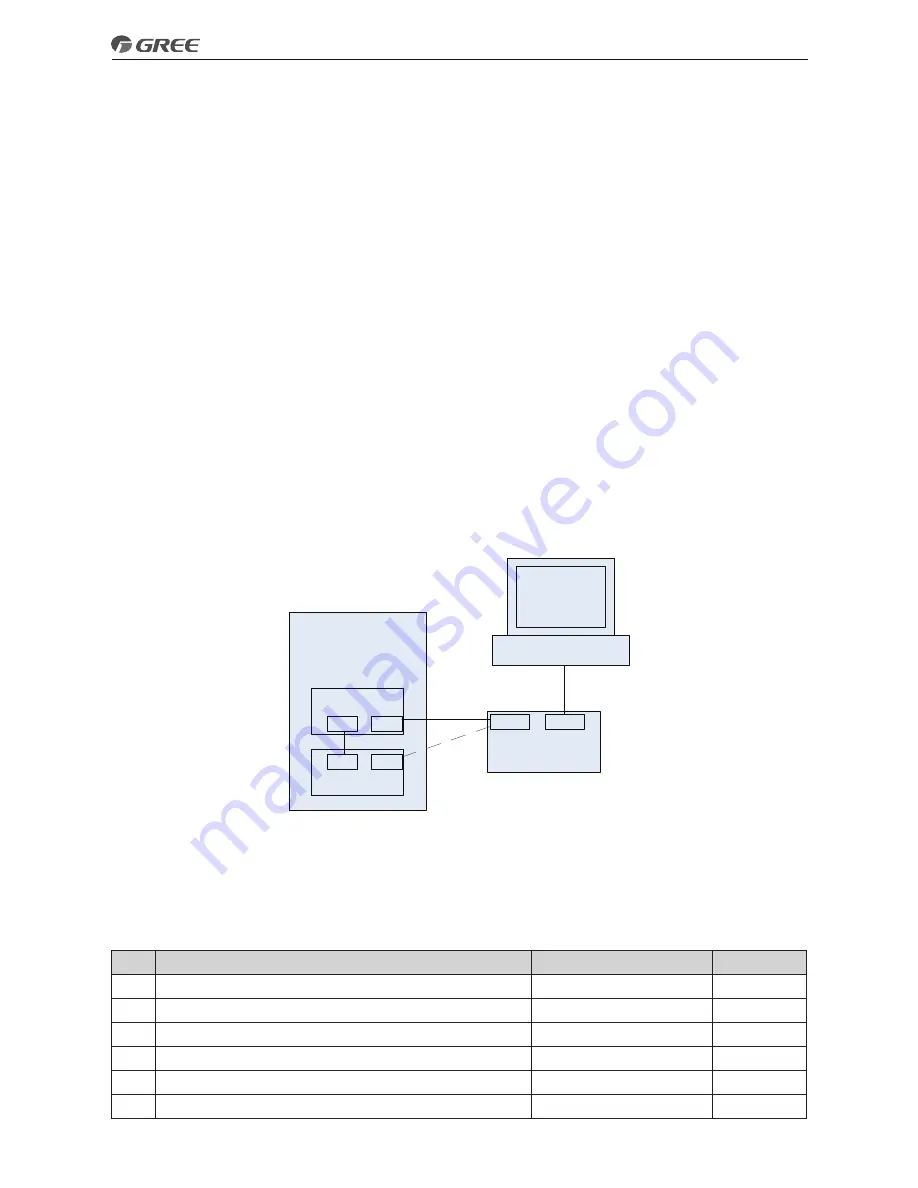
1
Test Operation & Troubleshooting & Maintenance
1 Trial Run
1�1 Check for Wiring
WARNING!
Do not check for the power supply unless proper checkout equipment has prepared and preventive
measures have been taken, otherwise it would lead to severe injury.
◆
Are sizes of connection lines and the air switch proper?
◆
Does wiring comply with relative standards and electric codes?
◆
Is there any incorrect wiring?
◆
Does each contact work properly?
◆
Is the power supply and insulation proper?
◆
Are initial set points of control and protective elements satisfied?
1�2 Check for the Water System
◆
Are water inlet and outlet directions correct?
◆
Is the water piping cleaned? Are there foreign matters at the pipe joints? Is the water quality satisfied?
◆
Is insulation of water pipes in good condition?
◆
Does exhaust valve of the water system work properly?
1�3 Check for the Communication System
When the unit is powered on, check for the communication system, including: communication between AP1
and AP2, between the wired controller and the main board. When there is unusual communication, this error will
be displayed at the wired controller. Then, check out the cause according to the displayed error. See the figure
below for wiring of the communication system.
CN8
CN7
CN6
CN5
AP1
AP2
Wired controller
CN5(Red)
Long-distance
Minitor PC(BMS)
CN4(White)
1�4 Trial Run
Start the unit when there is no any problem for wiring and piping. After startup, check for the electrostatic
expansion valve, water pump, fan, and compressor to see if they work normally. When there is any error, solve
it according to the troubleshooting flowchart covered in this manual. However, if the troubleshooting flowchart is
still unhelpful, please contact GREE sales agent.
2 Error Code List
No�
Full Name
Displayed Name
Error Code
1
Ambient temperature sensor error
Ambient sensor
F4
2
Defrost temperature sensor error
Defro. sensor
d6
3
Discharge temperature sensor error
Disch. sensor
F7
4
Suction temperature sensor error
Suction sensor
F5
5
Outdoor fan error
Outdoor fan
EF
6
Compressor internal overload protection
Comp. overload
H3
Summary of Contents for Versati II Series
Page 18: ......