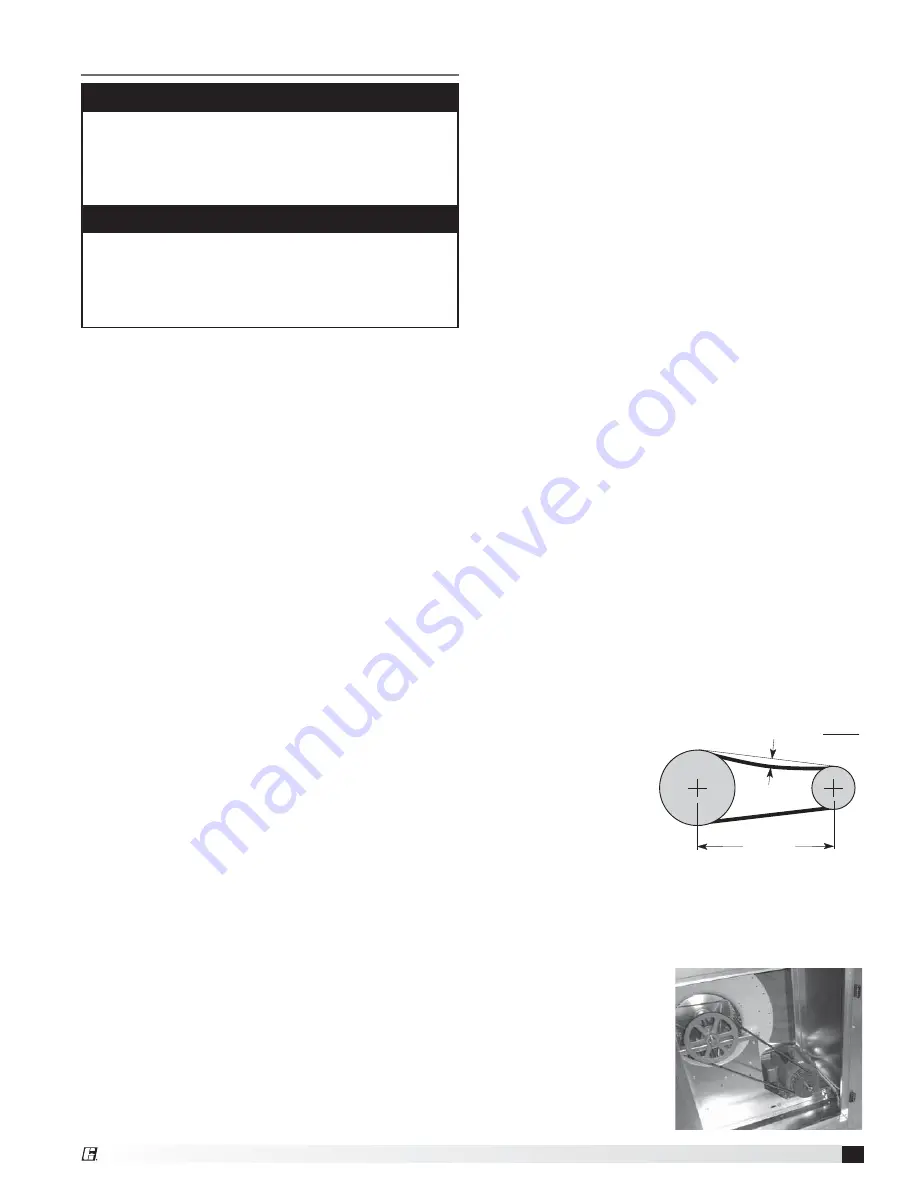
21
Energy Recovery Ventilator
Dampers
Check all dampers to ensure they open and close
properly and without binding. Backdraft dampers can
be checked by hand to determine if blades open and
close freely. Apply power to motorized dampers to
ensure the actuator opens and closes the damper as
designed.
Fan Belts
Belts must be checked on a regular basis for
wear, tension, alignment, and dirt accumulation.
Premature or frequent belt failures can be caused by
improper belt tension (either too loose or too tight)
or misaligned sheaves. Abnormally high belt tension
or drive misalignment will cause excessive bearing
loads and may result in failure of the fan and/or motor
bearings. Conversely, loose belts will cause squealing
on start-up, excessive belt flutter, slippage, and
overheated sheaves. Both loose and tight belts can
cause fan vibration.
When replacing belts on multiple groove drives, all
belts should be changed to provide uniform drive
loading. Do not pry belts on or off the sheave. Loosen
belt tension until belts can be removed by simply
lifting the belts off the sheaves. After replacing belts,
ensure that slack in each belt is on the same side of
the drive. Belt dressing should never be used.
Do not install new belts on worn sheaves. If the
sheaves have grooves worn in them, they must be
replaced before new belts are installed.
The proper belt setting is the lowest tension at which
the belts will not slip under peak load operation.
For initial tensioning, set the belt deflection at
1/64- inch for each inch of belt span (measured half-
way between sheave centers). For example, if the
belt span is 64 inches, the belt deflection should
be one inch (using
moderate thumb
pressure at mid-point
of the drive). Check
belt tension two times
during the first 24 hours
of operation and
periodically thereafter.
Fan Motors
Motor maintenance is generally limited to cleaning
and lubrication. Cleaning should be limited to exterior
surfaces only. Removing dust and grease buildup
on the motor housing assists proper motor cooling.
Never wash-down motor
with high pressure spray.
Greasing of motors is
only intended when
fittings are provided.
Many fractional motors
are permanently
lubricated for life and
require no further
lubrication.
Routine Maintenance
DANGER
Electric shock hazard. Can cause injury or death.
Before attempting to perform any service or
maintenance, turn the electrical power to unit
to OFF at disconnect switch(es). Unit may have
multiple power supplies.
CAUTION
Use caution when removing access panels or other
unit components, especially while standing on a
ladder or other potentially unsteady base. Access
panels and unit components can be heavy and
serious injury may occur.
Once the unit has been put into operation, a routine
maintenance program should be set up to preserve
reliability and performance. Items to be included in
this program are:
Lubrication
Apply lubrication where required
Dampers
Check for unobstructed operation
Fan Belts
Check for wear, tension, alignment
Motors
Check for cleanliness
Blower Wheel & Fasteners
Check for cleanliness
Check all fasteners for tightness
Check for fatigue, corrosion, wear
Bearings
Check for cleanliness
Check set screws for tightness
Lubricate as required
External Filter
Check for cleanliness - clean if required
Internal Filter
Check for cleanliness - replace if required
Door Seal
Check if intact and pliable
Energy Recovery Wheel
Check for cleanliness - clean if required
Check belt for wear
Check pulley, bearings, and motor
Maintenance Procedures:
Lubrication
Check all moving components for proper lubrication.
Apply lubrication where required. Any components
showing excessive wear should be replaced to
maintain the integrity of the unit and ensure proper
operation.
Belt Span
Deflection =
Belt Span
64