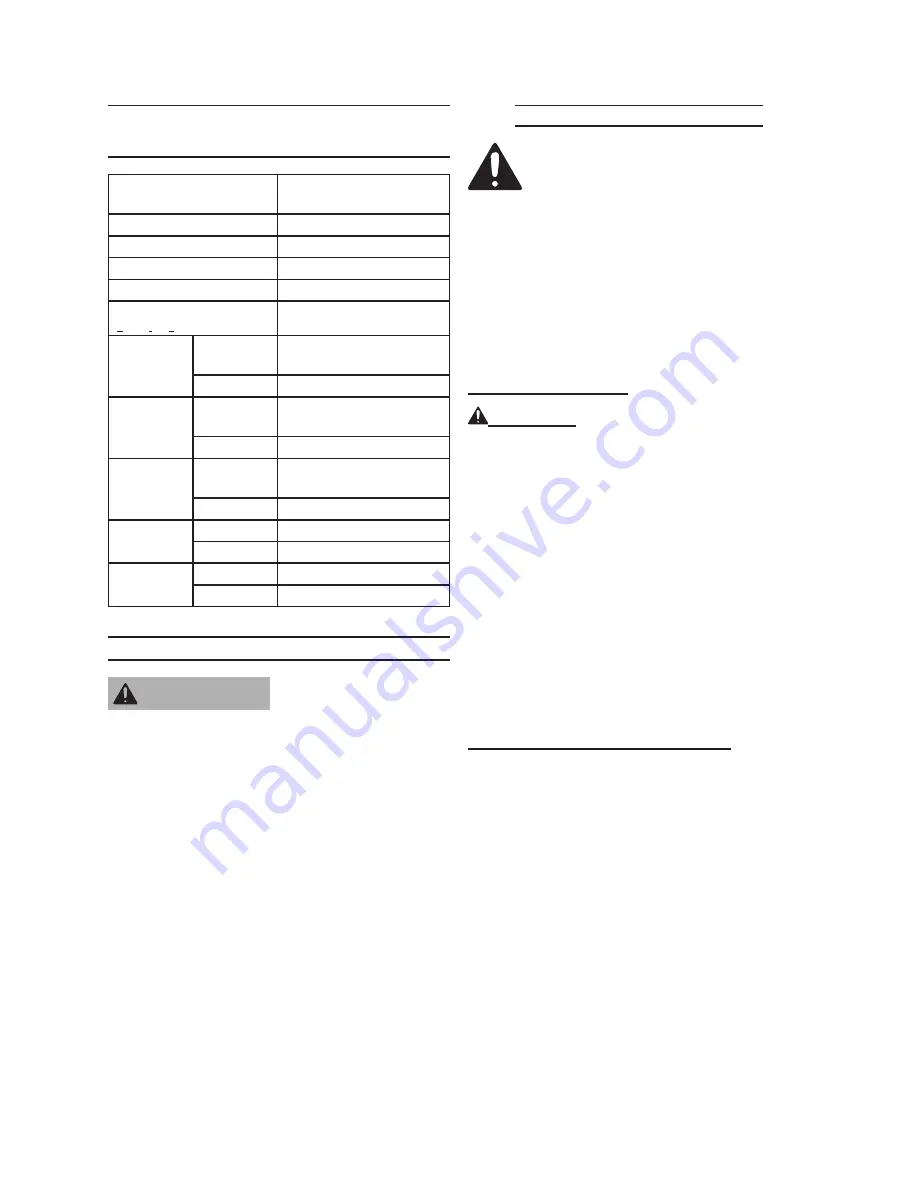
Page 15
SKU 65075
For technical questions, please call 1-800-444-3353.
tecHnical
speciFications
Engine Type
Single Cylinder 4 stroke
OHV
Battery Required
12V 18Ah
Bore x Stroke
68mm x 54mm
Displacement
196cc
Compression Ratio
8.5:1
Rotation
viewed from PTO
(power takeoff - the output shaft)
Counterclockwise
Fuel
Type
86+ octane unleaded
gasoline
Capacity
0.95 Gallons
Engine Oil
Type SAE 10W30 above 32° F
5W30 at 32° F or below
Capacity
0.63 Quarts
Spark Plug
Type
F7RTC or
NGK F7TC
Gap
0.028 - 0.031”
Valve
Clearance
Intake
0.15 ± 0.02 mm
Exhaust
0.20 ± 0.02 mm
Speed
Idle
1,400 ± 150 RPM
Maximum 3,400 RPM
servicing
risk of serious
personal injury
from accidental starting. turn
the power switch of the
equipment to its “oFF”
position, wait for the engine to
cool, and unplug the spark
plug wire(s) before performing
any inspection, maintenance,
or cleaning procedures.
damaged equipment can fail,
causing serious personal
injury. do not use damaged
equipment. if abnormal noise,
vibration, or excess smoking
occurs, have the problem
corrected before further use.
Maintenance procedures
Many maintenance procedures,
including any not detailed
in this manual, will need to
be performed by a qualified
technician for safety. if you
have any doubts about your
ability to safely service the
equipment or engine, have a
qualified technician service the
equipment instead.
engine oil change
caution!
Oil is very hot during opera-
tion and can cause burns. Wait for
engine to cool before changing oil.
Place a drain pan (not included) un-
1.
derneath the crankcase’s drain plug.
Remove the drain plug and, if pos-
2.
sible, tilt the crankcase slightly to help
drain the oil out. Recycle used oil.
Replace the drain plug and tighten it.
3.
Refill the oil to the proper level follow
-
4.
ing the instructions under the Starting
the Engine section.
air Filter element Maintenance
The air cleaner cover is held in place
1.
by a wing nut or clamps. Remove it.
Remove the air filter element.
2.
cleaning:
3.
For “paper” filter elements:
a.
To prevent injury from dust and
debris, wear ANSI-approved safety
goggles, NIOSH-approved dust
mask/respirator, and heavy-duty
work gloves. In a well-ventilated
area away from bystanders, use
pressurized air to blow dust out of
the air filter.
Warning