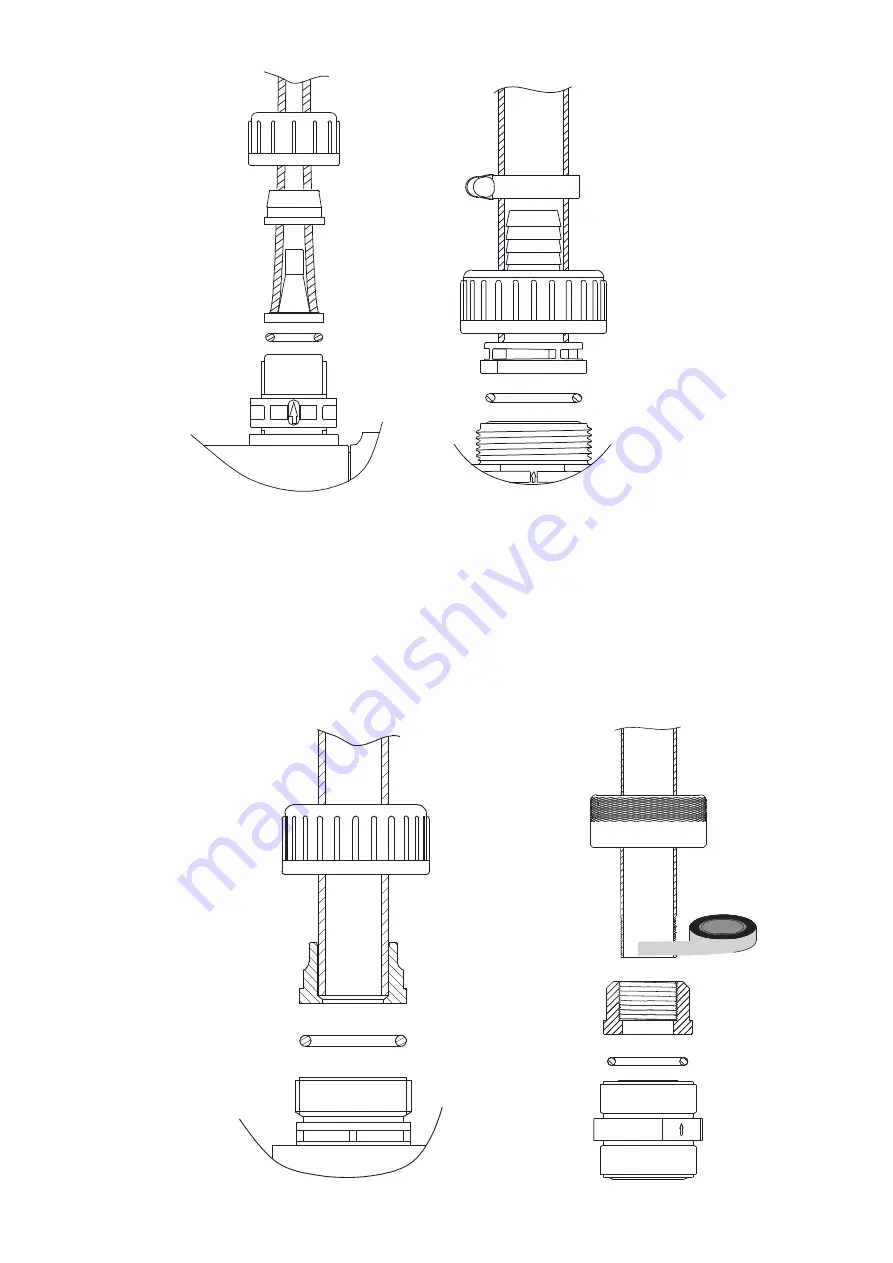
1. Make sure the valve gasket is placed correctly.
2. Push the hose firmly onto the nipple or nozzle.
3. Secure the hose with the connection counterpart or a hose clip.
4. Screw the union nut onto the valve and tighten it.
Related information
• 2.1.1 Installation requirements
2.2.2.2 Connecting pipes
Pipes are to be connected to the valves with a connection piece.
DMX 221 | |
13