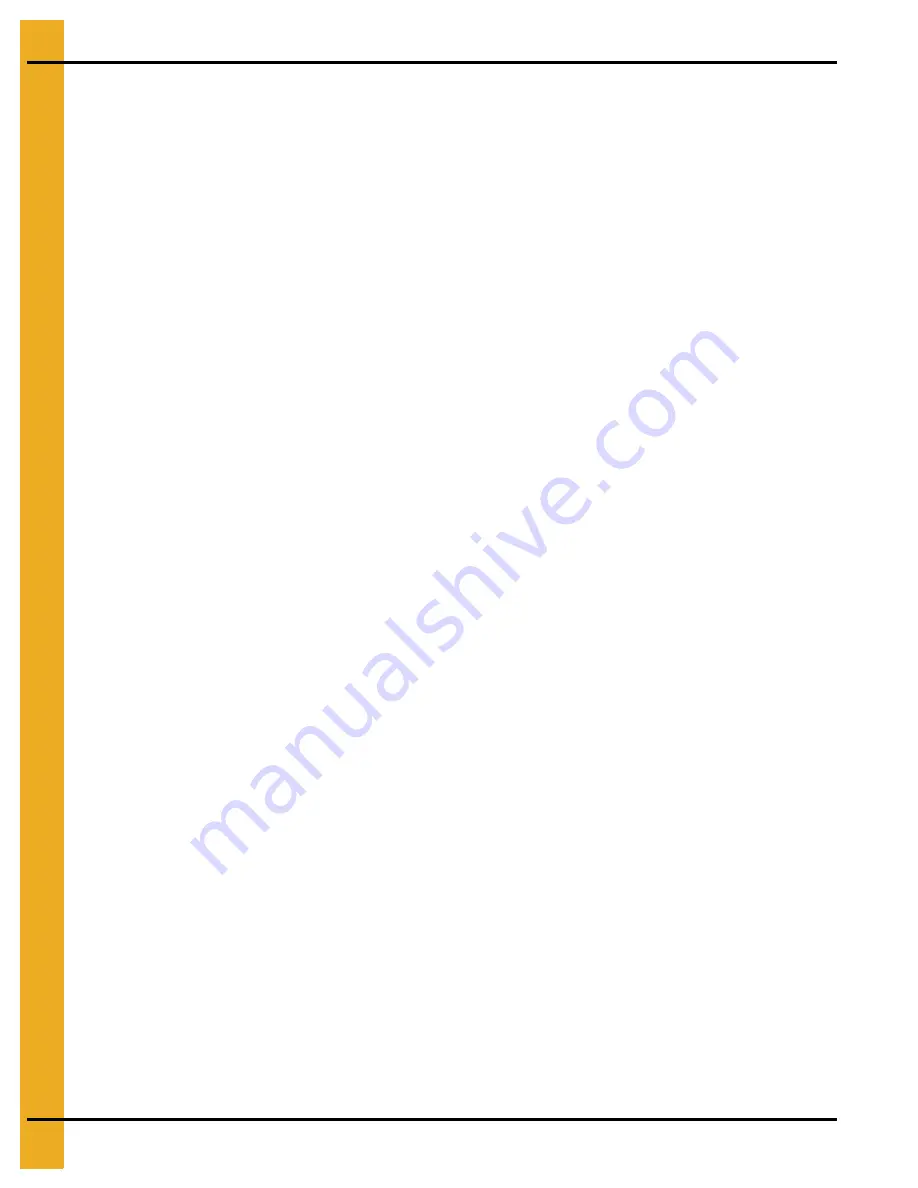
20
PNEG-681CE
CE Compliant Series II Bucket Elevator
5. Bucket Elevator Foundation
1. The Bucket Elevator foundation must be designed by a qualified civil engineer and installed by a
qualified contractor.
2. Always consider the additional weight of live loads, dead loads, wind loads and soil bearing loads.
3. Always provide for proper moisture run-off on the top of the foundation.