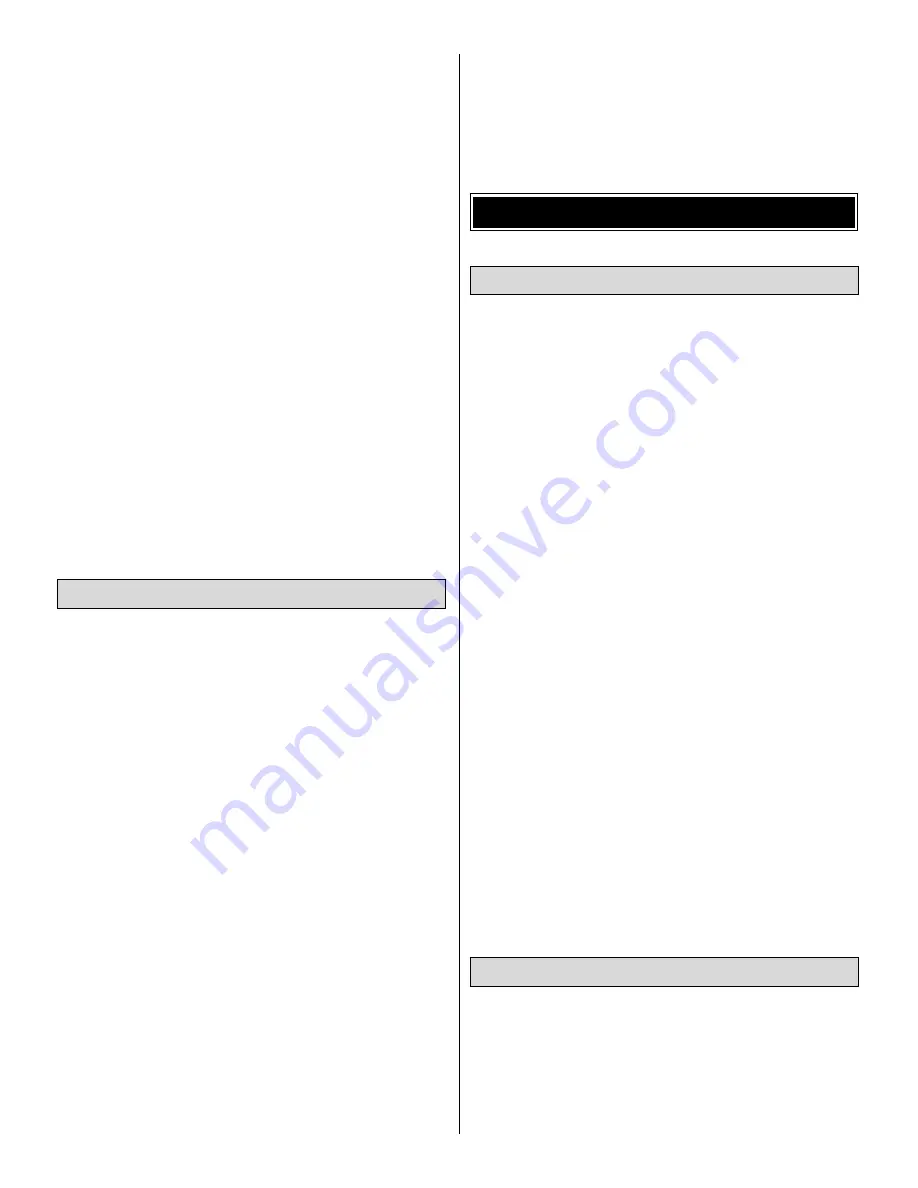
batteries. A single cell rechargeable battery supplies 1.2
volts with no load (not powering anything). A 7-cell battery
pack can supply 8.4 volts (1.2 volts x 7 cells = 8.4 volts). The
cell rating in mAh (milli-amp-hours) is the amount of current
the battery can supply. If a battery is rated at 1700 mAh, the
battery can supply 1.7 amps for 1 hour (or 1 amp for 1.7
hours). This sounds great, flying for over 1-1/2 hours on a
single battery charge! The bad news is that to produce the
power needed to fly an airplane the size of the Ryan STA
EP, the motor draws from 15-25 amps. The current
consumption reduces the run time to 4-6 minutes. The good
news is that propellers become more efficient as the speed
of the plane increases. This lowers the current draw,
allowing the plane to fly longer on a single charge,
sometimes up to 20% longer. Also, if an electronic speed
control is used, the motor can be throttled back, increasing
the flight time. Most airplanes only need full throttle during
takeoff.
We recommend the use of high quality battery packs. The
higher quality batteries usually have less internal resistance
than the average battery. The higher quality battery will
provide more power to the motor than the average battery.
In rechargeable batteries, internal resistance transforms
power into heat. With less internal resistance, there is more
power available to the motor and less heat is generated. We
hope this helps explain NiCd and NiMH batteries and why a
high quality battery should be used in the Ryan STA EP.
A fully charged battery pack will provide an initial “surge” of
power during the first 15 to 30 seconds of the motor run.
Then the power output stays fairly steady for the next
several minutes before dropping off quickly. If you do not
charge your battery completely, it will not deliver that surge
necessary for a good takeoff and climb out. There are three
easy ways to “peak-charge” your battery pack.
1. The easiest way is with a “peak-detecting” battery
charger. This type of charger will automatically charge your
battery until it is fully charged. The NiMH batteries require a
peak-detecting charger that meets the specific charging
needs of NiMH batteries.
2. The second method of charging your motor batteries is to
monitor the voltage of your battery pack with a voltmeter.
This method is only recommended for NiCd batteries.
Your charger may have sockets into which you may plug a
voltmeter. If not, you may insert the probes from the
voltmeter into the rear of the battery plug, making contact
with the metal contacts. As your battery charges, the voltage
will gradually increase. When the battery is fully charged,
the voltage will start to drop. At this point your battery is fully
charged.
3. The third (and least reliable) method of peak-charging
your battery pack is by checking its temperature. This
method is only recommended for NiCd batteries. As the
battery charges it will remain cool until it is fully charged.
When it reaches the fully charged state, it will rapidly build
up heat. You can feel this heat with your hand. As soon as
the pack starts to noticeably warm up, disconnect it from the
charger. Do not continue charging if the battery pack is
hot! Overcharging will damage your battery pack and can
result in an explosion.
In addition to the items listed in the
“Decisions You Must
Make” section, following is the list of hardware and
accessories required to finish the Ryan STA EP. Order
numbers are provided in parentheses and are recognized
by most distributors and hobby shops and are listed for your
convenience.
❏
4-channel radio with 4 mini servos
❏
(2) 2" Ultralite Wheel (GPMQ4201)
❏
(1) 1" Tail Wheel (GPMQ4241)
❏
(1) Velcro
®
Hook and Loop material (GPMQ4480)
❏
(1) 1-3/4" White Spinner (GPMQ4505)
❏
(1) 1/6 Scale (2") Pilot
❏
(1) C-30 ElectriFly Electronic Speed Control
(GPMM2030, included in GPMG0075)
❏
(1) Motor battery pack charger 910 Hobbico
®
Variable
Rate Charger (HCAP0175) or the DuraTrax
®
Intellipeak
™
AC/DC Pulse Charger (DTXP4100)
❏
(1)1700 mAh 8.4 volt NiCd battery pack (DTXC2071)
or 3000 mAh 8.4 volt NiMH battery pack (DTXC2096)
Recommended Drive Unit
❏
(1) GD-600 Gear Drive (GPMG0850)
❏
(1) 15 Tooth Pinion Gear (GPMG0852)
❏
(1) Motor (14-turn reverse, GPMG0715)
❏
(1) 9x8 Propeller (APCQ0908)
or
❏
(1) S-600 GD System (GPMG0770), or S-600 GD
System with ESC (GPMG0775)
❏
(1) White MonoKote Film (TOPQ0204)
❏
(1) Red MonoKote Film (TOPQ0201)
❏
(1) Black MonoKote Film (TOPQ0208)
❏
(1) White LustreKote
®
Paint (TOPR7204)
❏
(1) Red LustreKote Paint (TOPR7201)
❏
(1) Black LustreKote Paint (TOPR7208)
In addition to common household tools (screwdrivers, drill,
etc.), this is the “short list” of the most important items
required to build the Ryan STA EP.
We recommend Great
Planes Pro
™
CA and Epoxy glue.
❏
1/2 oz. Thin Pro CA (GPMR6001)
❏
1/2 oz. Medium Pro CA+ (GPMR6007)
Adhesives & Building Supplies
Hardware & Accessories
ADDITIONAL ITEMS REQUIRED
Chargers
4
Summary of Contents for Ryan STA EP
Page 7: ...7 DIE CUT PATTERNS...
Page 48: ...TWO VIEW DRAWING Use copies of this page to plan your trim scheme...
Page 49: ...B C...
Page 50: ...D A...