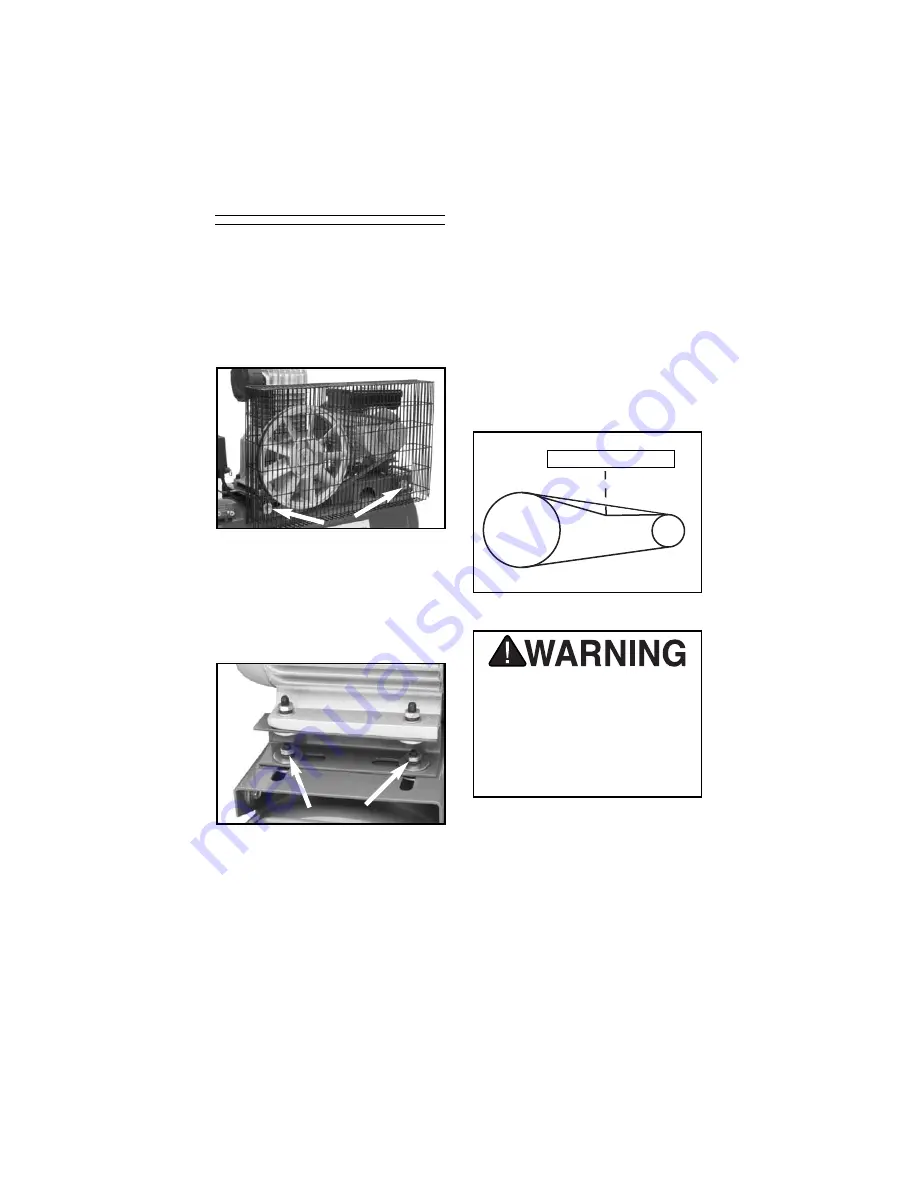
H3372 3 HP Air Compressor
-13
-
Changing V-belt
Make sure the V-belt is properly ten-
sioned. If the V-belt is too tight, the
motor could overheat and cause
machine damage or fire. If the V-belt
is too loose, the belt will slip on the
pulley and cause belt damage and
compressor inefficiency.
Figure 11
. Belt Guard and
mounting bolts.
Figure 12
. Mounting bolt locations.
Figure 13
. V-belt deflection.
To change the V-belt drive on your air
compressor:
1.
Remove the belt guard from the air
compressor shown in
Figure 11.
The
guard is attached to the compressor
frame by the two mounting bolts
shown in
Figure 11.
2.
Loosen the four nuts (one side shown
in
Figure 12
) that secure the motor to
the compressor frame so the motor
can slide towards crankcase, relieving
the tension on the V-belt.
3.
Remove the V-belt from the motor pul-
ley and fly pulley.
4.
Install the new V-belt.
5.
Reposition the motor in its original
place so the belt is tensioned, and
secure the four mounting bolts loos-
ened in
step 2
.
6.
A properly tensioned V-belt will have
about a
1
⁄
2
inch deflection as shown in
Figure 13
.
Replace the belt
guard.
7.
Replace belt gaurd.
1
⁄
2
Inch of Deflection