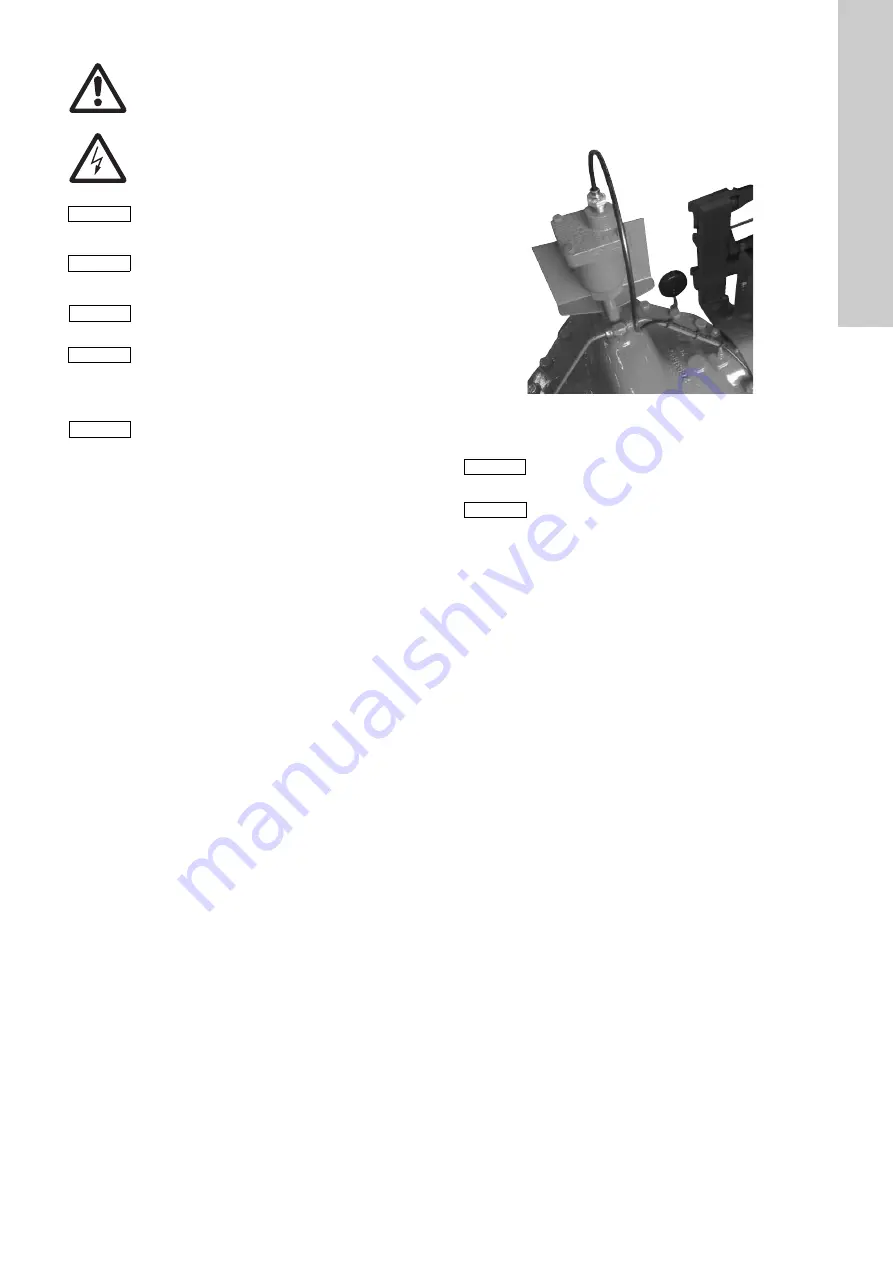
English (GB)
17
8.2 Preparations before commissioning
The below listed preparation actions are valid for applications
with flooded suction conditions.
1. Check that all screws are tight.
2. Check that all pipes and hoses are installed correctly.
3. Check all electrical connections.
4. Check that all fuses in the control cabinet are switched on.
5. Check the alignment of the coupling. See section
6. Check that the coupling guard is installed correctly and that all
screws are tightened to 10 Nm for M6 and 25 Nm for M8.
7. Check that all safety devices are installed.
8. Make sure that any storage tank and pump priming tank are
filled with water.
9. Set the pressure switches according to the instructions.
System pressure minus 0.5 bar can be used as a reference
value.
10. Open the isolating valves on the suction and discharge sides.
The static geometric suction pressure from the main water
tank will fill the suction pipe, discharge pipe and pump with
water.
11. Bleed all air from the pump casing and suction pipe by the
opening of the automatic relief valve at the top of the pump.
Rotate the shaft a few times if possible to evacuate any air
trapped inside the impeller passages.
12. Close the isolating valves on the suction and discharge sides.
Fig. 29
Air relief valve
8.2.1 Pump set with diesel engine
1. Check the V-belt tension.
2. Check the oil level and refill, if necessary.
3. Check the level of coolant and refill, if necessary.
4. Check that all hose connections in the cooling circuit are tight
and leakage-free.
5. Fill the fuel tank with diesel fuel and vent the fuel pipes.
Warning
Commissioning must be carried out by authorised
staff.
Warning
The control cabinet of the controller must remain
closed during commissioning.
Caution
Do not start the pump until it has been filled with
water and vented.
Caution
The pump must not run against closed valve as this
may cause an unacceptable temperature increase or
the formation of vapour.
Note
See also installation and operating instructions for
the controller.
Caution
You must not change the engine speed setpoint
(rpm).
Note
Pump set with Clarke diesel engine:
We recommend that you register the diesel engine
before startup. Otherwise, Clarke cannot provide any
warranty if the engine is faulty. Go to
www.clarkefire.com: SERVICE, PARTS &
WARRANTY.
T
M
06
24
9
1
43
1
4
Caution
Check the level of oil and coolant in the engine prior
to startup.
Note
See installation and operating instructions for the
diesel engine.