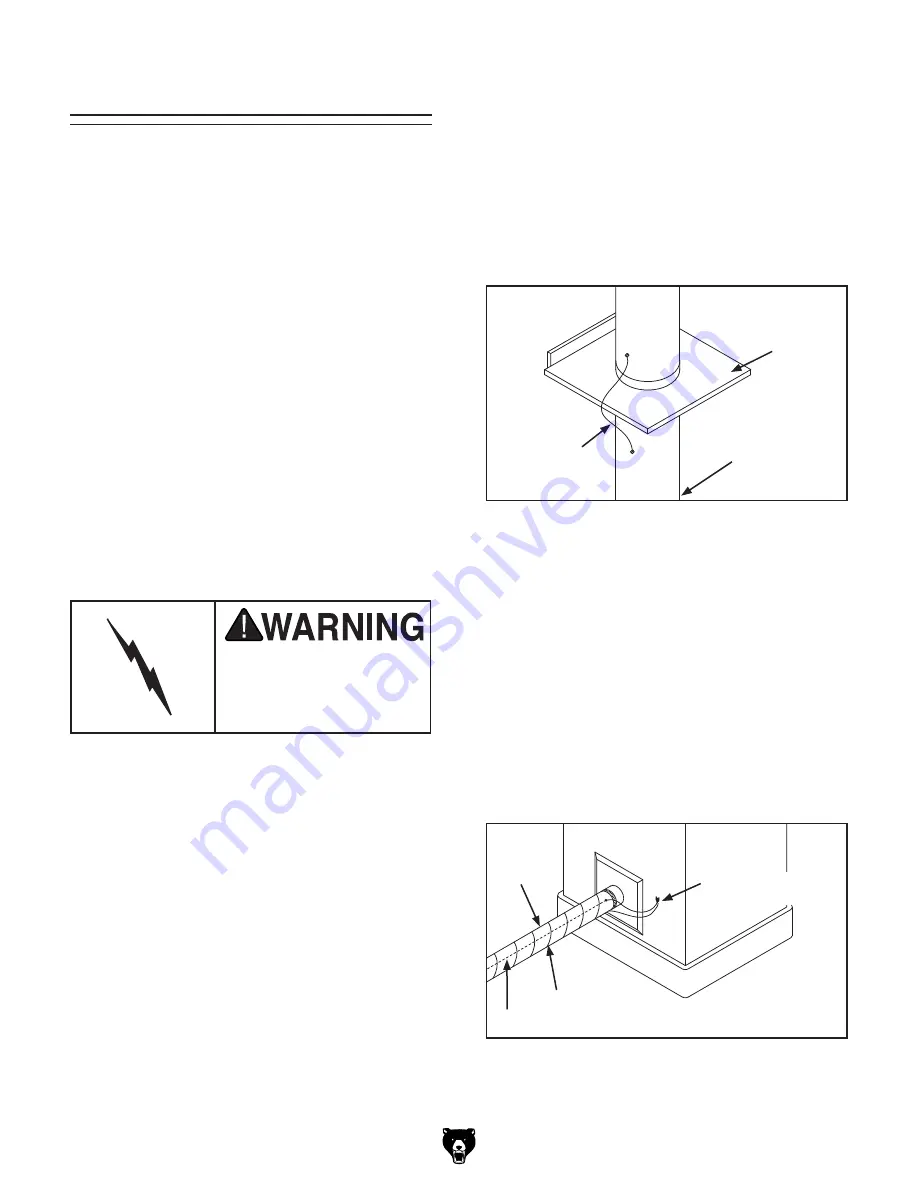
Model G1163P (Mfd. Since 7/15)
-15-
Material Selection
You have many choices regarding dust collection
ducting, but flexible hose is the most common for
this size of machine. However, be aware that there
is a fire or explosion hazard if plastic duct material
is used for dust collection without being grounded
against static electrical charge build-up.
Flexible rubber hose, polyethylene, plastic flex-
hose and other flexible ribbed hose is gener-
ally used for short runs. There are many different
types of flex hose on the market today. These are
manufactured from materials such as polyethyl-
ene, PVC, cloth hose dipped in rubber and even
metal, including steel and aluminum.
If using flex-hose, you should choose one of the
many types that are designed specifically for
the movement of solid particles, i.e. dust, grains
and plastics. However, the cost of specifically
designed flexible duct can vary greatly. Grizzly
offers polyethylene and steel flex hose.
Collection System
Always guard against
static electrical build up
by grounding all dust
collection lines.
Duct Grounding
Plastic flex-hose is an insulator, and dust particles
moving against the walls of the hose creates a
static electrical build up. This charge will build
until it discharges to a ground. If a grounding
medium is not available to prevent static electrical
build up, the electrical charge will arc to the near-
est grounded source. This electrical discharge
may cause an explosion and subsequent fire
inside the system.
To protect against static electrical build up inside
a non-conducting duct, a bare copper wire should
be placed inside the duct along its length and
grounded to the dust collector. You must also
confirm that the dust collector is continuously
grounded through the electrical circuit to the elec-
tric service panel.
Figure 11. Ground jumper wire when using
plastic blast gates or elbows and metal duct.
Plastic
Blast
Gate
Metal
Duct
Copper
Ground
Wire
We also recommend wrapping the outside of all
plastic ducts with bare copper wire to ground the
outside of the system against static electrical build
up. Wire connections at Y’s and T’s should be
made with wire nuts.
Be sure that you extend the bare copper wire
down all branches of the system. Do not forget
to connect the wires to each other with wire nuts
when two branches meet at a “Y” or “T” connec-
tion.
Ensure that the entire system is grounded. If using
plastic blast gates to direct air flow, the grounding
wire must be jumped (
Figure 11) around the blast
gate without interruption to the grounding system.
Attach the bare ground wire to each stationary
woodworking machine and attach the dust col-
lector frame with a ground screw, as shown in
Figure 12. Ensure that each machine is continu-
ously grounded to the grounding terminal in your
electric service panel.
Figure 12. Flex-hose grounded to machine.
Ground Screw
Internal Ground Wire
External Ground Wire
Flex
Hose
Summary of Contents for G1163P
Page 32: ......