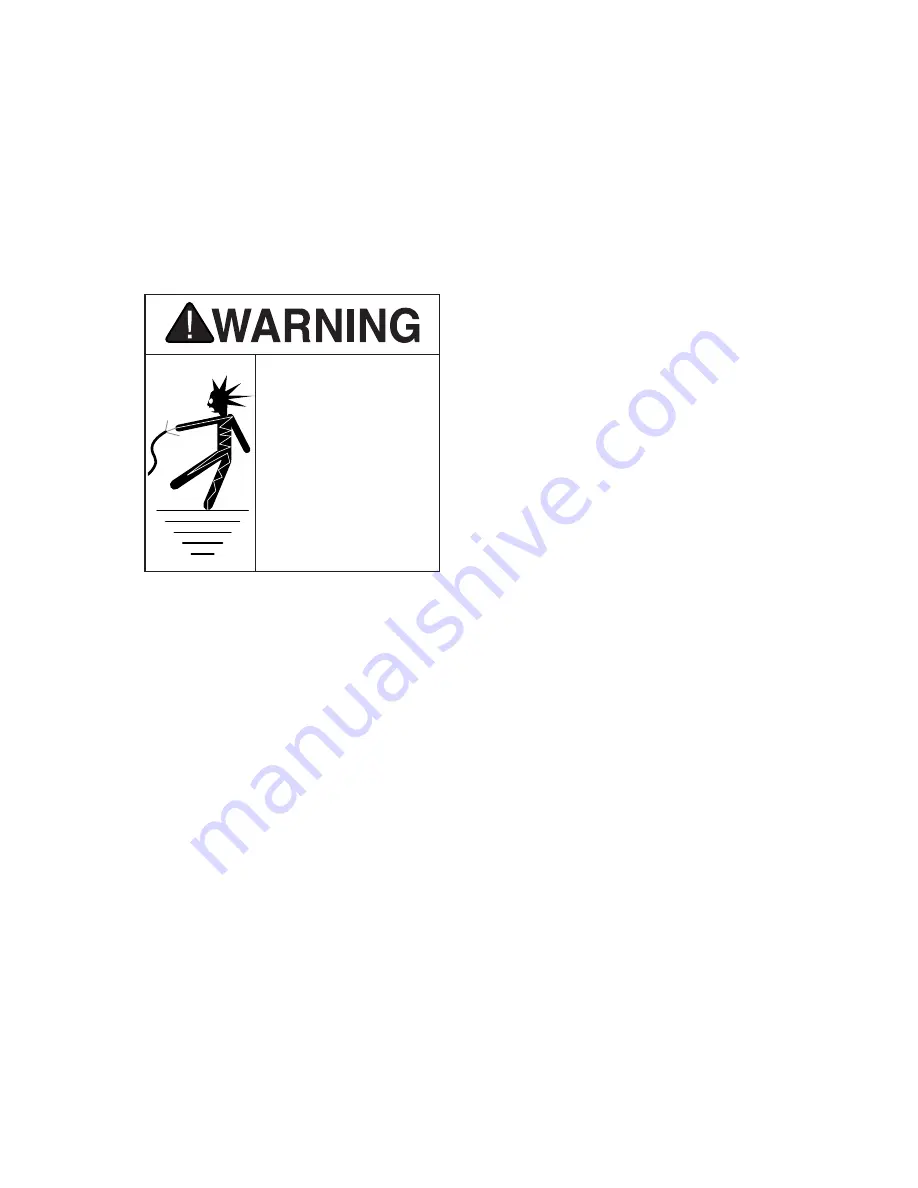
Model G0464/G0465/G0467/G0468/G0470 Air Compressors
-
8
-
Extension Cords
The use of extension cords can cause
power loss and overheating in air com-
pressors. When possible, locate the air
compressor where it can be plugged into
an outlet without the use of an extension
cord, and use an additional air hose to
reach the work area.
If you find it necessary to use an exten-
sion cord with your machine:
• Make sure the cord is rated Standard
Service (grade S) or better.
• The extension cord must contain a
ground wire and plug pin.
• Use at least a 14 gauge cord. Use a
12 gauge cord if the cord is between
25-100 feet.
• DO NOT use extension cords over 100
feet.
Electrocution
or
fire could result if
this machine is not
grounded correctly or
if your electrical con-
figuration does not
comply with local and
state codes. Ensure
compliance by check-
ing with a qualified
electrician!
Grounding
In the event of an electrical short, ground-
ing reduces the risk of electric shock. The
grounding wire in the power cord must
be properly connected to the grounding
prong on the plug; likewise, the outlet
must be properly installed and grounded.
All electrical connections must be made
in accordance with local codes and ordi-
nances.
Summary of Contents for G0464
Page 2: ......
Page 24: ...Model G0464 G0465 G0467 G0468 G0470 Air Compressors 22 G0464 Parts Breakdown ...
Page 26: ...Model G0464 G0465 G0467 G0468 G0470 Air Compressors 24 G0465 Parts Breakdown ...
Page 28: ...Model G0464 G0465 G0467 G0468 G0470 Air Compressors 26 G0467 Parts Breakdown ...
Page 30: ...Model G0464 G0465 G0467 G0468 G0470 Air Compressors 28 G0468 Parts Breakdown ...
Page 32: ...Model G0464 G0465 G0467 G0468 G0470 Air Compressors 30 G0470 Parts Breakdown ...