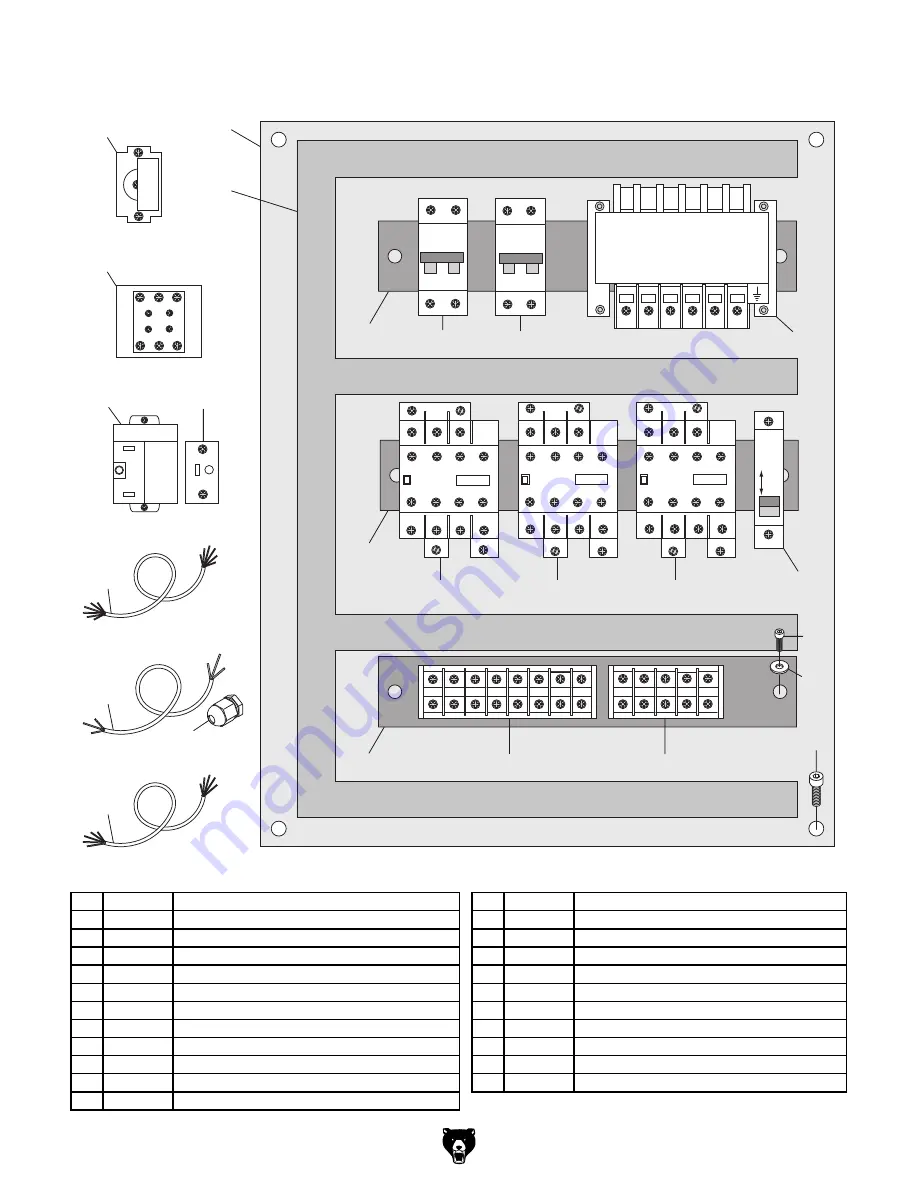
Model G0792 (Mfd. Since 12/15)
-33-
PE
L1
L2
PE
U1
V1
U2
V2
PE
L1
L2
PE
U1
V1
U2
V2
3
4
6
7
20
3
4
6
7
20
ON
OFF
C3
1L1
22E
3L2
5L3
43NO
31NC
21NC
13NO
14NO
22NC
32NC
44NO
6T3
4T2
3TB41
2T1
CHNT
1L1
22E
3L2
5L3
43NO
31NC
21NC
13NO
14NO
22NC
32NC
44NO
6T3
4T2
3TB41
2T1
1L1
22E
3L2
5L3
43NO
31NC
21NC
13NO
14NO
22NC
32NC
44NO
6T3
4T2
3TB41
2T1
0
220 400 415
0
24
202
203
205
206
207
208
211
212
212
212
213
217
218
219
220
221
222
1NC
201
T1
T2
T3
L1
L2
L3
204
214
209
NO
3
4
210
216
215
223
Electrical Panel
REF PART #
DESCRIPTION
REF PART #
DESCRIPTION
201 P0792201 E-STOP BUTTON ANIUEC LA158-BE102
213 P0792213 CIRCUIT BREAKER 3A CHNT DZ47-60 C3 1P
202 P0792202 ELECTRICAL PANEL MOUNTING PLATE
214 P0792214 FOOT SWITCH CORD 12G 6W 60"
203 P0792203 WIRE RACEWAY
215 P0792215 POWER CORD 12G 3W 72"
204 P0792204 POWER SWITCH E&E LW8GS-25/30000
216 P0792216 MOTOR CORD 12G 5W 48"
205 P0792205 DIN RAIL (UPPER)
217 P0792217 DIN RAIL (LOWER)
206 P0792206 CIRCUIT BREAKER 10A CHNT DZ47-60 D10 2P
218 P0792218 TERMINAL BAR 8P
207 P0792207 CIRCUIT BREAKER 3A CHNT DZ47-60 C3 2P
219 P0792219 TERMINAL BAR 5P
208 P0792208 TRANSFORMER BEIJ AOHENGDA JB/T555
220 P0792220 CAP SCREW M4-.7 X 8
209 P0792209 POWER LAMP ANUIEC LA158-BW 24V
221 P0792221 FLAT WASHER 4MM
210 P0792210 POWER BUTTON ANIUEC LA158-BE101
222 P0792222 CAP SCREW M6-1 X 12
211 P0792211 DIN RAIL (MIDDLE)
223 P0792223 STRAIN RELIEF M20-2 TYPE-3
212 P0792212 CONTACTOR SIEMENS 3TB41 22-0X
Summary of Contents for G0792
Page 44: ......