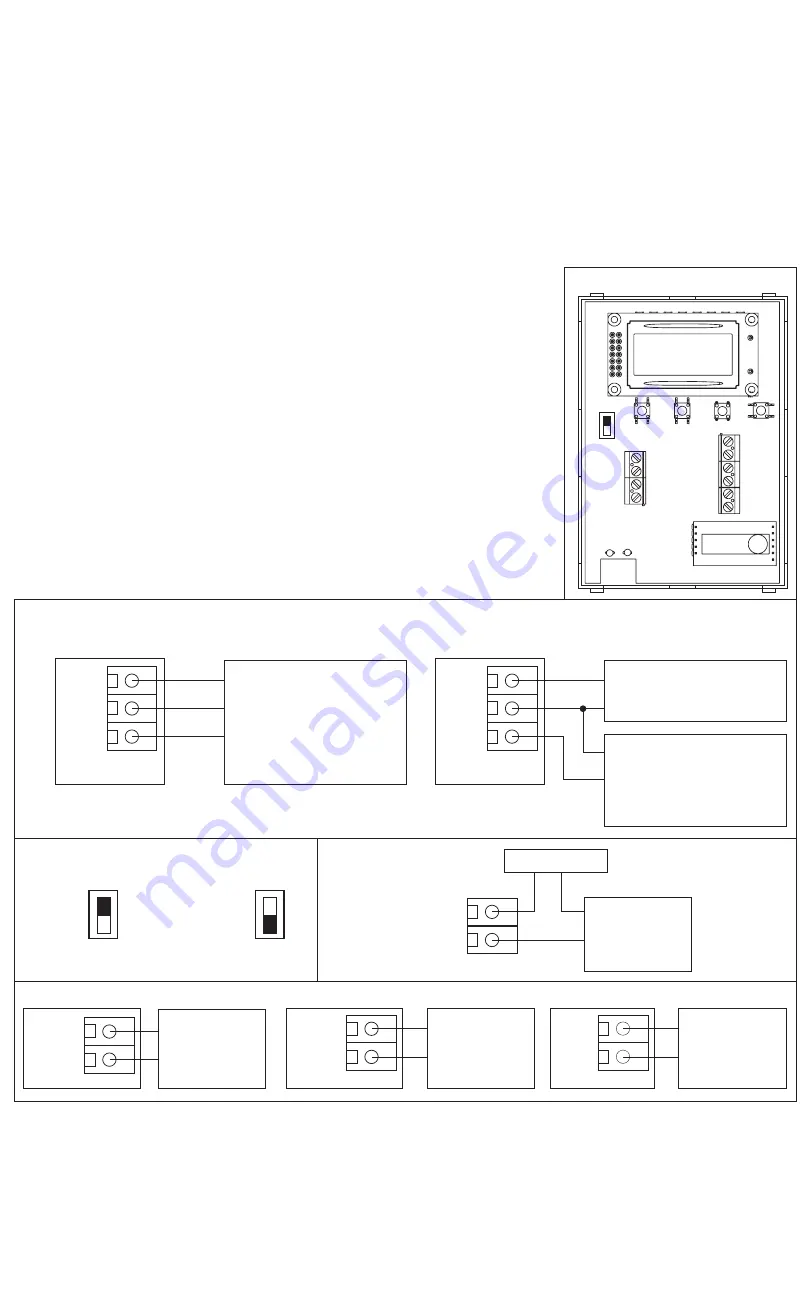
Page 2
The PCB must be removed from the base to access the mounting holes. Follow anti-static procedures when
handling the PCB and be careful not to touch the sensors.
The PCB is removed by pressing the enclosure base to unsnap the latch near the bottom edge, then the PCB
can be lifted out of the base as shown in Figure 3.
Sit the PCB aside until the base is mounted on the wall. For added protection, place the PCB in the supplied
anti-static bag.
Mount the base by screwing to an electrical box or directly to the wall as shown in Figure 4.
After the base is screwed to an electrical box or directly to the wall using the appropriate holes, remove the
PCB from the anti-static bag, feed connection wires through the center hole and place the top of the PCB
into the PCB holders on the backplate and snap the bottom of the PCB into place as shown in Figure 4.
Making wiring connections as per the Wiring Illustrations on page 2 and
install the decorative cover by placing the top of the cover into the cover
holder on the top of the backplate and snapping the bottom into place as
shown in Figure 4. Tighten the security screw with a Phillips screwdriver.
WIRING
Deactivate the power supply until all connections are made to the
device to prevent electrical shock or equipment damage. Use 16-22 AWG
shielded wire for all connections (only ground the shield at the controller
end) and do not locate the device wires in the same conduit with wiring
used to supply inductive loads such as motors. Pull at least six inches of
wire into the enclosure and complete the wiring connection according to
the wiring diagram. Figure 6.
This is a 3-wire sourcing device. Connect the plus DC or the AC voltage
hot side to the PWR terminal and the common is connected to the COM
terminal. The device is reverse voltage protected and will not operate if
connected backwards. It has a half-wave power supply so the supply common is the same as the signal
common. Several devices may be connected to one power supply and the output signals all share the
same common. Use caution when grounding the secondary of a transformer or when wiring multiple
devices to ensure the ground point is the same on all devices and the controller.
The CO
2
analog output is available on the CO
2
terminal. This signal is switch selectable for either 4-20 mA
or voltage output (0-5 / 0-10 Vdc) see Figure 7 and connects to the controller analog input. Check the
controller Analog Input to determine the proper connection before applying power. Both current and
Figure 5
Figure 7
Figure 8
Figure 9
Figure 6
Power Supply
Wiring for CO
2
output signal and
24 Vdc power from controller
Wiring for all output and external 24 Vac power
transformer or external 24 Vac power supply
CO
2
COM
PWR
RELAY
SETPNT
SWITCH
TEMP
CO
2
COM
PWR
Analog Input
COMMON
+24 Vdc
COMMON
Digital Input
Analog Input
COMMON
Digital Input
COMMON
Analog Input
COMMON
Analog Input
COMMON
COMMON
24 Vac
Controller
Alarm
Controller
Controller
Controller
24 Vac Transformer /
Power Supply
mA
VOLT
Current
4-20 mA
Voltage
0-5 or 0-10 Vdc
VOLT
mA
mA
VOLT
SETPNT
CO2
COM
PWR
TEMP
SWITCH
RELAY
MENU
UP
DOWN
OVERRIDE
CO2 SENSOR
Copyright © Greystone Energy Systems, Inc. All Rights Reserved Phone: +1 506 853 3057 Web: www.greystoneenergy.com
IN-GE-CD2RMCXXX-04