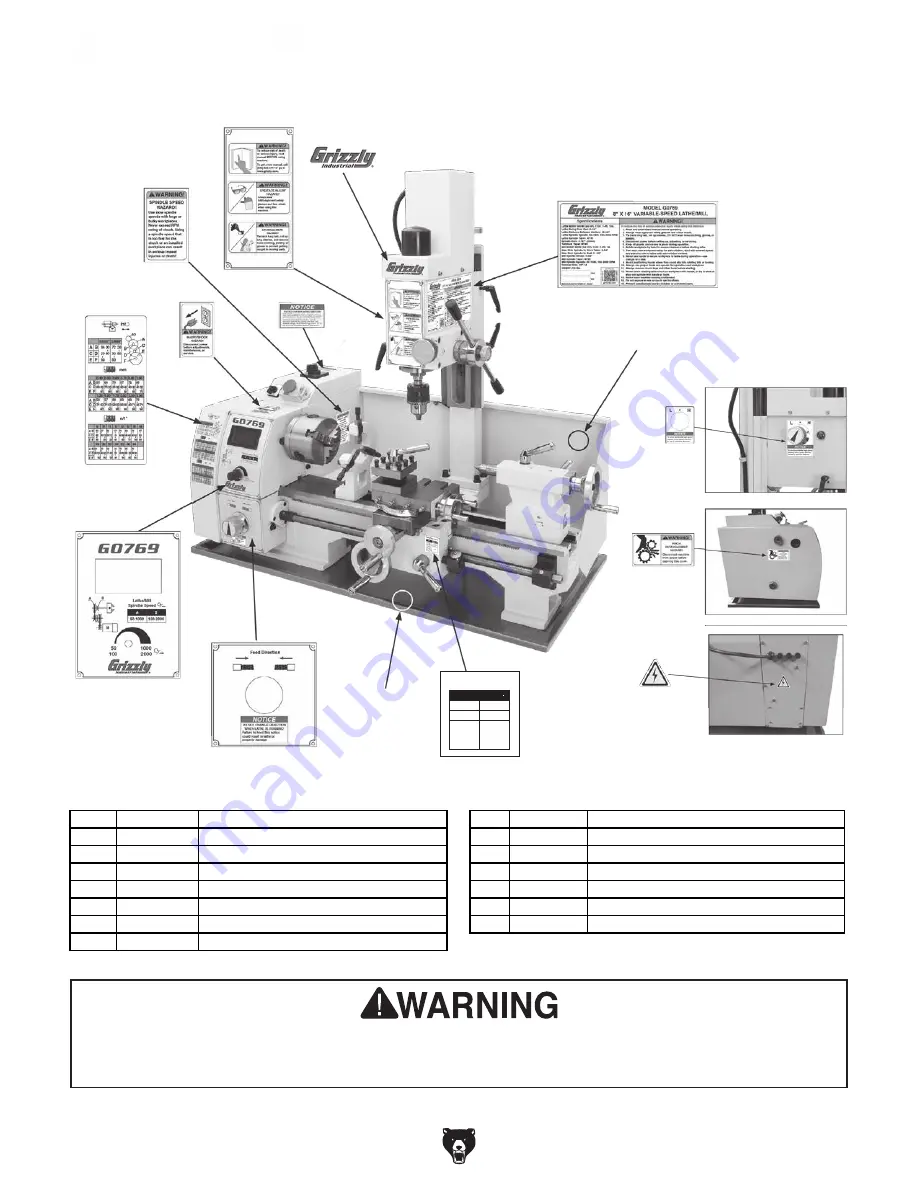
801
802
803V2
804
805
806
807
808
809
810
815
811
INDICATOR TABLE
TPI
Odd
Even
12, 16,
20, 24,
32, 40, 44
1, 3, 5, 7
1–8
1, 5
SCALE
G0769 Labels & Cosmetics
REF
PART #
DESCRIPTION
REF PART #
DESCRIPTION
801
P0769801
MACHINE ID LABEL
809
P0769809
SPINDLE SPEED HAZARD LABEL
802
P0769802
GRIZZLY PUTTY TOUCH-UP PAINT
810
P0769810
COMBO WARNING LABEL
803V2 P0769803V2 THREAD DIAL CHART V2.04.16
811
P0769811
GRIZZLY LOGO LABEL (RED)
804
P0769804
GRIZZLY GREEN TOUCH-UP PAINT
812
P0769812
LOW/HI SPEED LABEL
805
P0769805
FEED DIRECTION LABEL
813
P0769813
ENTANGLEMENT HAZARD LABEL
806
P0769806
CONTROL PANEL LABEL
814
P0769814
ELECTRICITY LABEL
807
P0769807
GEAR CONFIGURATION CHART LABEL
815
P0769815
OVERHEATING MOTOR NOTICE LABEL
808
P0769808
DISCONNECT POWER WARNING LABEL
Safety labels help reduce the risk of serious injury caused by machine hazards. If any label comes
off or becomes unreadable, the owner of this machine MUST replace it in the original location
before resuming operations. For replacements, contact (800) 523-4777 or www.grizzly.com.
812
813
814
812
813
814
812
813
814
Model G0768/G0769 (Mfd. Since 8/15)
-107-