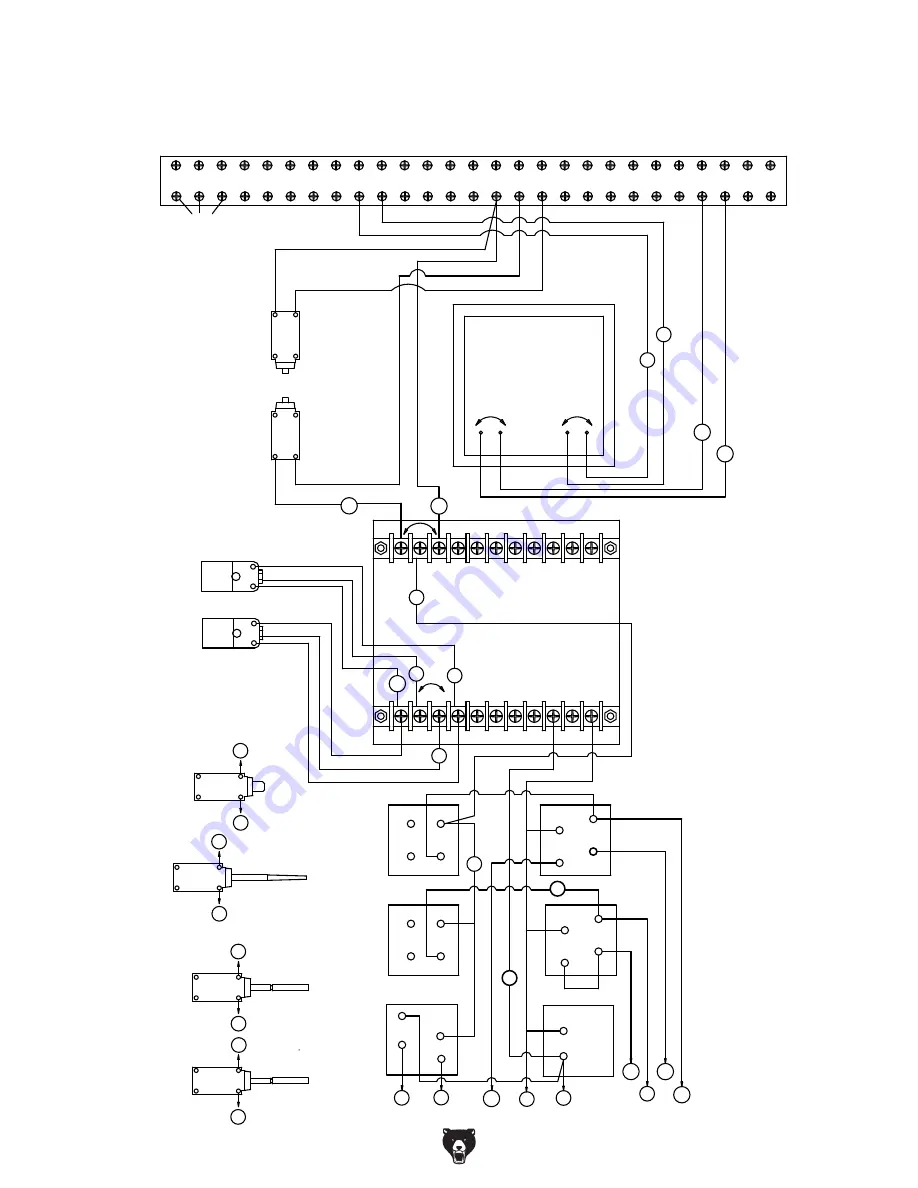
-44-
H2933/H2934/G0447/G0581 Wide Belt Sander
DIGITAL AMP
METER
DIGITAL PANEL
SANDING
BELT START
SWITCH
SANDING
BELT STOP
SWITCH
BLUE
BLAC K
3
1
4
2 1
4 3
2
14
14
14
13
13
13
21
21
22
22
X1
X2
8
6
2
3
10
U1 V1 W1 U2 V2 W2
2
3 3
8
8 4
5 22 23 6
9 10 11 12
14 15
7
4
12V
OV
B
X1
X2
9
14
13
21
22
X1
X2
14
13
13
20 21
5
1
2
4
3
8
3
2
3
14
15
11 10 9 8 7 6 5 4 3 2 1
12 13 14 15 16 17 18 19 20 21 22
7
1
2
4
3
8
3
CONVEYOR
BELT START
SWITCH
POWER
LAMP
EMERGENCY
STOP
BUTTON
CONVEYOR
BELT STOP
SWITCH
EMERGENCY STOP
PUSH-PANEL LIMIT
SWITCH
1
3
2
4
1
2
3
4
8
3
8
3
BELT TENSION
LIMIT
SWITCH
BELT TRACKING
LIMIT
SWITCH
BELT TRACKING
LIMIT
SWITCH
TABLE UP/DOWN
SAFETY LIMIT
SWITCH
TABLE UP/DOWN
SAFETY LIMIT
SWITCH
OUT TO
SANDING MOTOR
TABLE HEIGHT SENSOR
BLUE
BLAC K
A
12
11
13
3
9
Control Panel Electrical Diagram
(G0581)
Summary of Contents for G0447
Page 22: ......
Page 24: ......
Page 40: ... 16 H2933 H2934 G0447 G0581 Wide Belt Sander 5mm Hardware Chart ...
Page 69: ...H2933 H2934 G0447 G0581 Wide Belt Sander 45 Notes ...
Page 105: ......