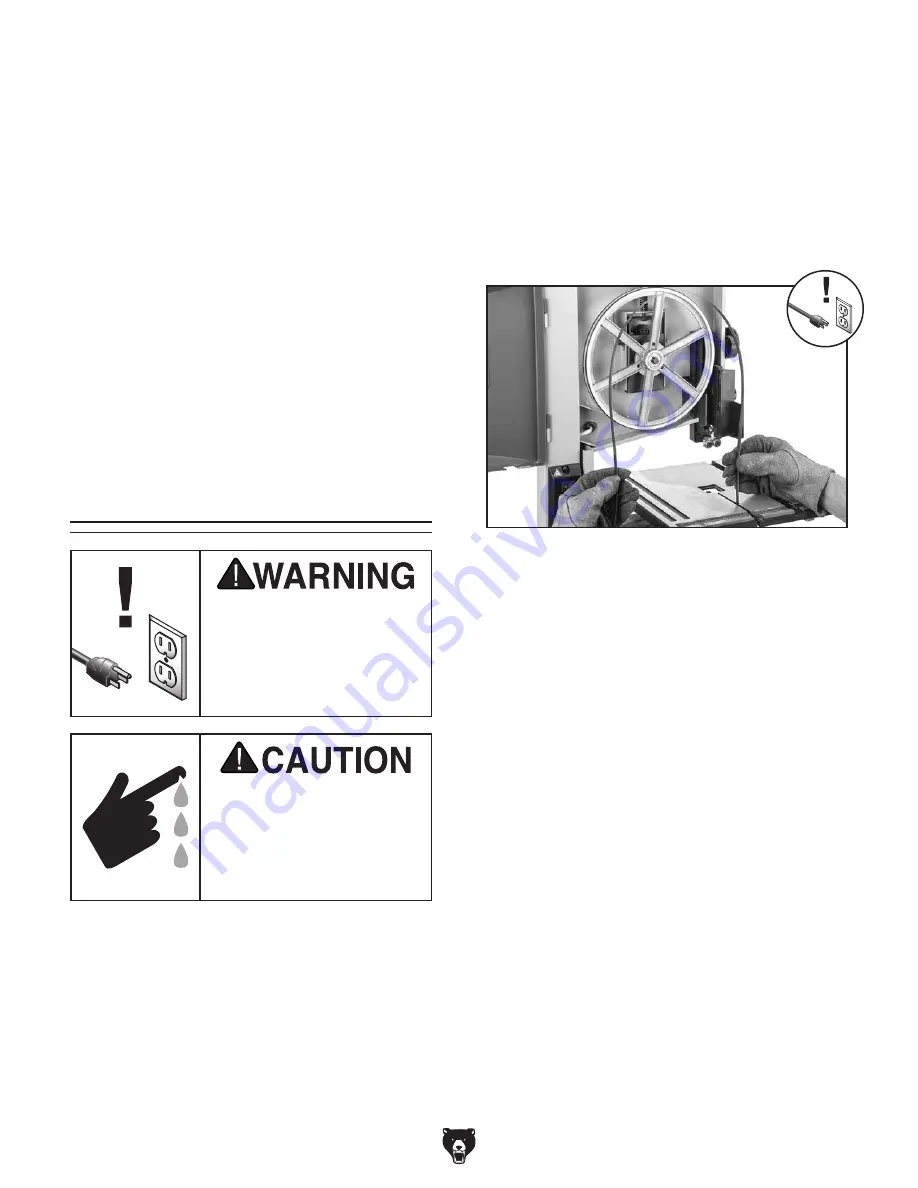
-32-
Model G0803Z (Mfd. Since 12/18)
The most common causes of blade breakage
are:
•
Faulty alignment/adjustment of the guides.
•
Forcing/twisting a wide blade around a short
radius.
•
Feeding the workpiece too fast.
•
Dull teeth or damaged tooth set.
•
Over-tensioned blade.
•
Upper blade guide assembly set too high
above the workpiece.
•
Using a blade with a lumpy or improperly fin-
ished braze or weld.
•
Continuously running the bandsaw when not
in use.
•
Leaving blade tensioned when not in use.
•
Using the wrong TPI for the workpiece thick-
ness. (The general rule of thumb is three
teeth in the workpiece at all times.)
To change the blade:
1. DISCONNECT MACHINE FROM POWER!
2. Move blade tension quick-release lever to left
to release blade tension.
3. Adjust upper blade guide assembly all the
way up, and move blade guides completely
away from blade.
Changing Blade
Disconnect bandsaw from
power BEFORE changing
blade. Serious personal
injury could occur if
machine is started during
this procedure.
LACERATION HAZARD!
Bandsaw blades are sharp
and difficult to handle.
Wear heavy leather gloves
while handling to reduce
the risk of being cut.
Figure 37. Example of removing blade.
8. Position new blade so teeth are facing you
and pointing down in your right hand, then
slide it through table slot.
Note: If the teeth will not point downward
in any orientation, the blade is inside out.
Remove the blade and twist it right-side out.
9. Slip blade over wheels while making sure it
is properly positioned between blade guards
and guides.
10. Engage blade tension quick-release lever,
then tension blade (see
Tensioning Blade
on
Page 21 for details).
11. Adjust blade tracking (see Blade Tracking
on
Page 17).
12. Adjust upper/lower support bearings and
blade guides (see
Adjusting Blade Support
Bearings on Page 22).
13. Close wheel covers and re-install fence com-
ponents removed in
Step 4.
14. Make sure fence is parallel to miter slot and,
if necessary, adjust alignment (see
Page 26).
4. Remove miter gauge, fence, wing bolt, lock
washer, flat washer, and D-nut from table.
5. Open upper and lower wheel covers.
6. Put on heavy leather gloves.
7. Slip blade off of wheels, slide it through table
slot (see
Figure 37), and remove it from
machine.
Summary of Contents for G0803Z
Page 60: ......