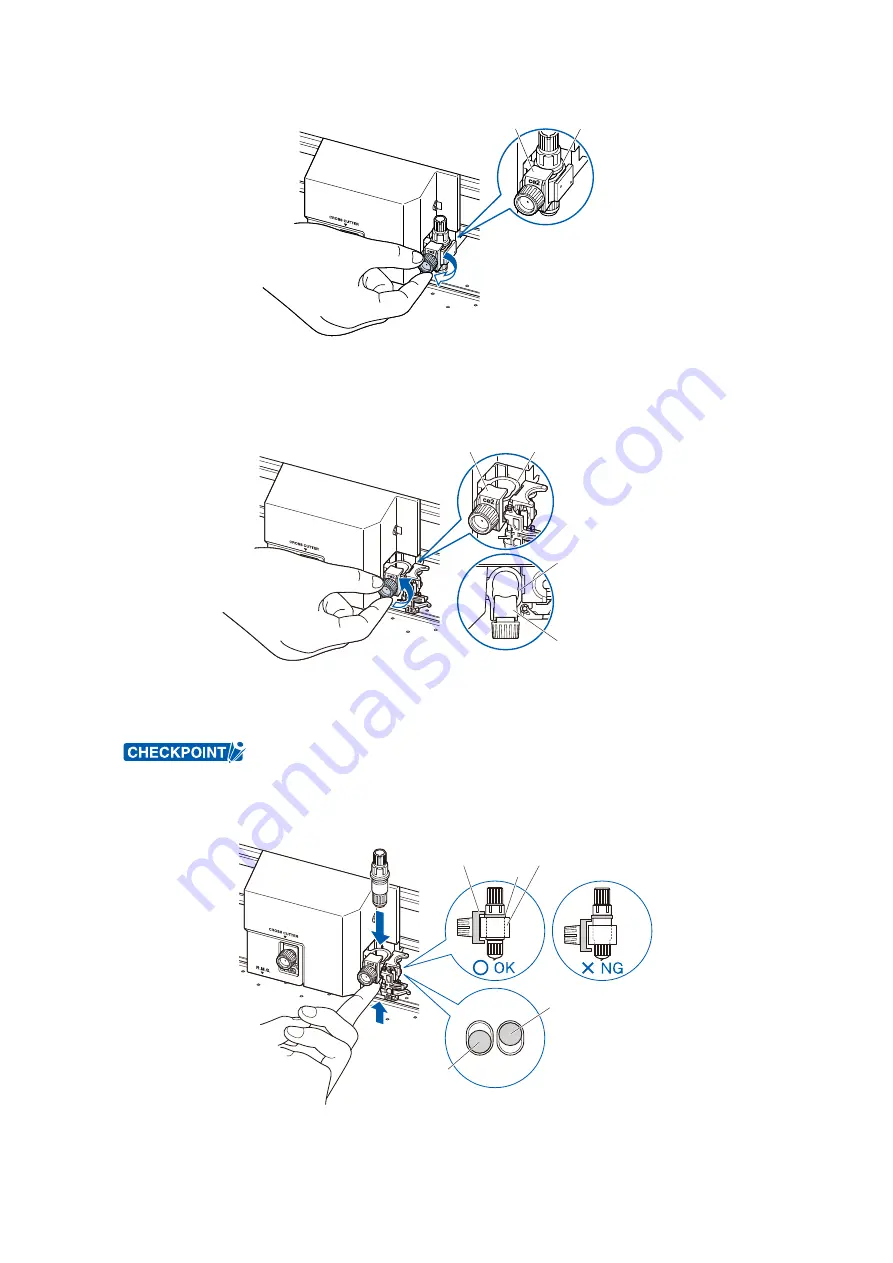
FC9000-UM-251-9370 3-4
3 PARTS NAMES and FUNCTIONS
(3)
Make sure that the tool bracket is engaged on the tool’s flange, and then tighten the screw.
Bracket to hold tool
Flange
Attaching a Pen to the Two-Pen Holder (Option)
The two-pen holder is a factory-installed option, and cannot be retrofitted.
(1) Loosen the pen holder screw
Top view
Tool holder
Tool holder
Bracker to hold tool
Bracker to hold tool
(2) While pushing the pen holder in the upward direction, push the pen all the way into the holder until its
flange contacts the upper part of the holder.
• When you push the pen holder with your fingers, the blade tip may be protruding. Take care not to cut
your fingers.
For half cutting
(backward)
For cutting out
(forward)
Tool holder
Top View
Bracker to hold tool
Flange
Summary of Contents for FC9000-100
Page 1: ...CUTTING PLOTTER SERVICE MANUAL FC9000 75 100 140 160 FC9000 UM 251 01 9370...
Page 2: ......
Page 4: ...FC9000 UM 251 9370 II...
Page 38: ......
Page 201: ...FC9000 UM 251 9370 10 2 10 PARTS LIST Outer Casing 1 2 3 4 10 7 11 5 16 15 6 12 12 9 13 14 8...