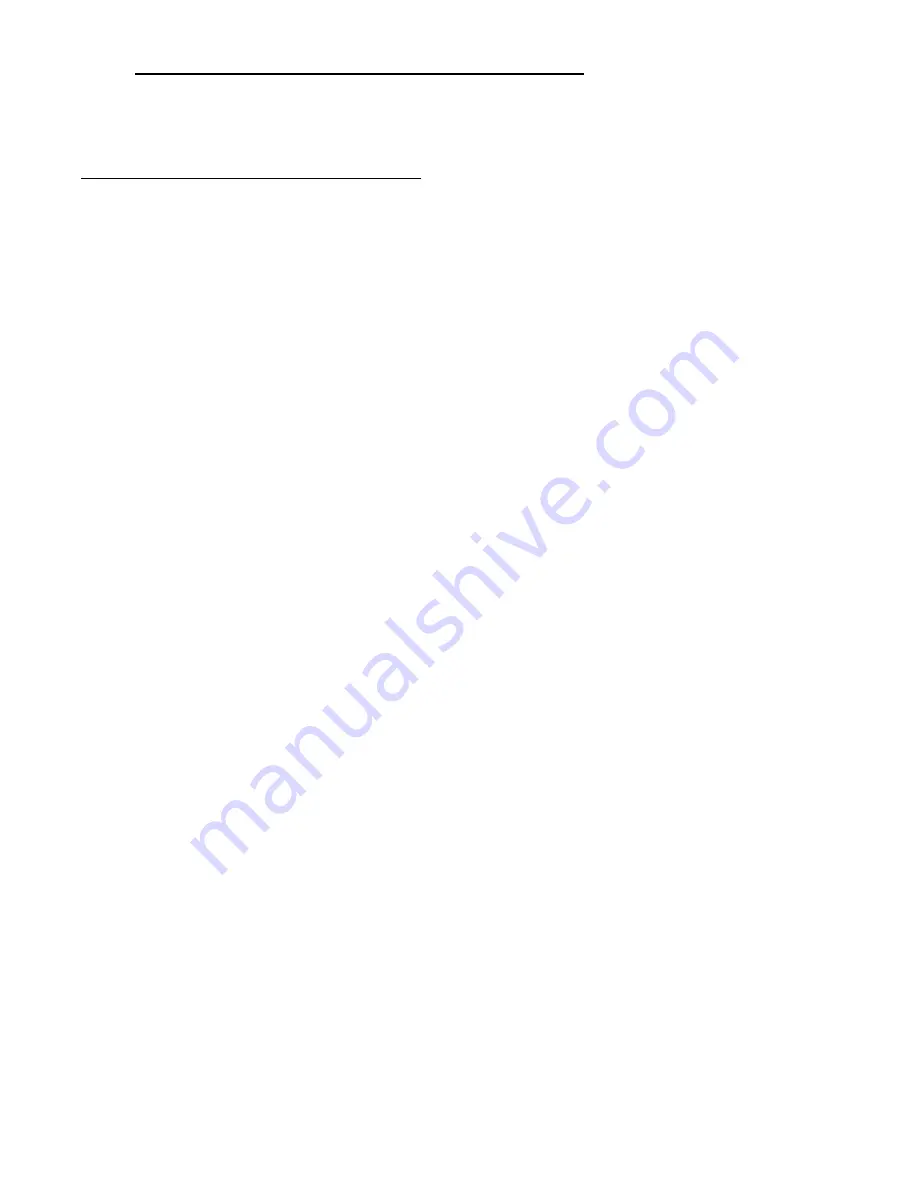
W:\ELECTRICAL\INSTRUCT\FURNACE\FURNACE GENERAL INSTRUCTIONS 2011.DOC
31 of 36
01/2014
11
APPENDIX C - MINIMUM PERIODIC INSPECTION REPORT
Model: _________________________________________________ Serial No.: _________________
Inspected By: ___________________________________________ Date: _________________
BEFORE APPLYING POWER CHECK THAT:
1. ____
No changes in process have been made including types of materials processed and
temperature:
-Furnace originally designed for: _______________________________________________
_________________________________________________________________________
_________________________________________________________________________
-Furnace being used for: _____________________________________________________
_________________________________________________________________________
_________________________________________________________________________
2. ____
If flammable solvents are involved in process, quantity entering furnace and operating
temperature are within furnace design parameters -- see Operating Manual for Safety Design
Form.
-Furnace designed for __________ gallons of solvent (per batch or per hour) at a maximum
of ________°F.
-Furnace being used for __________ gallons of solvent (per batch or per hour) at an
operating temperature of ________°F.
3. ____
All electrical connections are tight without stray strands.
4. ____
All contactors, relays, motor starters and other components with contacts have been
inspected for wear or sticking.
5. ____
Furnace body inspected and painted surfaces touched up to prevent rusting.
6. ____
Furnace interior inspected for component assembly and positioning, cleaned, and all foreign
matter removed from the following. Protect inspecting personnel from dust, see 7-2.
________
Floor
________
Heat chamber (including heating element surfaces)
________
Duct work
________
Air inlets
________
Exhaust outlets
________
Filters
________
Control enclosure and components
________
Door hinges or support mechanism
7. ____
Remove and clean all drip pans. Inspect and clean all work racks, trays, holders or spacers.
Protect inspecting personnel from dust; see 7-2.
8. ____
Locate main temperature controller and excess temperature limit interlock thermocouples;
inspect for damage. Make sure thermocouples are in free air and not touching anything.
9. ____
Top of furnace is clear; no material is stored on top of furnace.
10. ____ Doors are free to move and not obstructed.
11. ____ Exhaust duct work from furnace has been inspected and cleaned; all foreign matter
removed.
12. ____ Fresh air duct work and/or filters have been inspected and cleaned; all foreign matter
removed.
13. ____ Lubricate motors.