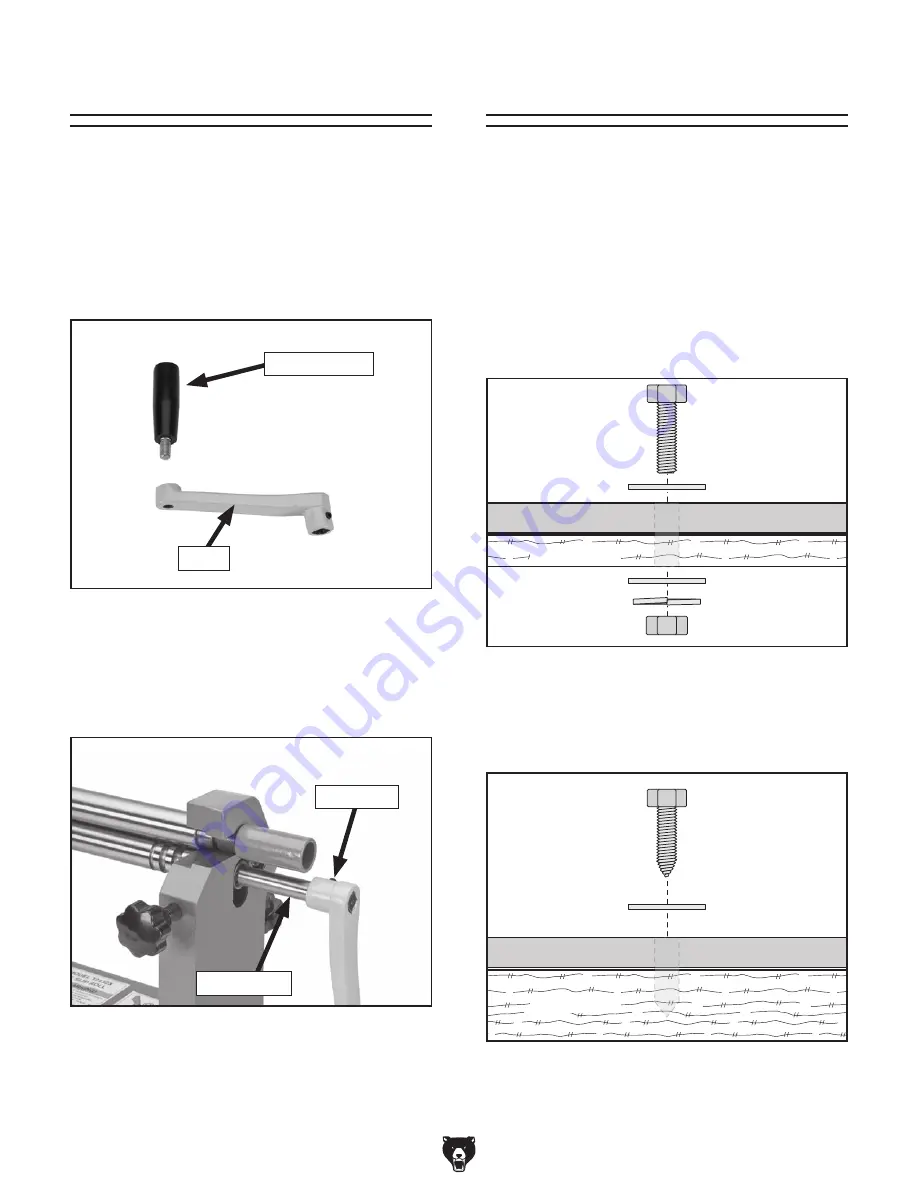
-12-
Model t23103 (Mfg. 12/09 and later)
Mounting
once you have confirmed that your machine is
assembled and functioning properly, mount it to
a workbench through the holes in the base. if
you don't, the machine can tip in use and cause
injury.
the strongest mounting option is a "through
Mount" (see
figure 8) where holes are drilled all
the way through the workbench, and hex bolts,
washers, and hex nuts are used to secure the slip
roll to the workbench.
Machine Base
Workbench
Bolt
Flat Washer
Flat Washer
Lock Washer
Hex Nut
figure 8. Example of a through mount setup.
Machine Base
Workbench
Lag Screw
Flat Washer
figure 9. Example of a direct mount setup.
another option for mounting is a "direct Mount"
(see
figure 9) where the machine is simply
secured to the workbench with a lag screw.
assembly
the Model t23103 comes from the factory almost
fully assembled. all that is required to complete
assembly is to attach the crank and handle.
To assemble your machine:
1. thread the crank handle shown in figure 6
into the small end of the crank and tighten.
figure 6. Crank assembly.
2. Slide the crank onto the crank shaft until the
crank stops against the beveled shoulders of
the shaft. tighten the set screw to secure the
crank in place (see
figure 7).
Crank
Crank handle
figure 7. Crank mounting.
Crank Shaft
Set Screw