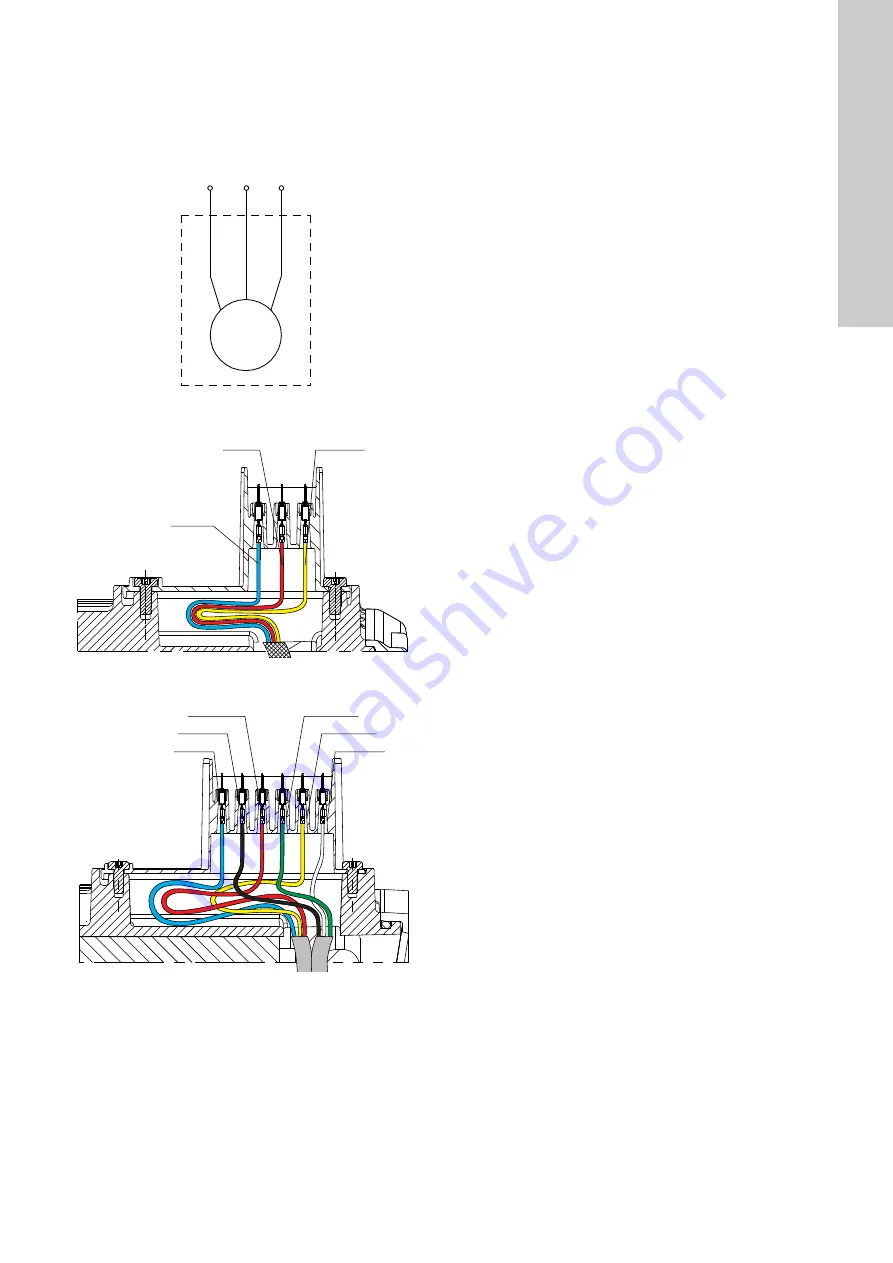
English (GB)
27
9.5 Winding resistance
As the motor is star-connected, the easiest way to measure the
winding resistance is to measure across two phases. Measure at
the coil temperatures stated in the table below. It may be
necessary to let the motor cool off if it has been running or if it
was stopped because of short circuit or overload.
Wiring diagram
Fig. 65
Wiring diagram
Fig. 66
Measure the winding resistance
Fig. 67
Measure the winding resistance
TM
05
70
25
04
13
TM
06
77
22
39
16
T
M
06
7
7
2
3
39
16
~
U1
V1
W1
U1 - Blue
V1 - Red
W1 - Yellow
U1 - Blue
V1 - Red
W1 - Yellow
U1 - Blue
W2 - Black
V1 - Red
U2 - Green
W1 - Yellow
V2 - White
Summary of Contents for MGE 100
Page 1: ...MGE and MLE model J Service instructions GRUNDFOS INSTRUCTIONS ...
Page 2: ...2 ...
Page 30: ...English GB 30 10 Exploded view Fig 68 MGE model J MGE 132 TM06 6857 2516 ...
Page 32: ...32 ...
Page 33: ...33 ...
Page 34: ...34 ...