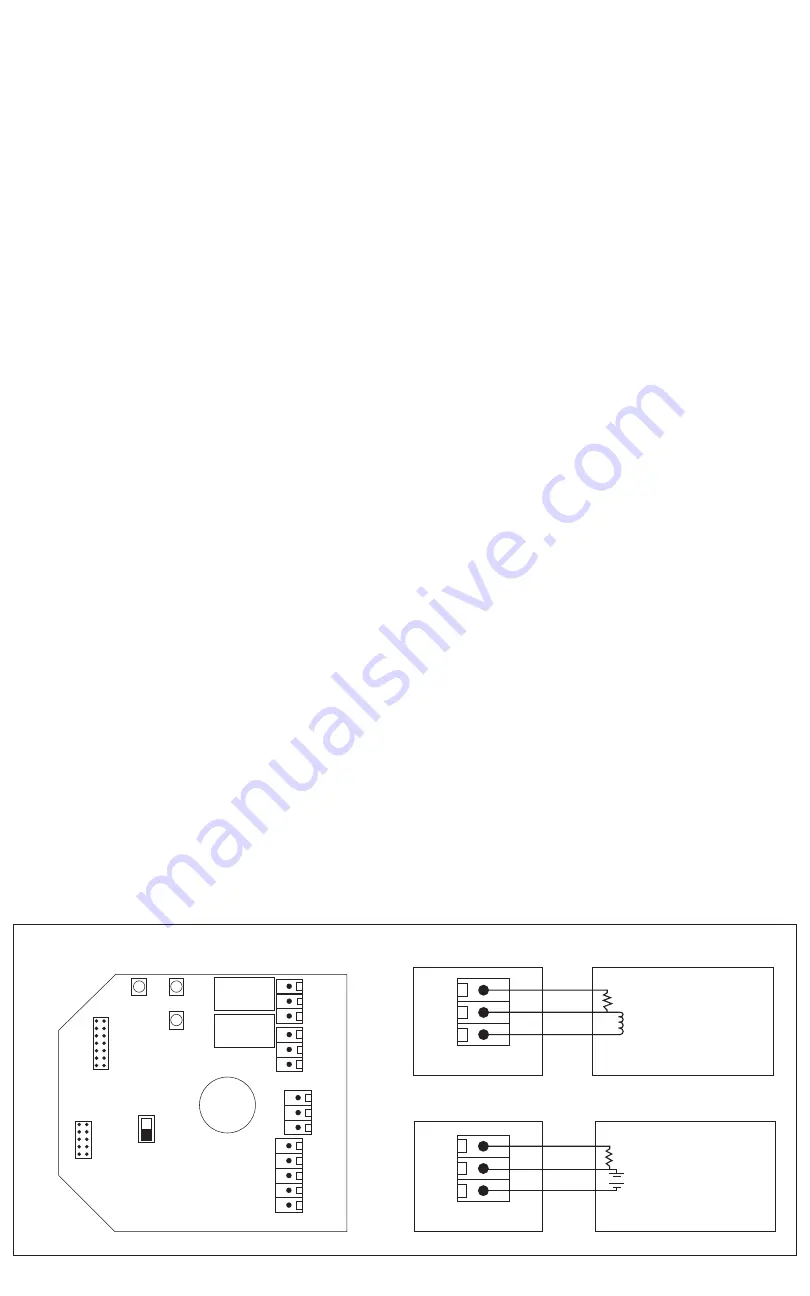
Page 2
POWER AND ANALOG OUTPUT WIRING
Use 22 AWG shielded wire for all connections and do not locate the device wires in the same conduit with
wiring used to supply inductive loads such as motors. Disconnect the power supply before making any
connections to prevent electrical shock or equipment damage. Make all connections in accordance with
national and local codes.
The wiring configuration depends on the specific model and the installed options. Follow the example
wiring diagrams to determine the correct wiring. All models have the same terminal functions. This device
has a half-wave type power supply so the power supply common is the same as the output signal common.
Therefore, several devices may be connected to one power supply and the output signals all share the
same signal common. Use caution when grounding the secondary of an AC transformer or when wiring
multiple devices so that the circuit ground point is the same on all devices and the controller.
This is a 3-wire sourcing device. All models require a 24 Vac/dc power supply to operate. Connect the
positive dc voltage or the hot side of the ac voltage to the ANALOG - PWR terminal and the power supply
common to the ANALOG - COM terminal. Note that the Analog COM terminal is NOT connected to the
Relay COM terminals. The device is reverse voltage protected and will not operate if the power supply is
connected backwards.
The linear output signal (either 4-20 mA or 0-5/10 Vdc) is available on the ANALOG - CO terminal. The
signal is referenced to the Analog COM terminal. The 4-20 mA output signal operates in the Active mode
and does not require a loop power supply. This means the signal current is generated by the transmitter
and must not be connected to a powered input or device damage will result. This is the typical operating
mode of a “three-wire device”. Ensure the controller Analog Input (AI) matches the CO Transmitter output
signal type before power is applied. The current signal has a maximum load that it will drive and the
voltage output has a minimum load. Follow the ratings in the Specification section or inaccurate readings
may result. The power must be disconnected to change from VOLT to mA. The analog output CO signal is
typically connected directly to the Building Automation System (BAS) and used as a control parameter or
for logging purposes.
REMOTE TEST WIRING
The CO Transmitter has a Test function that will test the analog output and the alarm relays which is initiated
by pressing the front panel TEST switch. The Test function may also be initiated remotely by shorting the
TEST + and TEST - terminals. Note that the TEST - terminal is connected to the Analog COM terminal. The
TEST terminals should only be connected to a dry-contact digital output from the controller that is either
shorted or floating open. Ensure no power is applied to the TEST terminals. The TEST terminals may also be
connected to a remote switch. If desired, only one wire need be connected to the TEST + terminal and use
the power supply COM as the return signal path.
ALARM RELAY WIRING
If equipped, the alarm relay outputs are available on the NO, COM and NC terminals for each relay. The
relay COM terminals are NOT connected to the signal or power supply COM terminal nor to each other. The
two relays are completely isolated and have both Normally Open (NO) and Normally Closed (NC) contacts.
These signals can be used to directly control alarms, ventilation fans or may be connected to digital inputs
of the BAS for status monitoring. Ensure any loads connected to the relays are within the relay ratings in
the Specification section.
Figure 4
Analog Input for
4-20 mA CO Signal
24 Vac Power
Controller
CO
COM
PWR
250R
Com
Hot
Analog Input for
0-5 Vdc CO Signal
24 Vdc Power
Controller
CO
COM
PWR
1M
Com
+
Wiring for 4-20 mA Output Signal
Wiring for 0-5 Vdc Output Signal
RELA
Y 1
NC
COM
NO
RELA
Y 2
COMM
LCD
ROLL
MENU
POWER
PCB
VOLT
mA
+
TEST
-
CO
COM
PWR
A-
B+
SHLD
NC
COM
NO
IN-GE-CMD5B5XXX-01-02 03/19
Copyright © Greystone Energy Systems, Inc. All Rights Reserved Phone: +1 506 853 3057 Web: www.greystoneenergy.com