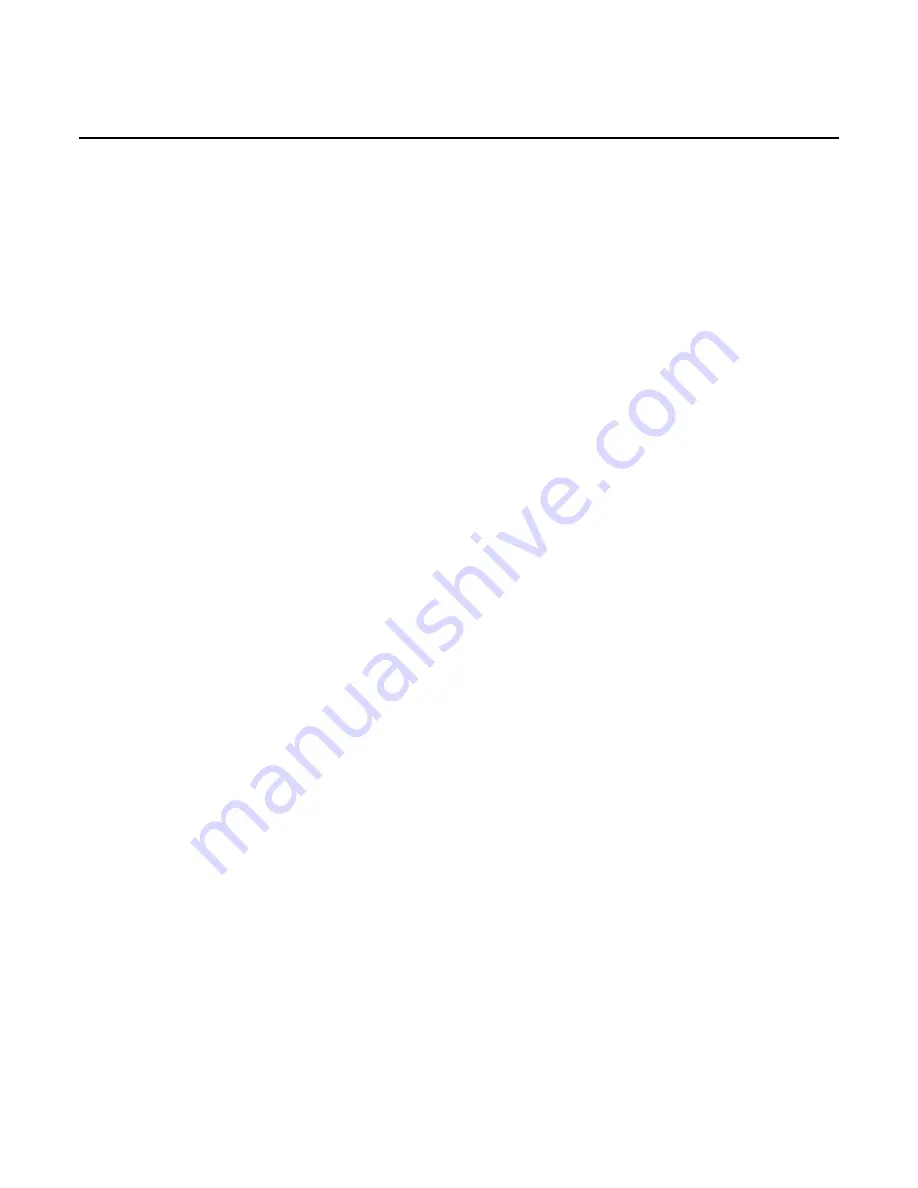
SAFETY INSTRUCTIONS
DO NOT TAMPER WITH COMPRESSOR PRESSURE SWITCH SETTINGS
- The pressure
switch settings set at the factory provide the maximum safe operating pressure recommended
for this compressor. Altering these settings can result in over-pressurization, risk of tank,
hose, and pneumatic equipment failure, and serious injury to operator and bystanders.
USE AIR HOSE RATED FOR 150 PSI OR GREATER
- Air hose must be rated to safely
handle maximum compressor pressure. Air hose that does not meet minimum pressure
requirements can rupture, releasing high pressure air. Replace a cracked or leaking air hose
immediately to prevent serious injury from contact with high pressure air streams.
SHUT OFF COMPRESSOR AND RELIEVE TANK PRESSURE BEFORE SERVICING UNIT
–
Never perform service or maintenance on any part of the compressor while the unit is running
or tanks are pressurized. Open tank drains slowly to allow air to escape, and keep clear of air
stream.
DO NOT MODIFY COMPRESSOR
– Altering the compressor in any way may create a serious
safety hazard, and result in serious injury to operator and bystanders. If compressor does not
work properly, stop using unit immediately. Return unit to an authorized service center for
repairs if problem cannot be remedied by following troubleshooting instructions in this manual.
DO NOT USE COMPRESSED AIR FROM THE UNIT FOR BREATHING PURPOSES
- Air
produced by this compressor may contain poisonous exhaust gases from the engine, and is
not suitable for breathing purposes.
DO NOT LEAVE COMPRESSOR RUNNING UNATTENDED
- Shut compressor off when done,
and disconnect air hoses to prevent unauthorized use of compressor. Drain air tanks if unit is
to be stored or transported.
CONNECT COMPRESSOR POWER CORD ONLY TO A PROPERLY GROUNDED POWER
OUTLET USING AN APPROVED 3-PRONG GROUNDED EXTENSION CORD -
Using an
improperly grounded outlet or extension cord can result in shock or electrocution. Electrical
wiring, outlets, extension cords, and current protection devices such as fuses and circuit
breakers must meet local electrical and safety codes, as well the requirements of the National
Electrical Code. A ground-fault circuit interrupter (GFCI) device may be required for
compressor use outdoors, in garages, and in damp locations.
USE AN EXTENSION CORD THAT IS PROPERLY SIZED -
Using an undersize cord can
result in overheating of cord and short-circuiting, resulting in fire and damage to property. Use
a UL-listed extension cord rated to safely handle the power requirements of the compressor.
Cord
Length
Wire Gauge Size
Up to 25 ft.
12 ga.
Up to 100 ft.
10 ga.
Up to 150 ft.
8 ga.
Up to 250 ft.
6 ga.
4