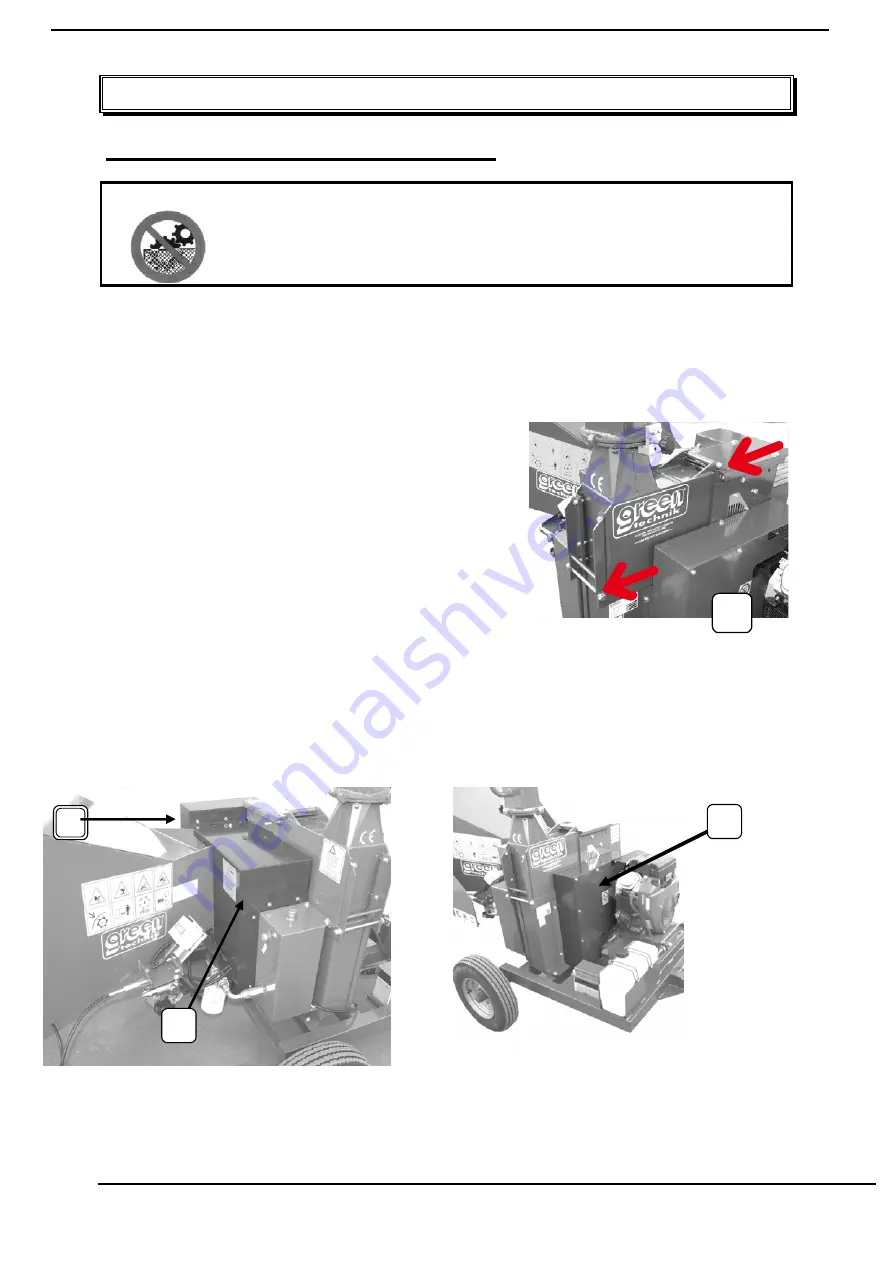
CIP 1500 – User and Maintenance Manual
11
Chapter
5
SAFETY GUARDS
PROTECTIONS AND SAFETY DEVICES
CAUTION!
Protections have been provided for by the manufacturer in
order to safeguard the operator’s physical integrity.
During the operation, the safety guards cannot be removed
for any reason whatever.
A)
Fixed guard for closing of the flywheel
rotation zone.
B)
Fixed guard protecting from driving belts.
C)
Rear guard for protection from hydraulic
components
D)
Side guard for protection from hydraulic
components.
NOTE: The guards have not to be removed:
when servicing, switch off the engine
and take off the key from the control
panel.
A
D
C
B