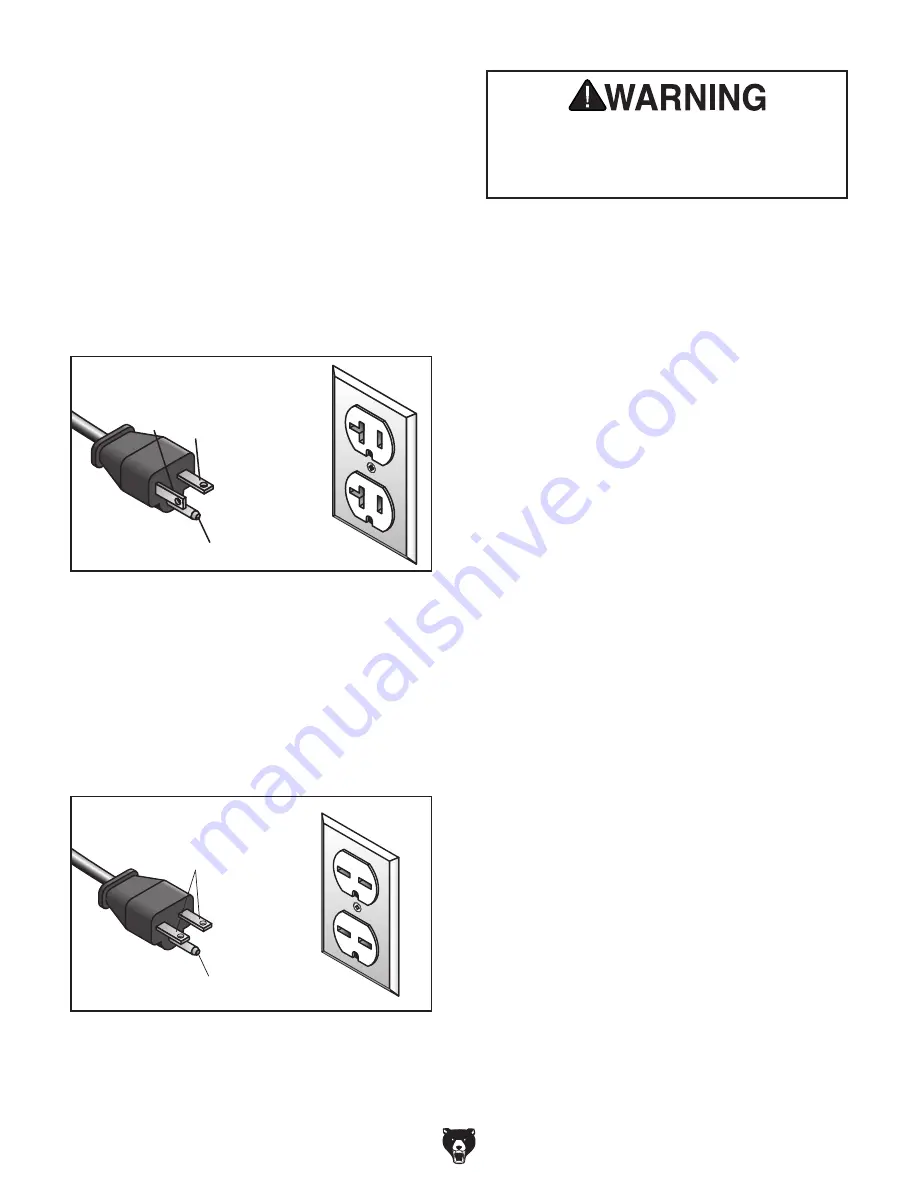
-14-
Model G0899 (Mfd. Since 10/20)
Grounding Requirements
This machine MUST be grounded. In the event
of certain malfunctions or breakdowns, grounding
reduces the risk of electric shock by providing a
path of least resistance for electric current.
Figure 5. Typical 6-15 plug and receptacle.
Grounding Pin
Current Carrying Prongs
6-15 PLUG
GROUNDED
6-15 RECEPTACLE
Figure 4. Typical 5-20 plug and receptacle.
Grounding Pin
Hot
Neutral
5-20 PLUG
GROUNDED
5-20 RECEPTACLE
Improper connection of the equipment-grounding
wire can result in a risk of electric shock. The
wire with green insulation (with or without yellow
stripes) is the equipment-grounding wire. If repair
or replacement of the power cord or plug is nec-
essary, do not connect the equipment-grounding
wire to a live (current carrying) terminal.
Check with a qualified electrician or service per-
sonnel if you do not understand these grounding
requirements, or if you are in doubt about whether
the tool is properly grounded. If you ever notice
that a cord or plug is damaged or worn, discon-
nect it from power, and immediately replace it with
a new one.
Extension Cords
We do not recommend using an extension cord
with this machine. If you must use an extension
cord, only use it if absolutely necessary and only
on a temporary basis.
Extension cords cause voltage drop, which can
damage electrical components and shorten motor
life. Voltage drop increases as the extension cord
size gets longer and the gauge size gets smaller
(higher gauge numbers indicate smaller sizes).
Any extension cord used with this machine must
be in good condition and contain a ground wire
and matching plug/receptacle. Additionally, it must
meet the following size requirements:
Minimum Gauge Size ...........................12 AWG
Maximum Length (Shorter is Better).......50 ft.
Serious injury could occur if you connect
machine to power before completing setup
process. DO NOT connect to power until
instructed later in this manual.
For 115V operation: This machine is equipped
with a power cord that has an equipment-ground-
ing wire and a grounding plug (see following fig-
ure). The plug must only be inserted into a match-
ing receptacle (outlet) that is properly installed
and grounded in accordance with all local codes
and ordinances.
For 230V operation: The plug specified under
“Circuit Requirements for 230V” on the previ-
ous page has a grounding prong that must be
attached to the equipment-grounding wire inside
the included power cord. The plug must only be
inserted into a matching receptacle (see following
figure) that is properly installed and grounded in
accordance with all local codes and ordinances.
Summary of Contents for G0899
Page 92: ......