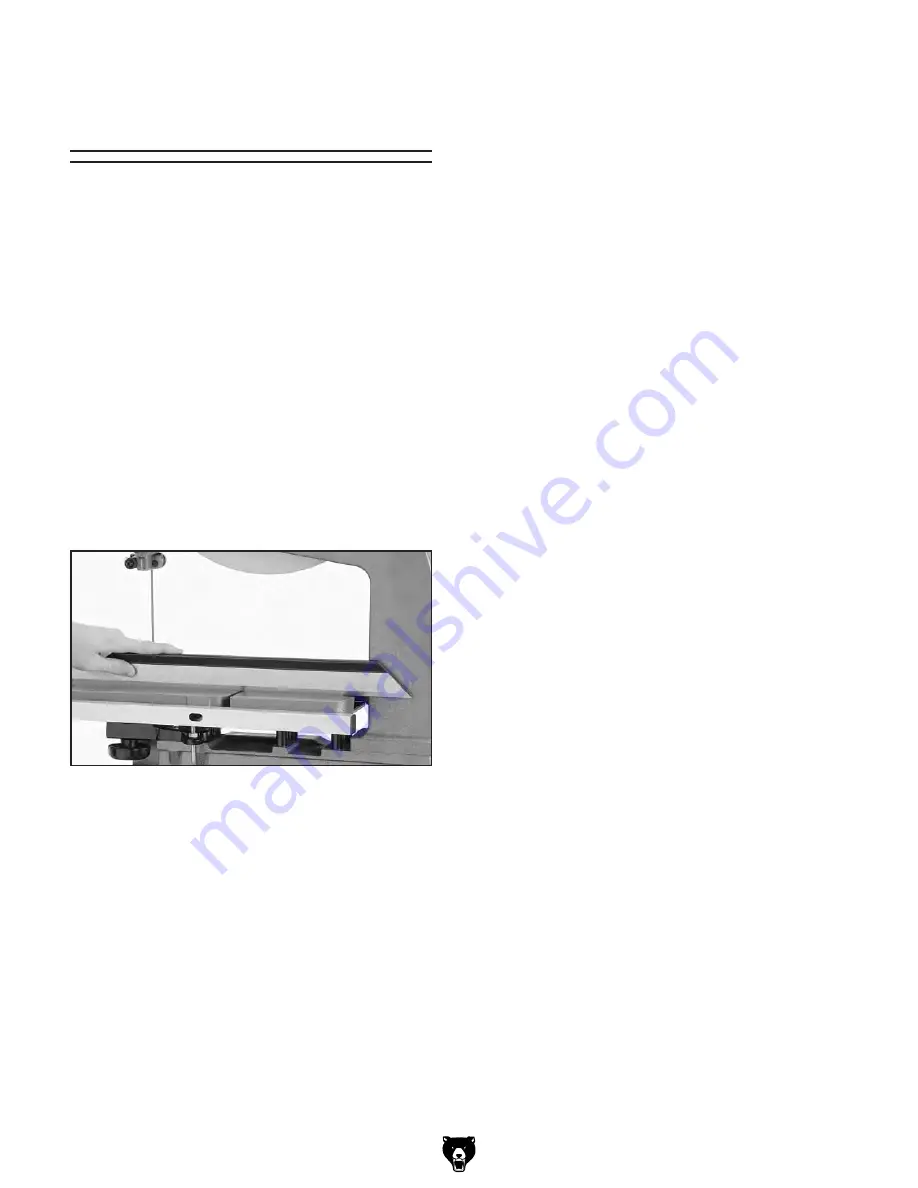
-24-
g0555X
(Mfg. since 1/12)
the extension table must be level with the main
table. it is important to keep the extension table at
least
1
⁄
8
" away from the main table during leveling
to allow the table room for tilting.
To level the extension table:
1. set the table to 90°.
2. locate the lever board set screws under-
neath the extension table (see
figure 10 on
page 16) and loosen the hex nuts on the set
screws. this will allow you to adjust the set
screws when leveling the extension table.
3. place a straightedge across the front of the
main table and extension table as shown in
figure 26.
Leveling Extension
Table
4. adjust the two front setscrews in the lever
board until the extension table is even with
the main table.
5. place a straightedge across the rear of the
main table and extension table.
6. adjust the two front setscrews in the lever
board until the extension table is even with
the main table.
7. repeat Steps 3–4.
8. repeat Steps 5–6.
9. tighten the cap screws that secure the exten-
sion table to the lever board.
10. Verify that the extension table did not move
during tightening and adjust if necessary.
11. tighten the hex nuts, loosened in Step 2,
against the lever board so the set screws
cannot vibrate out of adjustment.
figure 26. leveling extension table with
straightedge.