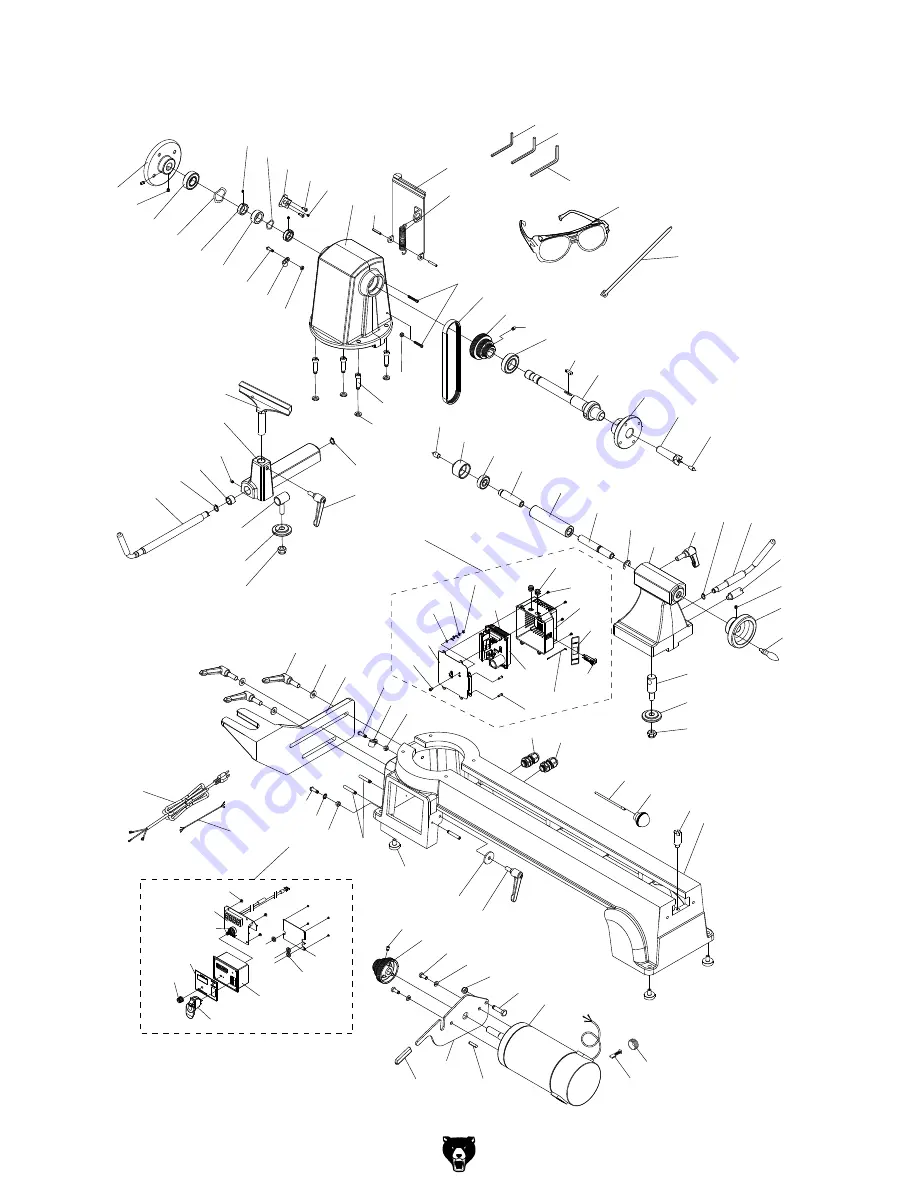
Models G0657/G0658 (Mfg. Since 5/13)
-43-
G0658 Main
26
27
30
31
32
33
94
95
9
8
7
6
5
3
1
19
20
22
24
25
10
14
12
21
23
28
29
48
51
49
50
52
53
45
46
38
34
35
36
37
39
41
42
43
44
46
38
45
40
2
2
54
68
73
74
74-1
74-2
75
78
41
67
65
61
72
21
76
79
55
56
59
63
11
10
81
81-1
80
4
82
7
7
2
9
18
16
17
15
58
62
9
64
60
8
9
64
51
13
69
57
58-3
58-1
58-13
58-5
58-8
58-11
58-2
58-6
58-12
58-4
58-9
58-7
58-10
63-3
63-4
63-2
63-6
63-5
63-9
63-1
63-8
63-7
87
88
89
86
Summary of Contents for G0657
Page 52: ......