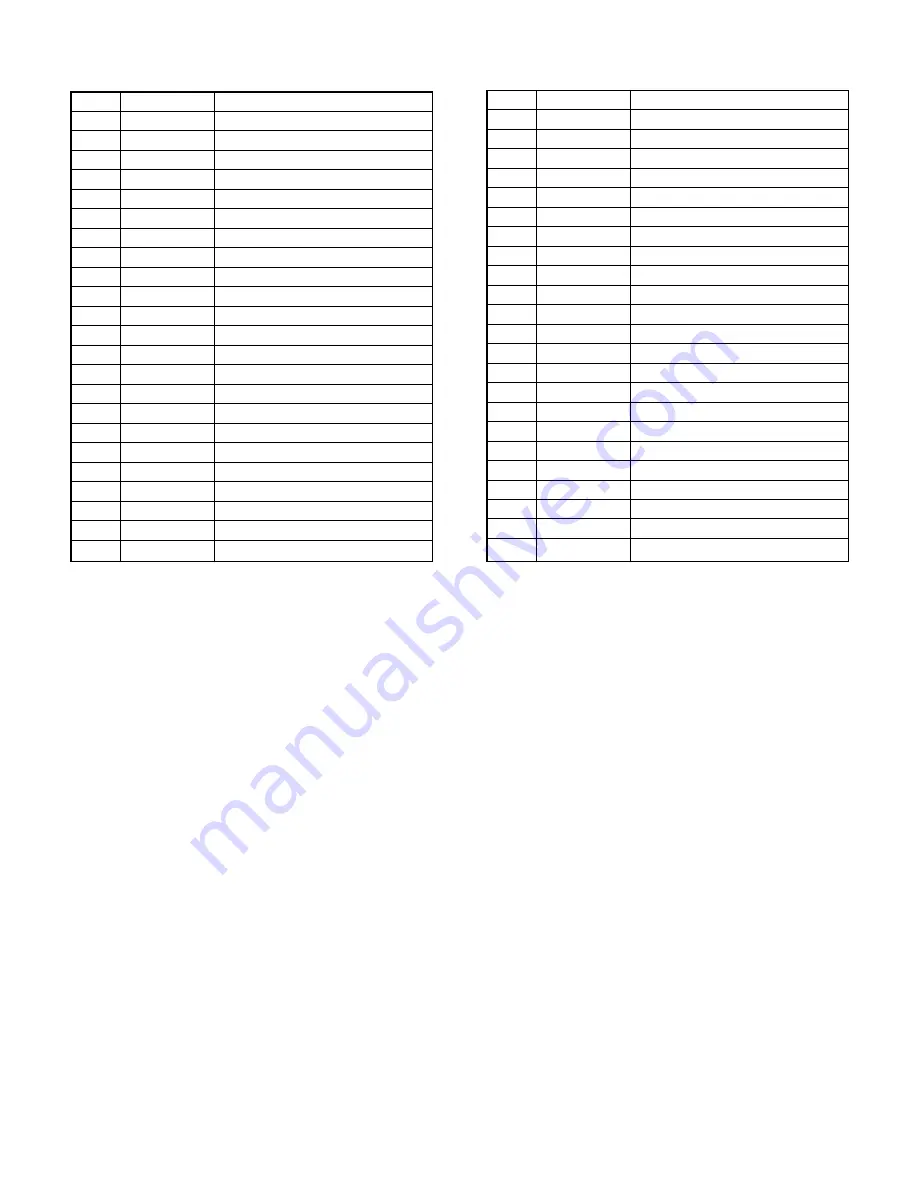
G0516 Lathe/Mill
-61-
REF
PART #
DESCRIPTION
901
PB26M
HEX BOLT M8-1.25 X 30
902
PW01M
FLAT WASHER 8MM
903
P0516903
AC MOTOR
904
PK02M
KEY 5 X 5 X 40
905
P0516905
MOTOR SHAFT SPACER
906
P0516906
DRIVE PULLEY
907
P0516907
KEYWAY SHAFT SPACER
908
P0516908
MOTOR PULLEY
909
P0516909
CHECK RING
910
PS62M
PHLP HD SCR M6-1.0 X 30
911
P0516911
OIL CUP 6MM
912
P0516912
GREAT WASHER
913
P0516913
COUNTER PULLEY
914
P0516914
SLIDE BEARING
915
P0516915
ARM SHAFT
916
P0516916
BEARING ARBOR
917
P0516917
TENSION PULLEY
918
P6001
BEARING 6001
919
P0516919
SPACER
920
PLW03M
LOCK WASHER 6MM
921
PR03M
EXT RETAINING RING 12MM
922
PR19M
EXT RETAINING RING 28MM
923
P0516923
PIVOT
924
P0516924
PIVOT SPACER
REF
PART #
DESCRIPTION
925
PW04M
FLAT WASHER 10MM.
926
PN02M
HEX NUT M10-1.5
927
PS59M
PHLP HD SCR M3-.5 X 14
928
PB07M
HEX BOLT M8-1.25 X 25
929
PS05M
PHLP HD SCR M5-.8 X 8
930
P0516930
FAN-SUPPORT
931
P0516931
ADJ SLOT SPACER
932
PS31M
PHLP HD SCR M6-1.0 X 35
933
PB32M
HEX BOLT M10-1.5 X 25
934
PN06M
HEX NUT M5-0.8
935
P0516935
PULLEY SUPPORT
936
P0516936
MOTOR COVER
937
PS14M
PHLP HD SCR M6-1 X 12
938
P0516938
ARM SHAFT NUT
939
P0516939
SOCKET OUTLET
940
P0516940
SUPPORT SPACER
941
PS12M
PHLP HD SCR M3-.5 X 6
942
P0516942
ELECTRIC TOP COVER
943
PLW04M
LOCK WASHER 8MM
944
P0516944
TIMING BELT 1.5 X 124 X 15MM
945
PVM30
V-BELT M-30 3L300
946
PN06M
HEX NUT M5-0.8
947
P0516947
MAIN POWER SOCKET
948
PLABEL-14 ELECTRICITY LABEL