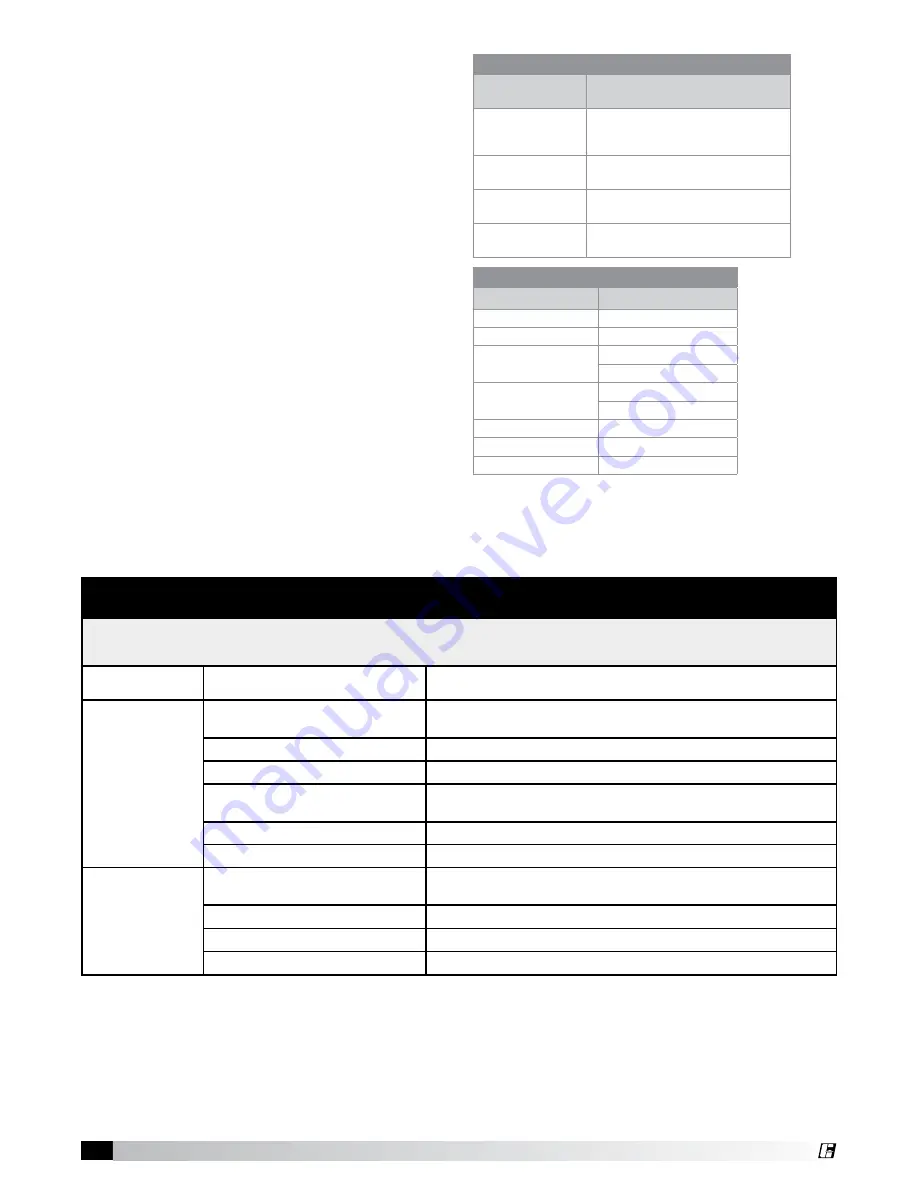
6
Model BDF • Belt Drive Duct Fan
®
Troubleshooting
WARNING: Before taking any corrective action, make certain unit is not capable of operation during
repairs.
PROBLEM
CAUSE
CORRECTIVE ACTION
Excessive noise
or vibration
Wheel unbalance
Clean all dirt off wheel. Check wheel balance, rebalance in place if
necessary.
Bad bearings
Replace.
Belts too tight or too loose
Adjust tension, see figure 7.
Wheel improperly aligned and
rubbing
Center wheel on inlet.
Loose drive or motor pulleys
Align and tighten. See “Pre-Starting Checks”, see page 4-5.
Foreign objects in wheel or housing Remove objects, check for damage or unbalance.
Reduced airflow
System resistance too high
Check system: Proper operation of backdraft or control dampers,
obstruction in ductwork, clean dirty filters.
Unit running backwards
Correct as shown in figure 4.
Excessive dirt buildup on wheels
Clean wheel.
Improper wheel alignment
Center wheel on inlets. See “Pre-Starting Checks”, see page 4-5.
Table 1: Suggested Fan Bearing Greasing Intervals
Interval (months)
Type of Service
1 to 3
Heavy duty in dirty, dusty locations;
high ambient temperatures; moisture
laden atmosphere; vibration.
3 to 6
12 to 24 hours per day, heavy duty,
or if moisture is present
6 to 12
8 to 16 hours per day in clean,
relatively dry atmosphere
12 to 18
Infrequent operation or light duty in
clean atmosphere
Table 2: Grease Manufacturers
Manufacturer
Grease (NLGI #2)
U.S. Electric Motors
Grease No. 83343
Chevron U.S.A. Inc
Chevron SRI Grease #2
Mobil Oil Corporation
Mobilith
Mobil 532
Texaco, Inc.
Premium BRB #2
Texaco Multifak #2
Amoco Oil Co.
Rykon Premium #2
Exxon
Unirex N2
Shell
B Shell Alvania #2
4. Once installed, adjust belts as shown in
“Pre-Starting Checks.”
5. Shaft bearings can be classified in two
groups: relubricating and non-relubricating.
B
earings on sizes 80 through 180 are factory
lubricated and require no further lubrication
under normal use (between -20°F and 180°
F
in a relatively clean environment). Bearings on
size 200 are relubricatable. These bearings
will require frequent lubrication. Caution
should be employed to prevent overpacking or
contamination.
6. Grease fittings should be wiped clean. The unit
should be in operation while lubricating. Extreme
care should be used around moving parts.
7. Grease should be pumped in very slowly until a
slight bead forms around the seal. A high grade
lithium base grease should be used.
Recommended Relubrication
Frequency in Months
NOTE: If unusual environment conditions exist
(extreme temperature, moisture or contaminants)
more frequent lubrication is required.
A good quality lithium base grease, conforming to
NLGI Grade 2 consistency, such as those listed here
may be used.