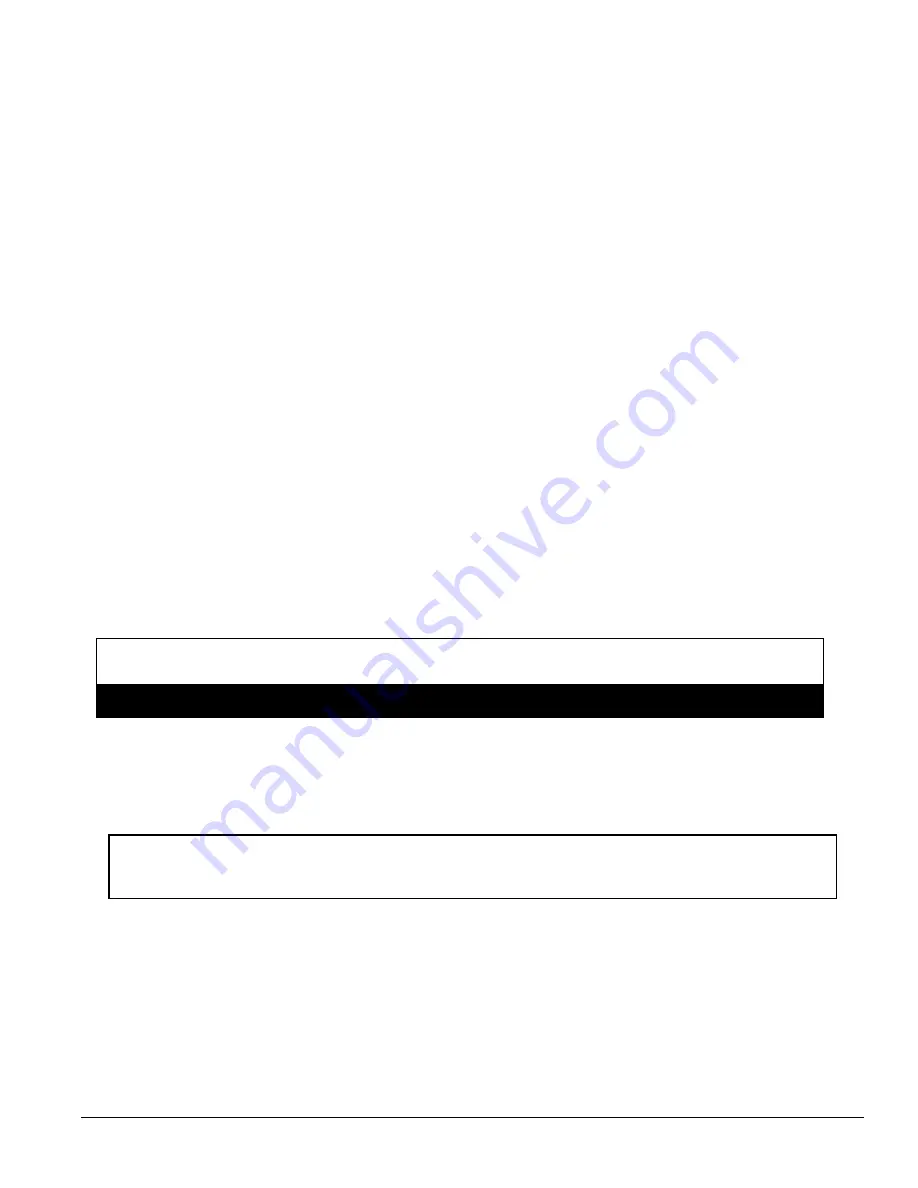
Shuttle Brewers & Airpot/Shuttle Brewers
Page 5
Installation (cont.)
Electric Hook-up
The brewer is designed to operate at the specified voltage on the nameplate with a tolerance of ± 10% for voltage
deviation. It is very important that the power line to the brewer be checked to make sure that the voltage is within
10% of the brewer’s rated voltage. Failure to provide adequate voltage, as defined above, will cause problems
with your brewer. If the power is too low, the solenoid valves may or may not work or longer recovery time will be
experienced. The brewer may be permanently damaged if the voltage is too high.
1) The electric ratings for your brewer are printed on its nameplate.
2) The brewer should be connected to its own circuit with a fused disconnect switch or a circuit breaker near the brewer.
Important:
For CE units, means shall be provided to endure all pole disconnection from the supply. Such means shall be
one of the following: a supply cord fitted with plug, or a switch that is directly connected to the supply terminals and has a
contact separation of at least 3mm in each pole.
3) Attach the appropriately sized cord to the brewer with a cord grip for the 1 1/2” (3.8 cm) electric input opening.
The cord may enter through the rear or bottom on the left side of the brewer. Use an oil resistant cord such as
type SO, SOO, SAO, STOO, SEO, SJO, SJOO, SJTO, SJTOO, SJEO, HSO, HSOO, HSJO, or HSJOO.
Alternatively, flexible conduit and type THHN wires may be used. Use only copper conductors.
4) Standard connection is 1 phase 3 wire. Connect the two lines to L1 and L2 on the terminal block. If the brewer is
wired for three phase, a lug, L3, is provided on the terminal block. A neutral line must be connected to the N terminal.
Note:
PB-xxxE 230V models are 1 phase, 2 wire or 3 phase, 3 wire and do not require a neutral.
5) The body of the brewer must be grounded. A ground lug is provided for this purpose.
Note:
If supply cord is damaged, it must be replaced by a special cord or assembly from the manufacturer, ot it’s
service agent.
Note:
This appliance is IP10 rated, and shall not be cleaned with a water jet.
WARNING
Never use the ground conductor as a neutral. This could cause electrocution.
Start-up
1) Flip power supply to machine “ON” at the branch supply disconnect and allow the water tank to fill. The machine
will make a subtle hissing sound while filling.
2) Once the brewer is full, it will take 15 to 35 minutes to heat. The ready lights will turn on when up to temperature.
3) Insert the brew baskets and place a Shuttle or airpot under the baskets. Brew at least one batch from each side.
Check the level in the container to be sure the brew volume is correct. Remember that when using coffee, the
level will be lower. Do this for all batch sizes. The water must be hot to check the levels. If adjustments are needed,
see the adjustments section of this manual.
Attention: A watchdog circuit also monitors the water level in the tank and will disable the machine
if the water level in the tank is not normal within (6) minutes of fill time. The machine will require
power to be reset to clear the watchdog timeout and “ER-1” message will appear.