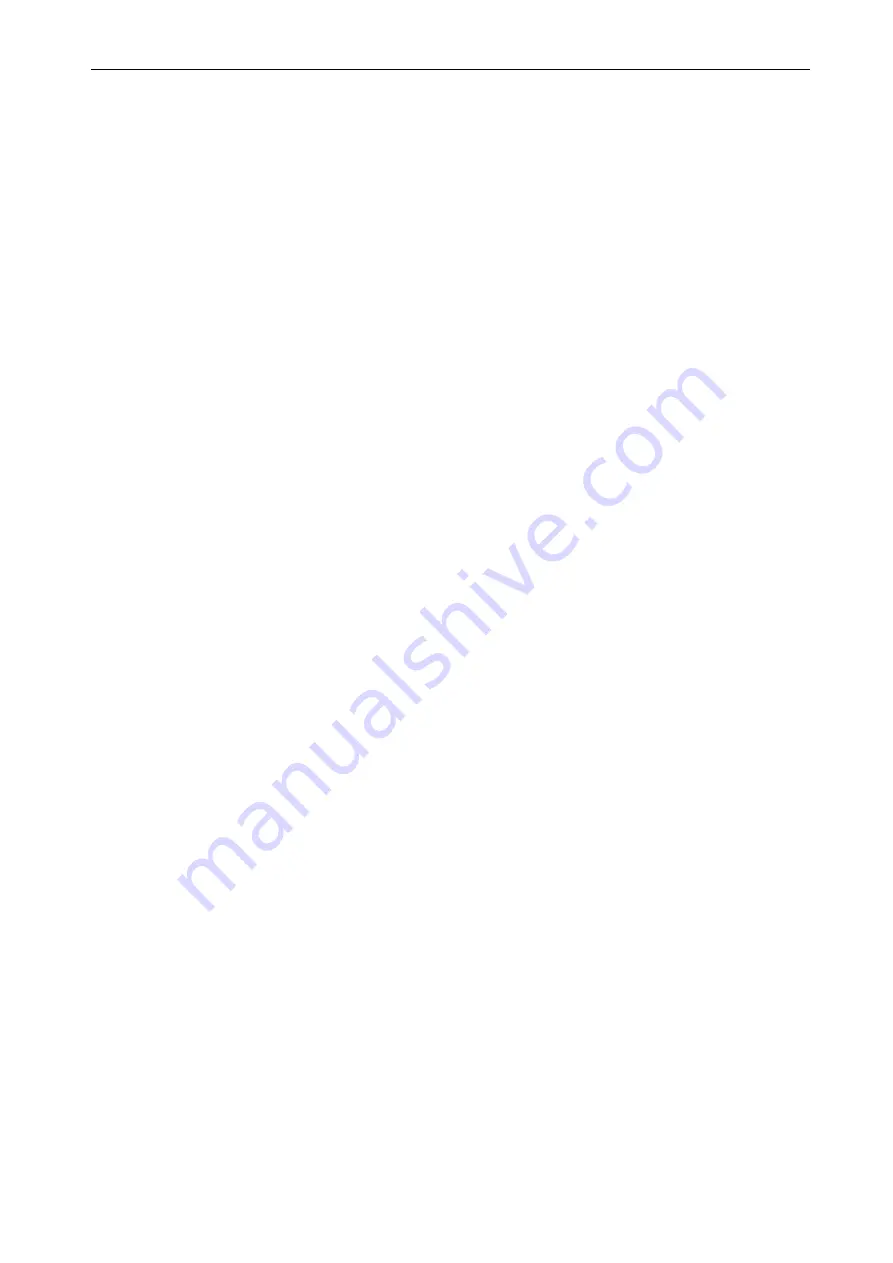
Air-to-water Heat Pump
28
The recovery equipment shall be in good working order with a set of instructions concerning the
equipment that is at hand and shall be suitable for the recovery of flammable refrigerants.
In addition, a set of calibrated weighing scales shall be available and in good working order.
Hoses shall be complete with leak-free disconnect couplings and in good condition. Before using
the recovery machine, check that it is in satisfactory working order, has been properly maintained and
that any associated electrical components are sealed to prevent ignition in the event of a refrigerant
release. Consult manufacturer if in doubt.
The recovered refrigerant shall be returned to the refrigerant supplier in the correct recovery cylinder,
and the relevant Waste Transfer Note arranged. Do not mix refrigerants in recovery units and especially
not in cylinders.
If compressors or compressor oils are to be removed, ensure that they have been evacuated to an
acceptable level to make certain that flammable refrigerant does not remain within the lubricant. The
evacuation process shall be carried out prior to returning the compressor to the suppliers. Only electric
heating to the compressor body shall be employed to accelerate this process. When oil is drained from a
system, it shall be carried out safely.
13.2 Decommissioning
Before carrying out this procedure, it is essential that the technician is completely familiar with the
equipment and all its detail. It is recommended good practice that all refrigerants are recovered safely.
Prior to the task being carried out, an oil and refrigerant sample shall be taken in case analysis is
required prior to re-use of reclaimed refrigerant. It is essential that electrical power is available before the
task is commenced.
(1) Become familiar with the equipment and its operation.
(2) Isolate system electrically.
(3) Before attempting the procedure ensure that: mechanical handling equipment is available, if
required, for handling refrigerant cylinders; all personal protective equipment is available and
being used correctly; the recovery process is supervised at all times by a competent person;
recovery equipment and cylinders conform to the appropriate standards.
(4) Pump down refrigerant system, if possible.
(5) If a vacuum is not possible, make a manifold so that refrigerant can be removed from various
parts of the system.
(6) Make sure that cylinder is situated on the scales before recovery takes place.
(7) Start the recovery machine and operate in accordance with manufacturer's instructions.
(8) Do not overfill cylinders. (No more than 80 % volume liquid charge).
(9) Do not exceed the maximum working pressure of the cylinder, even temporarily.
(10) When the cylinders have been filled correctly and the process completed, make sure that the
cylinders and the equipment are removed from site promptly and all isolation valves on the
equipment are closed off.
(11) Recovered refrigerant shall not be charged into another refrigeration system unless it has been
cleaned and checked.