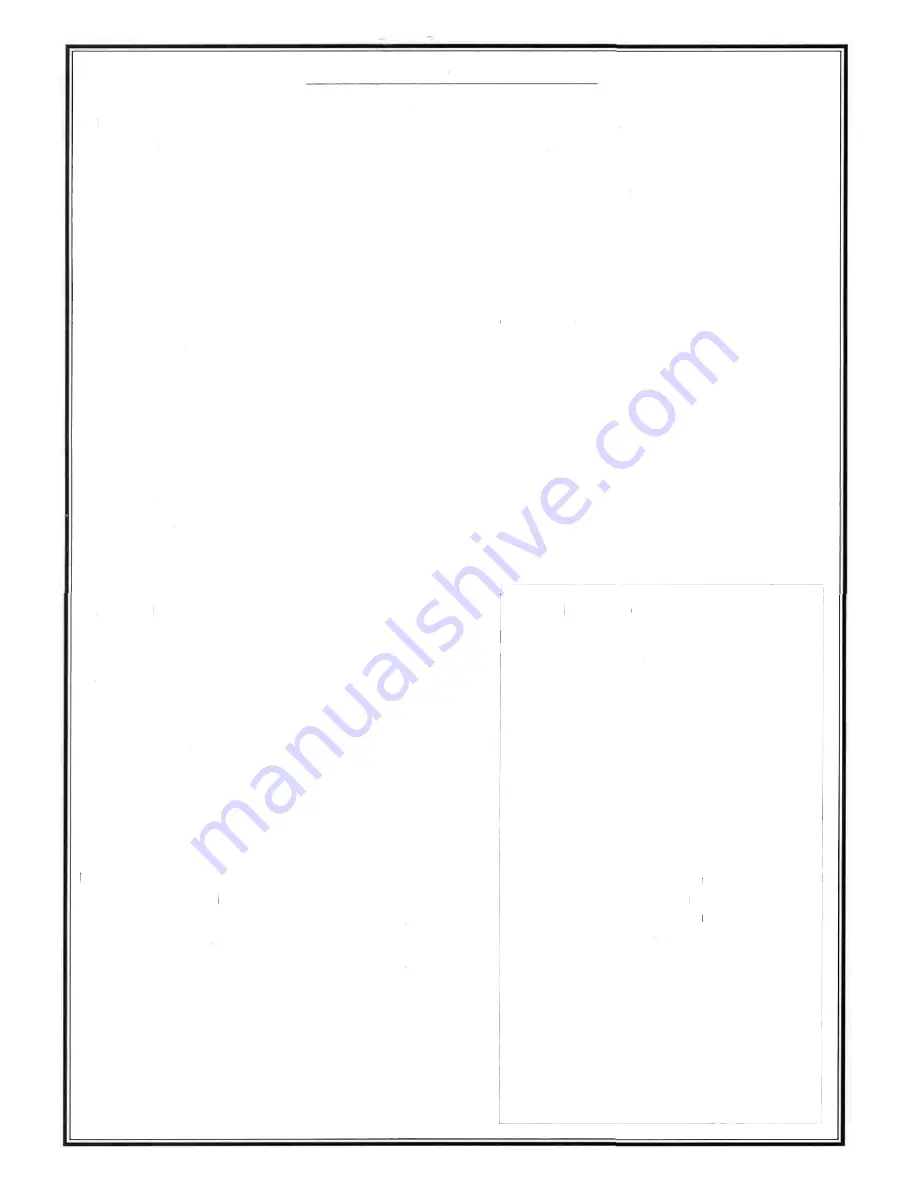
TABLE OF CONTENTS
INTRODUCTION............................................. 3
PRECAUTIONS........................................... 3
OTHER ITEMS REQUIRED ........................ 4
SUPPLIES AND TOOLS NEEDED.............. 4
DECISIONS YOU MUST MAKE NOW........ 5
COMMON ABBREVIATIONS ..................... 5
TYPES OF WOOD ...................................... 5
GET READY TO BUILD............................... 5
DIE-CUT PARTS DRAWING ....................... 6
TAIL FEATHERS ............................................ 7
BUILD THE FIN AND RUDDER................... 7
BUILD THE STAB. AND ELEVATOR ........... 8
TEMPORARILY INSTALL HINGES AND
TORQUE RODS........................................... 9
FUSELAGE ASSEMBLY................................ 10
PREPARE FUSE SIDES............................. 10
MOUNT ENGINE AND INSTALL SERVOS....... 18
BUILD THE NOSE SECTION ..................... 22
INSTALL THE RECEIVER BATTERY..........23
GLUE THE STABS ON ............................... 24
MAKE ELEVATOR PUSHROD.................... 25
FINISH UP THE FUSELAGE...................... 26
WING.............................................................. 28
SPARS ........................................................ 28
BUILD THE WING PANELS........................ 29
INSTALL WING TOP SHEETING................ 33
INSTALL THE BOTTOM WING SHEETING...... 35
INSTALL THE AILERON TORQUE RODS........ 38
ASSEMBLE AILERONS.............................. 39
INSTALL AILERON SERVO........................ 40
FINISHING THE WING ............................... 41
FINAL ASSEMBLY......................................... 42
MAKE RUDDER PUSHRODS .................... 42
FIT THE WING TO THE FUSE ................... 42
PREPARE THE CANOPY........................... 43
BALANCE THE AIRPLANE LATERALLY.... 44
FINAL SANDING......................................... 44
COVERING................................................. 44
GLUE FINS IN PLACE................................ 44
GLUE THE AILERON HINGES................... 44
GLUE TAIL FEATHER HINGES ..................45
COCKPIT & SEAT....................................... 45
GLUE CANOPY IN PLACE......................... 46
DECALS AND TRIM.................................... 46
WING SEATING.......................................... 47
RE-INSTALL ENGINE & RADIO ................. 47
CONTROL SURFACE THROWS................ 47
BALANCE YOUR MODEL .......................... 47
FINAL HOOKUPS AND CHECKS............... 48
PRE-FLIGHT.................................................. 49
CHARGE THE BATTERIES........................ 49
FIND A SAFE PLACE TO FLY.................... 49
GROUND CHECK THE MODEL................. 49
RANGE CHECK YOUR RADIO .................. 49
ENGINE SAFETY PRECAUTIONS............. 49
AMA SAFETY CODE .................................. 50
FLYING........................................................... 50
TAKEOFF.................................................... 50
FLYING........................................................ 50
LANDING .................................................... 51
2-VIEW DRAWING......................................... 52
METRIC CONVERSIONS
1"= 25.4 mm (conversion factor)
1/64" = .4 mm
1/32" = .8 mm
1/16" =1.6 mm
3/32" = 2.4 mm
1/8" = 3.2 mm
5/32" = 4 mm
3/16" =4.8 mm
1/4" =6.4 mm
3/8" = 9.5 mm
1/2" =12.7 mm
5/8" =15.9 mm
3/4" =19 mm
1" =25.4 mm
2" = 50.8 mm
3" = 76.2 mm
6" = 152.4mm
12" =304.8 mm
15" =381 mm
18" =457.2 mm
21" =533.4 mm
24" = 609.6 mm
30" = 762 mm
36" =914.4 mm
2
Summary of Contents for F-15 EAGLE
Page 7: ...6 DIE CUT PATTERNS ...
Page 53: ...TWO VIEW DIAGRAM ...