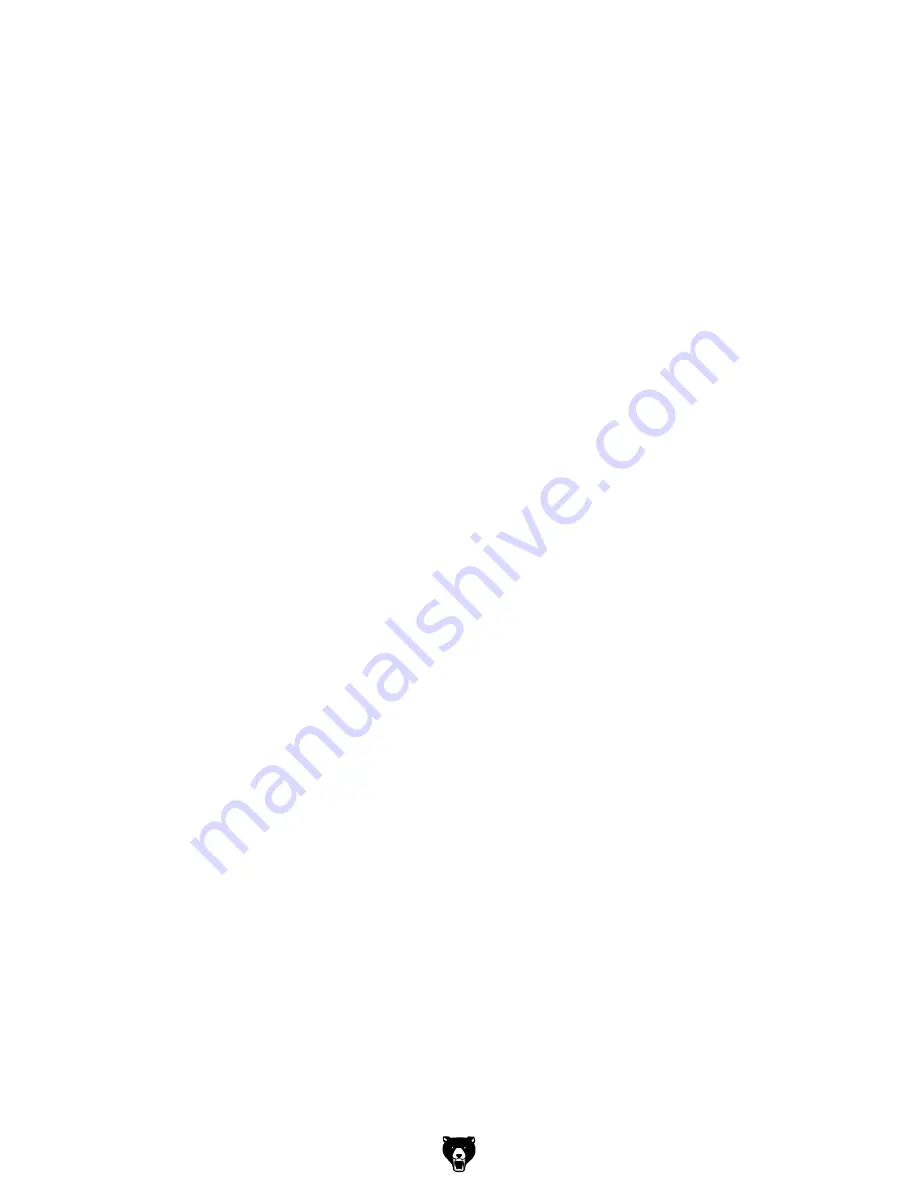
Model G0690/G0691 (Mfd. 6/15+)
-5-
The information contained herein is deemed accurate as of 11/29/2015 and represents our most recent product specifications.
Due to our ongoing improvement efforts, this information may not accurately describe items previously purchased.
PAGE 2 OF 3
Model G0690
Main Specifications:
Main Information
Table Saw Type..................................................................................................................................... Cabinet
Maximum Blade Diameter......................................................................................................................... 10 in.
Arbor Size................................................................................................................................................. 5/8 in.
Arbor Speed...................................................................................................................................... 4300 RPM
Maximum Width of Dado...................................................................................................................... 13/16 in.
Blade Tilt Direction....................................................................................................................................... Left
Max Blade Tilt......................................................................................................................................... 45 deg.
Maximum Depth of Cut At 90 Degrees.................................................................................................. 3-1/8 in.
Maximum Depth of Cut At 45 Degrees................................................................................................ 2-3/16 in.
Max Rip Right of Blade w/Included Fence & Rails.............................................................................. 29-1/2 in.
Max Rip Left of Blade w/Included Fence & Rails....................................................................................... 12 in.
Additional Blade Information
Included Blade Information.................................................................................................................. 10" x 40T
Riving Knife/Spreader Thickness.......................................................................................................... 0.100 in.
Required Blade Body Thickness.............................................................................................. 0.071 – 0.094 in.
Required Blade Kerf Thickness............................................................................................... 0.102 – 0.126 in.
Rim Speed at Max Blade Diameter................................................................................................. 11,300 FPM
Table Information
Floor to Table Height................................................................................................................................. 34 in.
Table Size with Extension Wings Width.................................................................................................... 40 in.
Table Size with Extension Wings Depth.................................................................................................... 27 in.
Distance Front of Table to Center of Blade......................................................................................... 17-1/4 in.
Distance Front of Table to Blade At Maximum Cut............................................................................. 12-1/4 in.
Main Table Size Thickness.................................................................................................................... 1-1/2 in.
Fence Information
Fence Type.................................................................................................... Camlock T-Shape w/HDPE Face
Fence Size Length..................................................................................................................................... 48 in.
Fence Size Width.................................................................................................................................. 4-1/8 in.
Fence Size Height................................................................................................................................. 2-1/2 in.
Fence Rail Type................................................................................................................. Square Steel Tubing
Fence Rail Length...................................................................................................................................... 62 in.
Fence Rail Width................................................................................................................................... 2-3/4 in.
Fence Rail Height........................................................................................................................................ 2 in.
Miter Gauge Information
Miter Gauge Slot Type.............................................................................................................................. T-Slot
Miter Gauge Slot Size Width..................................................................................................................... 3/4 in.
Miter Gauge Slot Size Height................................................................................................................... 3/8 in.
Construction
Table....................................................................................................................... Precision-Ground Cast Iron
Wings...................................................................................................................... Precision-Ground Cast Iron
Cabinet................................................................................................................................... Pre-Formed Steel
Trunnions............................................................................................................................................. Cast Iron
Fence Assembly................................................................................................... Steel with HDPE Side Plates
Rails........................................................................................................................................................... Steel
Miter Guage Construction............................................................................................. Cast Iron with Steel Bar
Guard............................................................................................................................. Steel and Clear Plastic
Body/Cabinet Paint Type/Finish................................................................................................ Powder Coated
Arbor Bearings.............................................................................................. Sealed & Permanently Lubricated
Other Related Information
Number of Dust Ports....................................................................................................................................... 1
Dust Port Size.............................................................................................................................................. 4 in.
Compatible Mobile Base........................................................................................................................ D2057A
Summary of Contents for G0690
Page 20: ...18 Model G0690 G0691 Mfd 6 15 Hardware Recognition Chart...
Page 92: ......