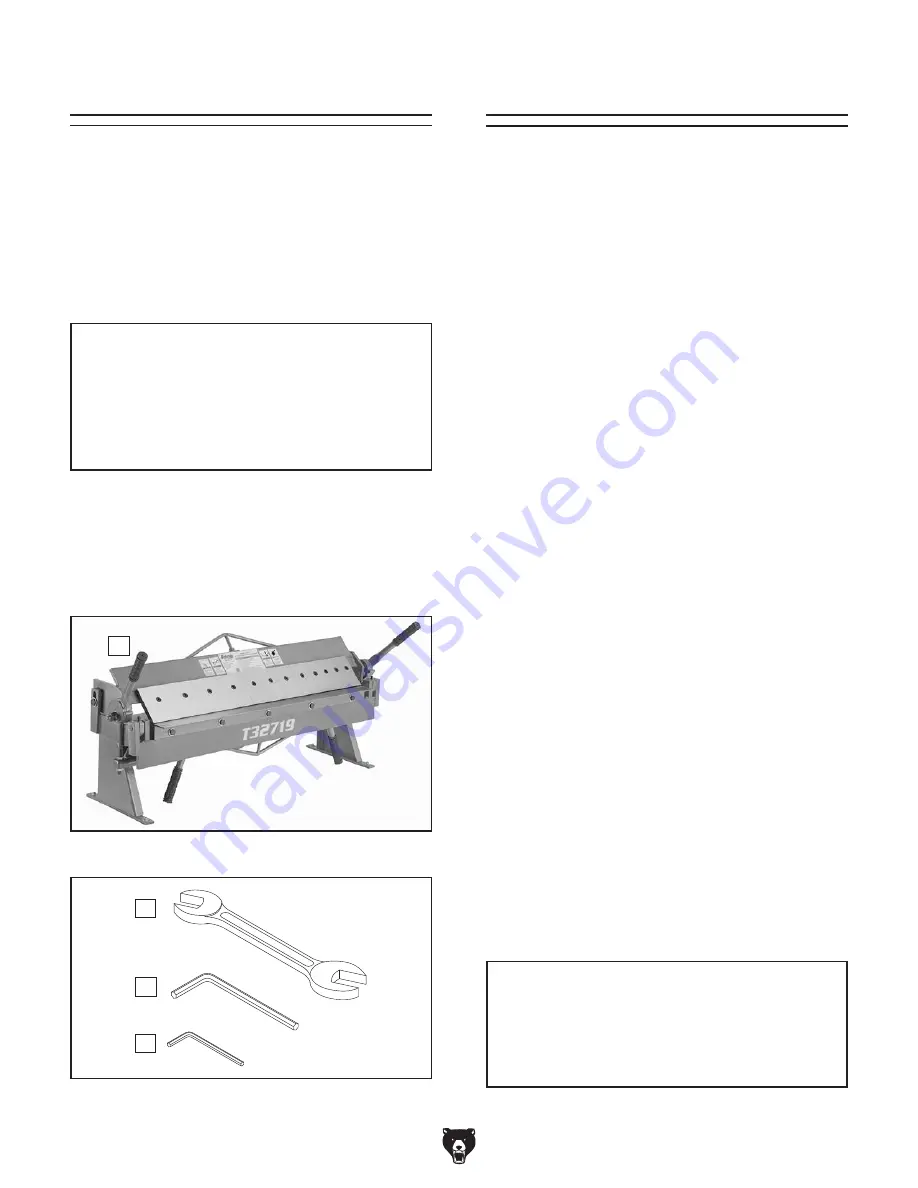
-10-
Model T32719 (Mfd. Since 06/21)
NOTICE
If you cannot find an item on this list, care-
fully check around/inside the machine and
packaging materials. Often, these items get
lost in packaging materials while unpack-
ing or they are pre-installed at the factory.
Inventory
The following is a list of items shipped with your
machine. Before beginning setup, lay these items
out and inventory them.
If any non-proprietary parts are missing (e.g. a
nut or a washer), we will gladly replace them; or
for the sake of expediency, replacements can be
obtained at your local hardware store.
Inventory (Figures 3–4) Qty
A. Pan & Box Brake ........................................ 1
B. Open-End Wrench 17/19mm ...................... 1
C. Hex Wrench 8mm ....................................... 1
D. Hex Wrench 5mm ....................................... 1
Cleanup
The unpainted surfaces of your machine are
coated with a heavy-duty rust preventative that
prevents corrosion during shipment and storage.
This rust preventative works extremely well, but it
will take a little time to clean.
Be patient and do a thorough job cleaning your
machine. The time you spend doing this now will
give you a better appreciation for the proper care
of your machine's unpainted surfaces.
There are many ways to remove this rust preven-
tative, but the following steps work well in a wide
variety of situations. Always follow the manufac-
turer’s instructions with any cleaning product you
use and make sure you work in a well-ventilated
area to minimize exposure to toxic fumes.
Before cleaning, gather the following:
•
Disposable rags
•
Cleaner/degreaser (WD•40 works well)
•
Safety glasses & disposable gloves
•
Plastic paint scraper (optional)
Basic steps for removing rust preventative:
1. Put on safety glasses.
2. Coat the rust preventative with a liberal
amount of cleaner/degreaser, then let it soak
for 5–10 minutes.
3. Wipe off the surfaces. If your cleaner/degreas-
er is effective, the rust preventative will wipe
off easily. If you have a plastic paint scraper,
scrape off as much as you can first, then wipe
off the rest with the rag.
4. Repeat Steps 2–3 as necessary until clean,
then coat all unpainted surfaces with a quality
metal protectant to prevent rust.
NOTICE
Avoid harsh solvents like acetone or brake
parts cleaner that may damage painted sur-
faces. Always test on a small, inconspicu-
ous location first.
B
C
D
Figure 4. Tools.
Cleanup
Figure 3. Pan and box brake.
A
Summary of Contents for T32719
Page 28: ......